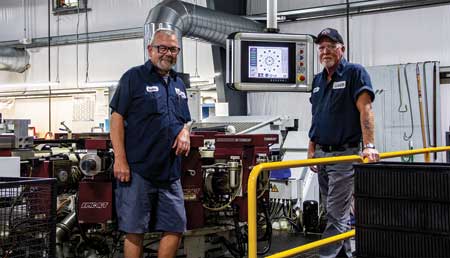
(l-r) Steve Pines, Machine Operations Manager, and Jerry Coy, Facility Machining Manager, with the EPIC R/T 25-12 rotary transfer machine.
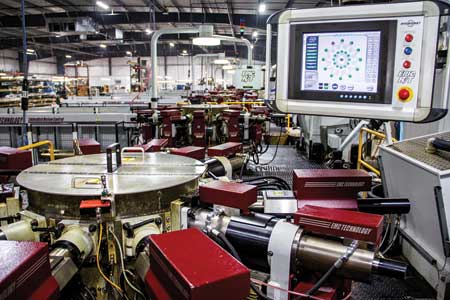
Alkon's successful integration of Hydromat technology enhances its manufacturing efficiency, reduces waste and strengthens its market leadership through a strong focus on customer satisfaction and continuous improvement.
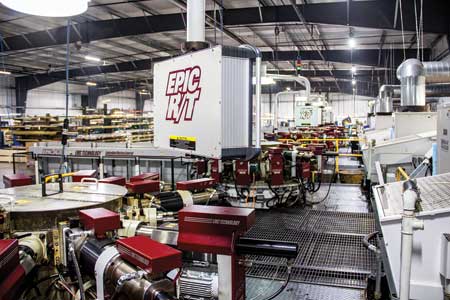
The first of five EPIC platforms on Alkon's production floor.
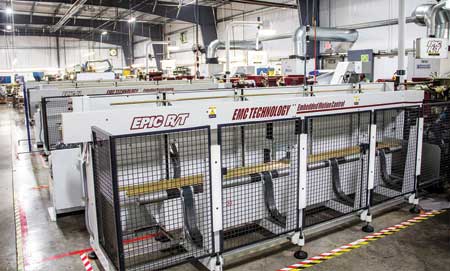
The EPIC R/T equipped with a bundle bar feeder.
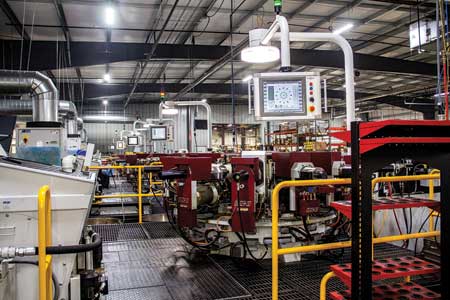
A glimpse into the state-of-the-art manufacturing line at Alkon.
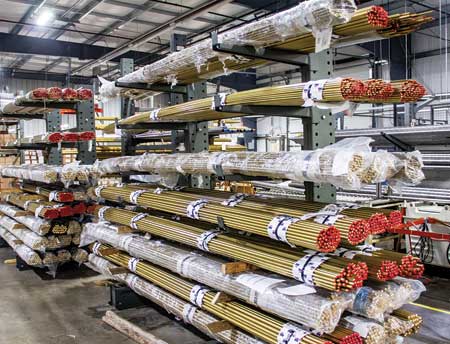
Alkon's bar stock inventory ready for use in its Hydromat machines.
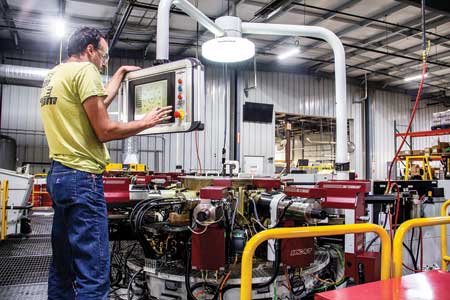
Matt Miller, Hydromat Department Lead, with the EPIC R/T.
In the modern era of precision machining, businesses are consistently seeking ways to enhance quality, streamline processes, minimize waste and lower overall costs. To achieve these objectives, companies need access to advanced technologies and tailored solutions that align with their specific requirements. As a privately held company for over four decades, Alkon Corporation understands the significance of prioritizing ongoing advancements.
Alkon Corporation is a provider of high-quality valves, fittings and cylinders in the industrial and mobile sectors. Alkon not only has its own product line, but also features Star Hydraulics, AIRman and Allenair. The brand has over 250 nationwide distributors, multiple OEMs and a production plant in Mexico.
"Alkon Corporation has continuously met the needs of its customers by offering a wide range of reliable products designed to enhance efficiency and safety in various applications," said a company spokesperson.
The process of moving through Alkon's production begins at its Fremont, OH, plant, which covers an expansive area of 60,000 sq. ft., a significant growth from its initial size of 7,000 sq. ft.
The factory runs around the clock, churning out 60,000 parts daily and 15 million annually with its complex machinery. Within its walls, machining, part washing, thread sealing, assembly and testing come together to create the end product. Alkon specializes in the production of over 10,000 parts crafted from materials such as aluminum, brass, stainless steel and engineered composites.
This entire process is overseen by a team that has expanded significantly from a small start-up single-line company in Hawthorne, NJ, in the mid-1950s. Alkon initially focused on pneumatic cylinders before expanding into air-powered drill units and hydraulic controls. Named after its founder, Al Konviser, the company diversified over the years, introducing the A Series pneumatic valves in 1964 and later the J Series, securing patents for these products. Through the 1970s and 1980s, Alkon broadened its offerings with new valve series and fitting designs after launching the first all-brass AQ push-to-connect fittings in 1981, and a similar product for the DOT industry in 1990. Ownership transitioned to the Winter family and other stakeholders, maintaining a strong position in the industry after selling its original cylinder business in 1985.
In 1991, Alkon initiated operations in Fremont, OH, and by 1999 had completed its move from New Jersey. The company broadened its valve offerings in 2001 by acquiring ISI Fluid Power and introducing the TransDOT series valves, designed to endure the rigorous conditions of the DOT industry. A significant step was taken in 2012 when Alkon acquired a majority stake in Star Hydraulics, a provider of premium hydraulic pumps and cylinders. Alkon has consistently engaged in production activities in Mexico, culminating in the full acquisition of Alkon Products, S.A de C.V in 2013.
In 2016, Alkon introduced the PAQ composite fitting line, patented and launched shortly thereafter, which combines the durability of brass with the lightweight advantage of composite materials. Following its acquisition of Allenair in 2017 and moving its production to its Fremont facility, Alkon enhanced its industrial offerings with premium cylinders and valves. By fully acquiring Star Hydraulics in 2020, Alkon optimized its production efficiency and product delivery for customers.
The purchase of Airman Products in 2022, previously a key competitor, broadened its DOT valve range and manufacturing capabilities in Brighton, MI. Today, Alkon operates from Fremont, OH, Chicago, IL, Brighton, MI, and Mexico City, MX, adhering to a vertically integrated manufacturing model that ensures control over quality and manufacturing, minimizing downtime for customers.
Revolutionizing Manufacturing Efficiency with Rotary Transfer Technology
At its Freemont plant, Alkon Corporation has acquired 15 screw machines to manufacture one part family, including 10 distinct sizes, achieving an annual production capacity of 5-6 million, its "bread and butter" fitting component.
This product presented the company with several challenges to overcome. The process involved six steps before they could fully assemble the part, demanding the need for lots of manpower. This intricate process involved the use of seven outdated pieces of secondary equipment, resulting in delays within the assembly department due to production wait times, and creating a prolonged quality inspection process, rather than a single check. This complicated the process of meeting delivery deadlines for customers. With readiness for change and a strong desire for improvement, the ownership team, along with other management positions, knew they needed the next level of lean manufacturing principles implemented in their production.
A big challenge was deciding which machine they were going to invest in. "We looked at several screw machines and knew Hydromat would be the best bet because it was straightforward. With the Hydromat, we do one operation, wash it and it is complete," said Steve Pines, Machine Operations Manager. Pines was a driver in the decision for the Hydromat platform.
The implementation of Hydromat machining in the production process of its proprietary bread and butter part was a significant achievement in Alkon's history. Now its line of machines includes five Hydromats and various other machine tool equipment, such as Davenports and other screw machines.
The first EPIC R/T 25-12 rotary transfer was successfully installed in December 2014, followed by the second in April 2015 and the third in February 2016. By 2019, an additional two EPIC II 25-12 rotary transfer machines were purchased and delivered, enhancing their manufacturing capabilities.
Introducing intricate machinery came with a slight learning curve. "There were some growing pains with introducing Hydromat," said Pines. "One of the big things is, we were not just buying a machine; we were buying a long-term solution process. A significant part of our adjustment involved familiarizing ourselves with manufacturing the part through a different process." Demonstrating tangible results and ensuring the production met the anticipated capabilities proved crucial for success.
Jerry Coy, Facility Machining Manager with 11 years of Alkon experience, discussed his journey of progression from traditional screw machines to contemporary EPIC machinery. Embracing a shift away from the familiar practices that had defined his career presented its own set of obstacles. However, with the backing of Hydromat, he tackled the learning curve with assurance: "At that time of the introduction to Hydromat, I was a repair guy," he said. "I got moved into supervision and then I moved into management, so now I am looking at the production numbers. I would not have anything but Hydromats for the production that we are running. Comprehensive training during the machine runoff coupled with ongoing support from set-up technicians facilitated a seamless transition."
Strong support has been the foundation of this partnership. Alkon's regular interactions with Hydromat's customer service demonstrate a transparent line of communication. Coy noted the importance of Hydromat's 24/7 support, which provides swift resolution to any challenges.
By incorporating Hydromat technology into its manufacturing processes as well as lean manufacturing methodology, Alkon is now achieving around 85% efficiency.
For more information contact:
Alkon Corporation
728 Graham Drive
Fremont, OH 43420
419-333-7000
www.alkoncorp.com
Hydromat, Inc.
Morgan Nelms
11600 Adie Road
St. Louis, MO 63043
314-432-4644
mnelms@hydromat.com
www.hydromat.com