

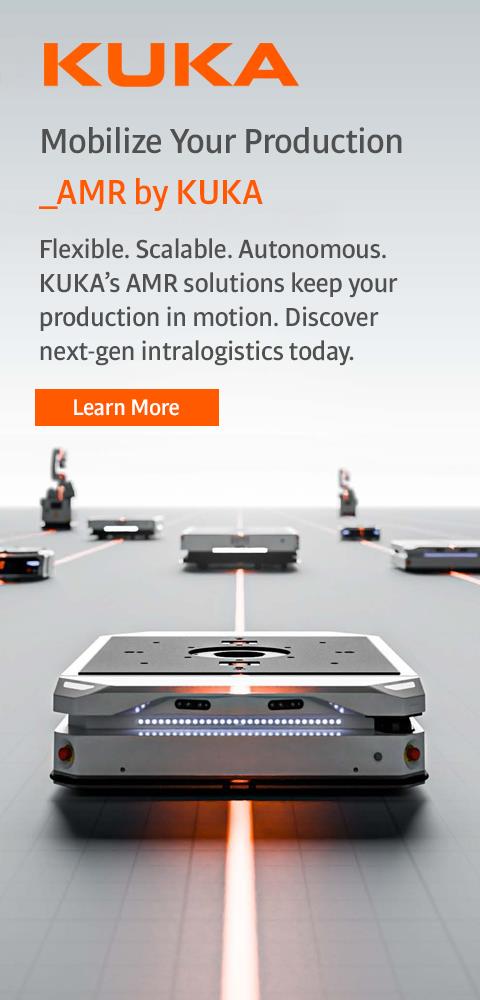
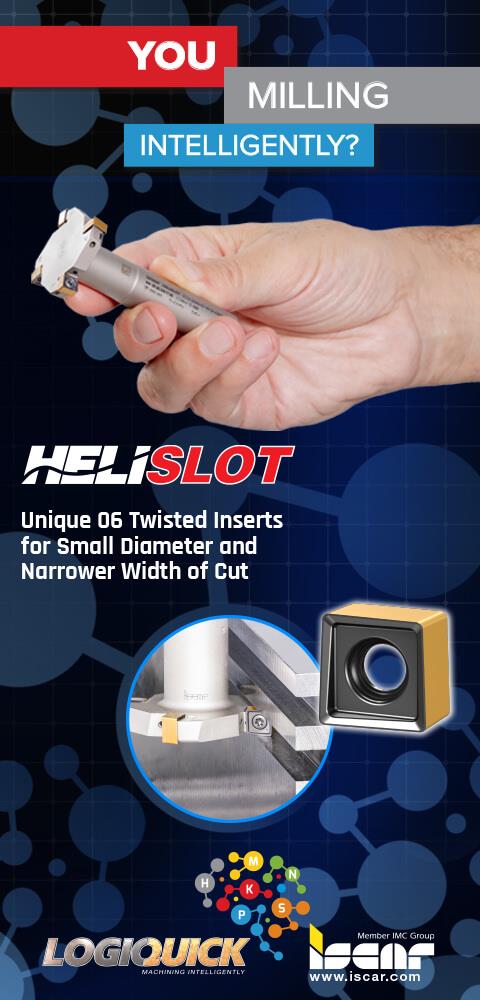
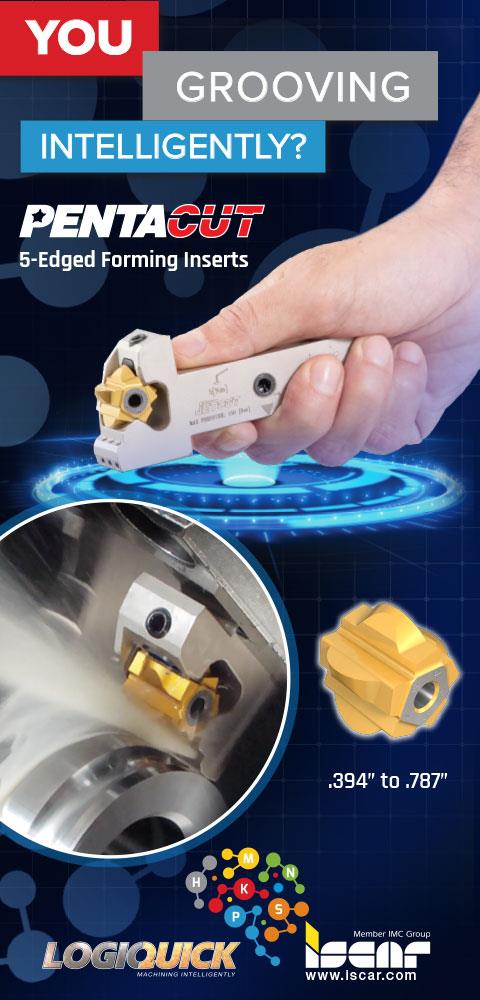
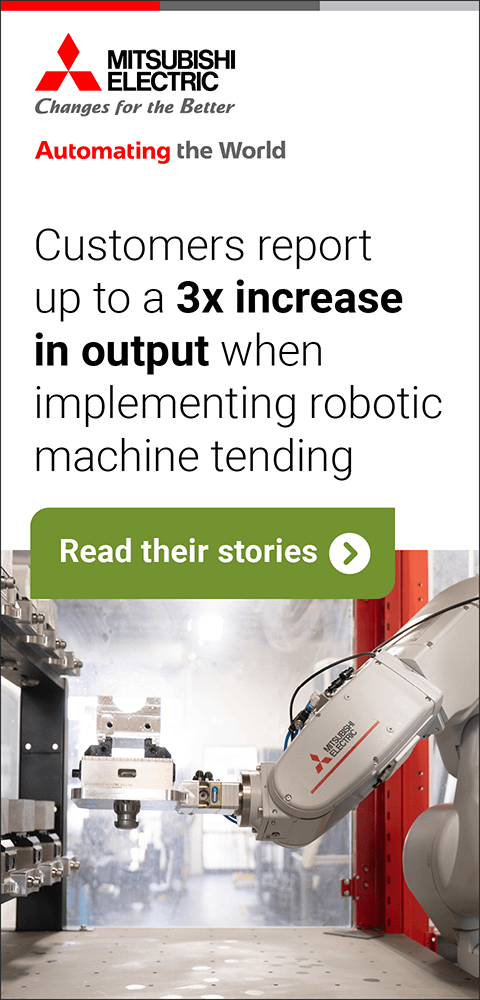
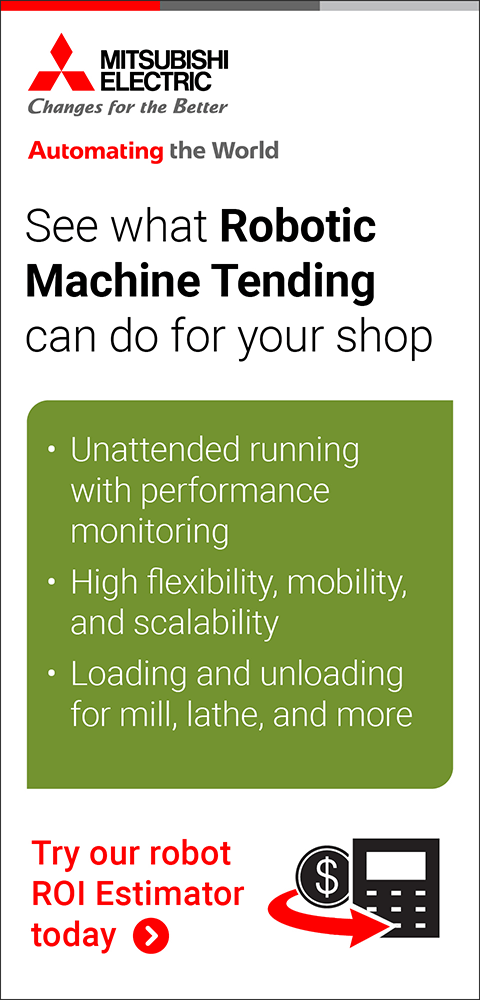
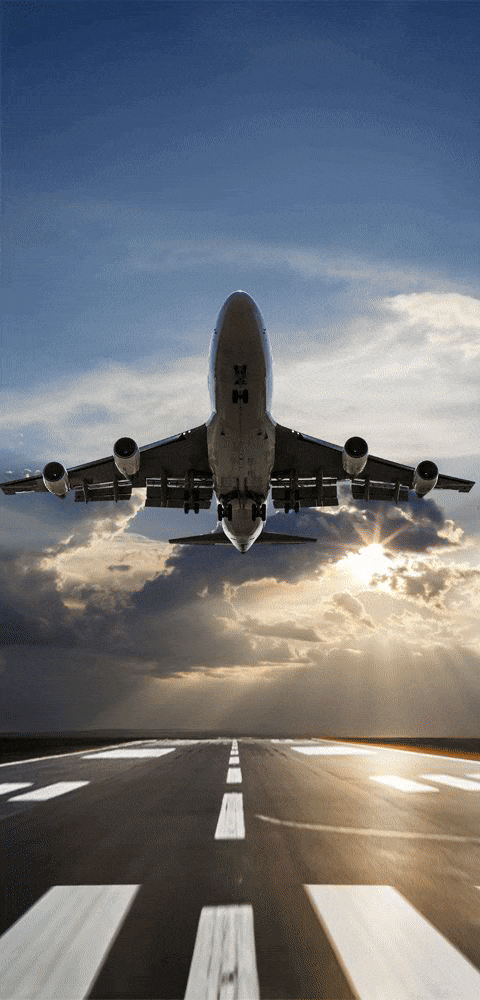
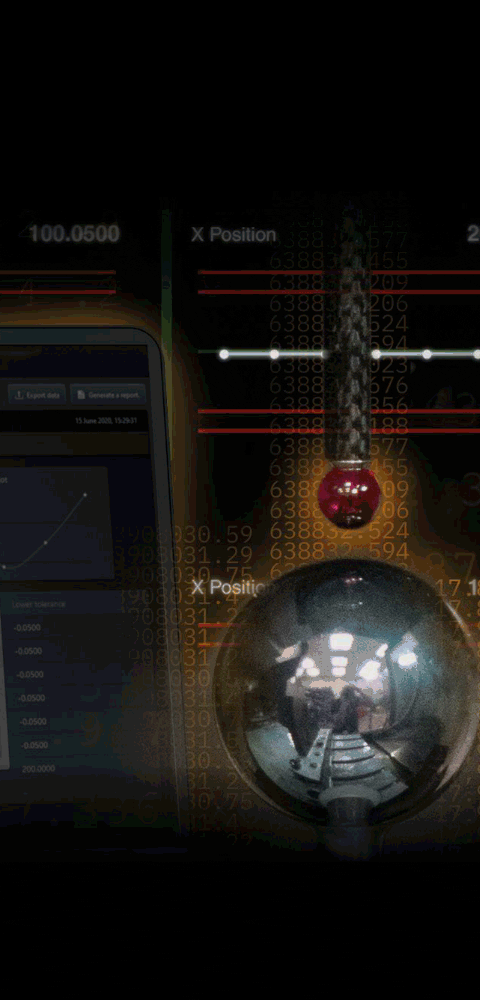
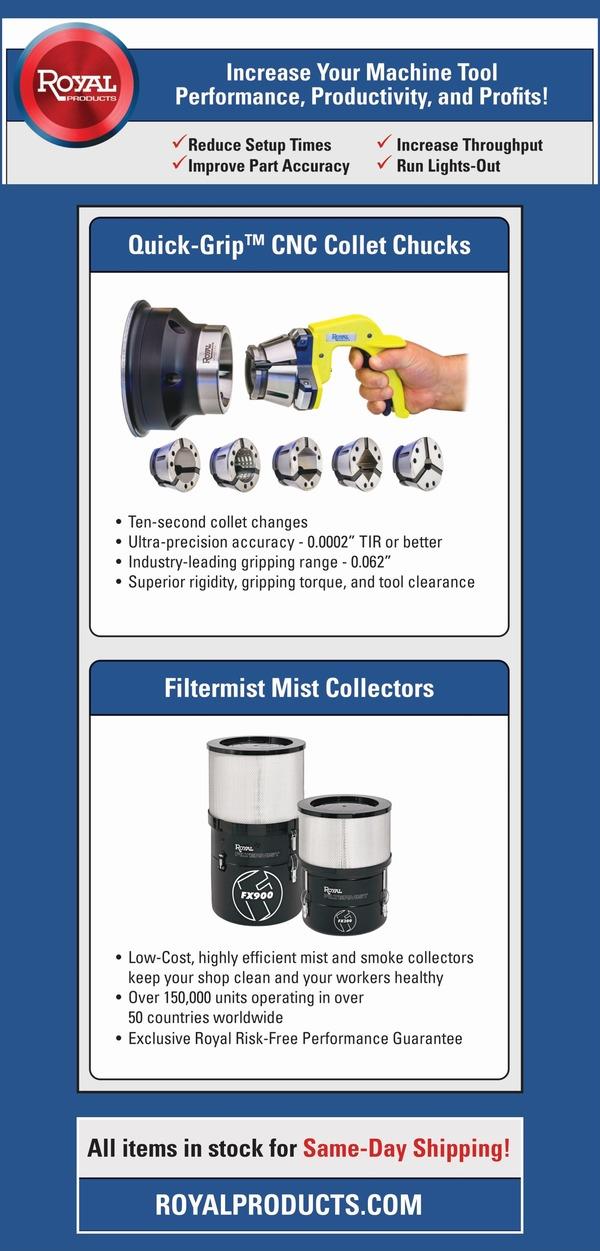
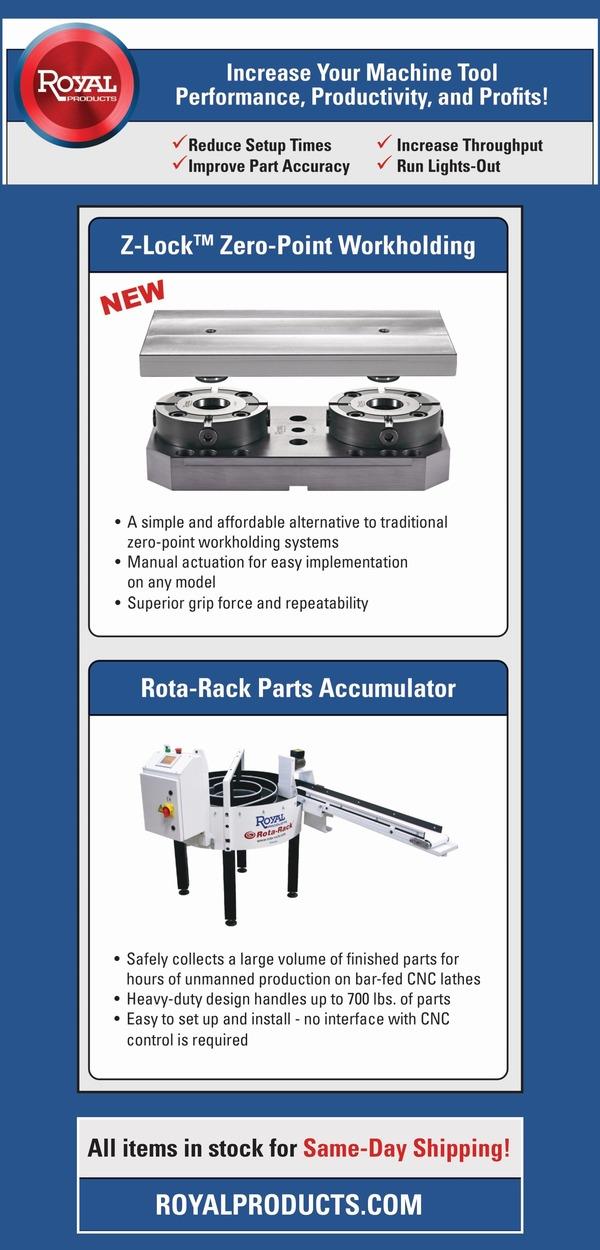
Spindle Error Analysis Made Easier for Fixed Spindles
May 1, 2014
"Lion Precision's spindle Error Analyzers (SEA) are used for testing and qualifying machine tool spindle performance, as well as qualifying spindles after rebuild and before shipment," said a company spokesperson. "But the spindles are in a fixed test stand, making it difficult to adjust the relative position of the spindle and the SEA probes. A 3-axis stage has been introduced to solve the problem. The 3-axis stage includes a top plate with mounting holes that mate to SEA probe holders. SEA users can attach their probe mounting system to the 3-axis stage. The stage can be located in approximate position relative to the spindle in the test stand then precisely adjusted in all three axes."
The SEA system includes high-resolution noncontact capacitive displacement sensors, precision probe mounts, precise masterball targets with less than 100 nm of roundness error, temperature sensors and software to acquire and analyze the measurements. Results are presented in polar or linear plots and values are listed for synchronous and asynchronous errors, TIR and more. Spindle displacement can be plotted against temperature and RPM to show critical relationships between these variables.
"Because so many precision machining operations are now using SEA to test their spindles, and also want to test spindles while in the test stand, we felt compelled to help make that task easier," said Don Martin, Lion Precision's President. "The precision nature of the system requires that the probes be located near the master balls which are mounted in the spindle for the test. The probes must be located at the proper distance +/- about 50 um from the master ball. Positioning like that takes a very steady hand. This new 3-axis stage system makes it easy."
For more information contact:
Lion Precision
563 Shoreview Park Road
St. Paul, MN 55126
800-250-9297 / 651-484-6544
info@lionprecision.com
www.lionprecision.com
< back