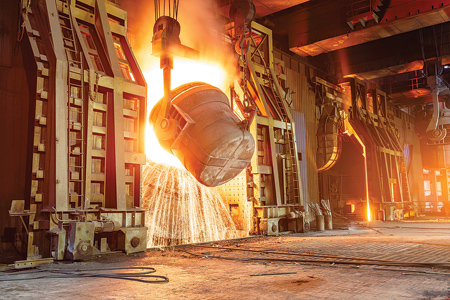
Pouring molten metal into a holding furnace.
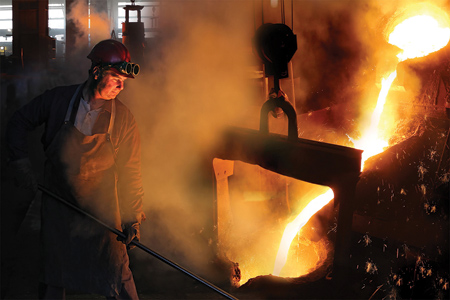
The beginning of the casting process.
One of the largest grey iron foundries in the Southern Hemisphere needed to reduce shipped defects in truck engine blocks. Each year, this foundry produces well over 100,000 high-quality cast iron automotive components (truck engine blocks) at its plant-or nearly 55,000 tons.
For this global foundry, the challenge was to improve quality to reduce the cost of scrap. The average scrap and rework rate was 6%. Every defective unit shipped and scrapped incurred waste, time and a relatively high shipping cost and penalty payments.
The level of complexity-from the large number of non-linear causal relationships in a modern foundry process-makes significant production gains difficult. According to the CEO of this foundry, improvements to the production line from traditional engineering practices had hit a ceiling. An avalanche of information translated into millions of possible combinations of plant states, which process engineers could not possibly consume-let alone analyze, contemplate and act on timeously and with certainty.
To address this challenge, DataProphet was contracted to deploy its AI-as-a-Service. The projected outcome was a reduction in internal and external defects, hence lower scrap rates. In turn, this would increase production capacity while avoiding rework, improving overall equipment effectiveness (OEE) and reducing waste and energy usage. The solution was strategically designed to contribute to the sustainability goals of the foundry.
DataProphet PRESCRIBE
The solution-DataProphet PRESCRIBE-functions as an AI-led tool deployed in a factory's existing data infrastructure. After building a digital unified view of a complex manufacturing process, PRESCRIBE harnesses its AI algorithms. These algorithms proactively automate optimal operating regimes for an actual production line. They achieve this with a combination of input from historical and live production data-accounting for both process variables and quality metrics.
Deep Learning models encapsulate the correlations and interactions of a specific manufacturing process and deliver prescriptions to operators to modify setpoints. In this way, factories can meet non-quality challenges with data-led prescriptions to prevent anomalies and optimize the production process. This AI-as-a-Service for manufacturing is provided according to agreed KPI benchmarking for a particular product or component.
According to a spokesperson, reasons for selecting PRESCRIBE include:
- PRESCRIBE is able to handle the high level of complexity in the foundry process.
- PRESCRIBE does not require additional hardware investment. It works with the existing data infrastructure of the plant.
- DataProphet offers indefinite post-installation support and full-model maintenance with weekly reports. This means clients are guided, updated (and the product maintained) at every step of the digital transformation journey.
DataProphet simultaneously implemented the extraction, transformation, loading and warehousing of plant-wide data. Historical production data was gathered from stakeholders across multiple departments from PLCs and from the plant's central SCADA systems. The data existed in a number of different formats, including handwritten forms, Excel files, proprietary databases and CSV files. DataProphet then digitally transformed this process history into a single view.
The unified view spanned:
- 15 months of historical production data
- 173,000 records
- 400 unique process variables.
To optimize cycle times and identify the root cause of defects, DataProphet established product traceability through the mold line; furnaces; raw metal process; and sand processes.
AI-Driven Optimization Via an Intelligent Web Interface
Once the plant data was digitized, DataProphet fed the process and quality data into the DataProphet PRESCRIBE system. Next, optimal prescriptions were generated for the controllable process parameters and delivered to operators. The prescriptions were updated every five minutes based on data that is continuously ingested from the actual process.
PRESCRIBE provided each operator, engineer and plant manager with a customized view of the relevant control parameters through its interactive web interface.
DataProphet issued weekly reports that intelligently prioritized prescriptions for parameters that were most important to improving productivity-taking into account both upstream and downstream changes.
The company reported the following results after PRESCRIBE was implemented:
- Reduced scrap, fewer defects and less rework
- The plant halved its scrap rate in the first month of deployment; within the first three months it achieved an external scrap rate (i.e., shipped defect rate) of less than 0.1% on an ongoing basis.
- DataProphet's AI-driven prescriptions reduced engine block defects to 0.5% for periods of up to three months and achieved an average defect reduction of 40% over the long term-unprecedented in the company's history.
- Increased yield: This foundry achieved record production outputs.
- Lighter carbon footprint.
Sustainability benefits of DataProphet PRESCRIBE for this foundry included:
- Reduced waste
- Lower production energy usage
- Prevention of the unnecessary transportation of defective engine blocks (resulting in an estimated savings of 135 kg of carbon dioxide emissions for each defective block not shipped).
- Since deploying DataProphet PRESCRIBE, the plant saves around $100K per month.
- Enhanced reputation on the digital value chain.
Specific areas impacted by DataProphet PRESCRIBE: sand plant (core shop machine, core packet assembly, painting and baking), melting, and mold press (core loading and casting).
For more information contact:
DataProphet
313-880-3980
info@dataprophet.com
www.dataprophet.com