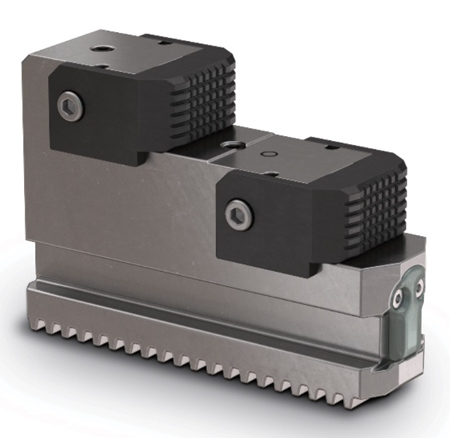
iJaw as a console jaw with exchangeable clamping inserts and two clamping stages
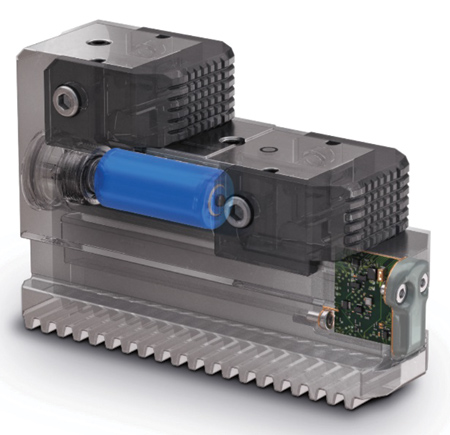
Sensor technology for clamping force measurement and electronics for wireless data transmission via IO-Link Wireless, as well as a rechargeable battery inside the iJaw.
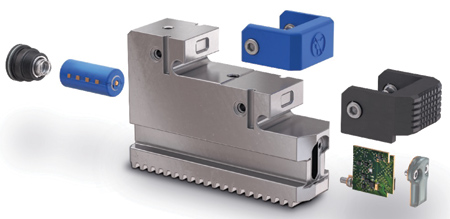
Components of the iJaw
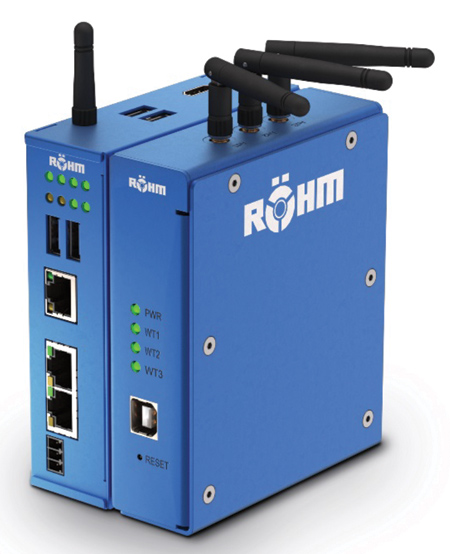
The gateway receives the data from the iJaw via the IO-Link Wireless protocol. Via Profinet, the data is available directly at the machine control system for display on the HMI, or for further processing for process control. The data can be sent via LAN to the Cloud and used for visualization, documentation or analysis.
ROHM has introduced the iJaw, a clamping force measuring jaw.
"This ground-breaking product solves the problem for which there has been no accepted industrial solution up to now: the clamping force is usually set by the operator of the machine tool, and is solely based on experience," said a company spokesperson. "Errors during machining due to incorrectly set clamping force are therefore embedded in the process, well before the operator presses cycle start."
The spokesperson continued, "Even on today's most advanced and modern machine tools, workpieces are clamped the same way they were a hundred years ago: the operator clamps 'by feeling.' Due to the lack of sensors, the machine tool can only support the operator to a limited extent. To ensure that workpieces are clamped correctly-since no one wants to risk ejection or waste-the clamping force is often set too high. On thin-walled aerospace, medical or watch components with sensitive surfaces, this can quickly lead to deformation or crushing."
The iJaw integrates sensor technology for clamping force measurement as well as data transmission in a complete, self-contained clamping jaw. There is a clamping insert a few millimeters thick between the sensor and the workpiece. The iJaw transmits the measured data to a gateway via the robust IO-Link wireless protocol with a high sampling rate of 100 Hz. This means the iJaw measures in real time during machining. It has a suitably robust hardened steel and waterproof (IP 68) design. The transmitting antenna has a cover made of high-temperature plastic to protect against chips.
"With the iJaw, ROHM eliminates virtually all factors that lead to inaccurate or improper clamping of the workpiece," said the spokesperson. The measurement takes place directly at the clamping point to the workpiece; the data transmission to a gateway is done by the industry standard IO-Link Wireless. The gateway can be connected to the machine control system via the integrated LAN interface.
The iJaw can be mounted and used on all lathe chucks with a similar jaw interface, like any standard jaw. The iJaw is available as a stepped jaw for lathe chucks with straight or helical serrations in sizes 215, 260 and 315. Suitable chucks from the ROHM lineup are DURO-A RC, DURO-NCSE, DUR\O-NC power chucks with the quick-change jaw system, as well as the DURO-T manual quick change jaw chuck. To adapt the jaws to different workpiece geometries, there are various exchangeable hard and soft clamping inserts that are locked onto the jaw with screws.
Product Applications and Benefits
"We have identified eight different scenarios in which the iJaw offers significant added value," said the spokesperson. "The first three scenarios are about monitoring clamping forces before and during machining."
Before machining, the iJaw assists in loading workpieces and setting up the clamping system. If errors occur, the measured clamping force deviates from the target values, and a manual or automated reaction can be initiated. During machining, clamping forces that are too high (risk of damage to the workpiece) or too low (insufficient clamping force up to ejection of workpiece) can be detected, and an adjustment can be performed.
Three further scenarios offer solutions for the evaluation of series and serial measurements. Here, changing clamping forces can be used to detect trends at an early stage. This includes the early detection of upcoming maintenance to maintain the clamping force or the wear of tools. Rejects can already be identified in the machining process, i.e., during their manufacture.
"A very exciting application is in automation processes, where the iJaw provides part presence confirmation without the need for pneumatics," said the spokesperson. "Another benefit offered only by the iJaw is the documentation. This is highly valuable for components requiring documentation-such as in aerospace technology-and product and process optimization tasks. If a manufacturer wants to understand how a component was previously manufactured, they can research the manufacturing environment in the data stored in the Cloud. The iJaw archives the fingerprint of the machining process, so to speak."
For more information contact:
ROHM Products of America
2500 Northlake Drive
Suwanee, GA 30024
770-963-8440
sales@rohm-products.com
www.rohm-products.com