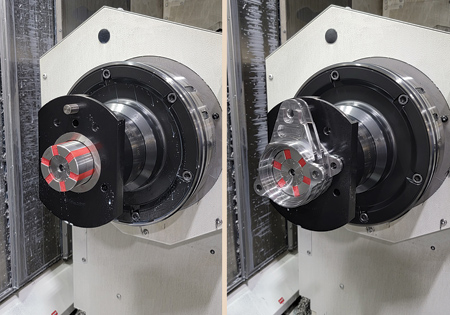
(left) HAINBUCH centroteX system with Mando T212 size 4 with end stop. (right) HAINBUCH centroteX system with Mando T212 size 4 with end stop, shown after part transfer. Part locates on ID, stop face and diamond pin.
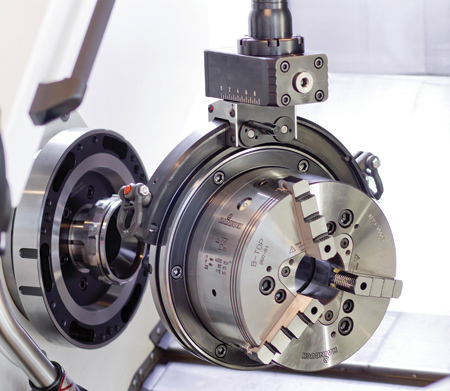
The HAINBUCH centroteX system allows changeover of virtually any clamping device in five minutes or less. It is indicated at the time of installation and never requires indication again, thereby allowing the flexibility to share workholding devices between different machines quickly and accurately.
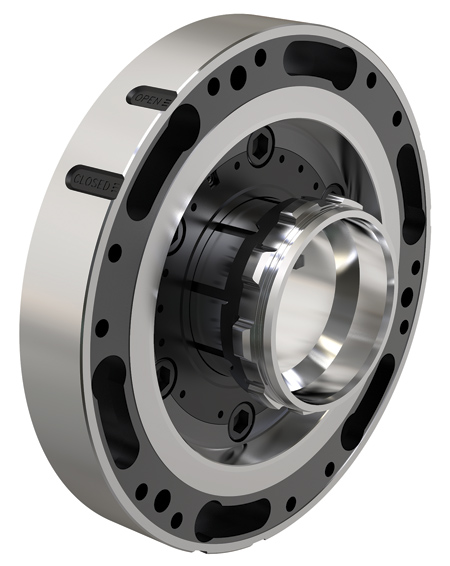
The heart of the centroteX system is an adapter plate (receiver) that is permanently secured to the machine spindle. Because of the bayonet coupling and CENTREX centering ring, repeatability between machine adapter and clamping device adapter is ≤ 0.002 mm without any alignment.
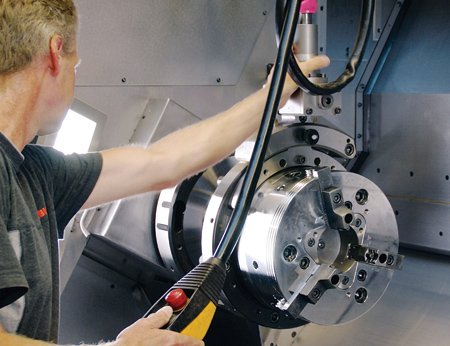
The HAINBUCH centroteX workholding system is designed to provide a highly precise, ergonomically-friendly means of quickly changing large and heavy workholding devices. The Monteq mounting allows for fast, safe and easy changeover without lifting.
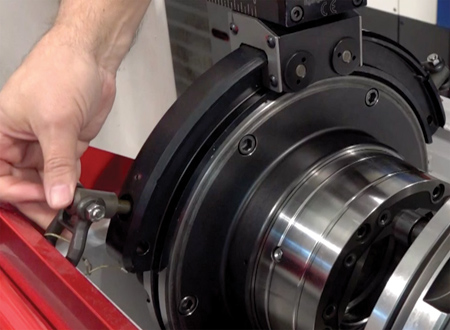
Devices are quickly and easily changed using the Monteq loading device through the use of pins that engage into holes in the adapter plate.
The Actuation Division of Curtiss-Wright in Shelby, NC, produces a variety of components for customers involved in commercial and military aviation markets. Founded in 1929 through a merger of Curtiss Aeroplane and Motor Corporation and Wright Aeronautical Corporation, the company traces its heritage to the earliest days of aviation.
Known for advanced engineering and innovation, today's Curtiss-Wright serves a diversified customer base by providing products and services to the aerospace and defense markets, and to the commercial markets including power, process and general industrial. At a time when supply chain problems have hampered deliveries in many industry segments, Curtiss-Wright is employing advanced production techniques to ensure timely delivery of high-quality precision components.
This approach is evident in the production of ring gears for rotary actuators. Manufactured from 4340M steel, parts require a .001" tolerance overall and a .002" positioning tolerance. Run-out has to be carefully controlled to ensure consistent accuracy.
According to Bert Crawford, Curtiss-Wright Manufacturing Engineering Manager, "In order to achieve the production goals we were seeking while maintaining the highest level of quality, our strategy involved developing systems that optimize the combined features of select manufacturing equipment. For instance, our present line includes six DMG MORI NT 4250 turn-mill centers. To provide quick changeout as well as high precision, we equipped the machines with HAINBUCH centroteX workholding systems featuring the ability to utilize the mando system or the flexibility to mount 3-jaw chucks. Because our operations include lower turret turning and B-axis high-speed milling, turning, boring, slotting, finish milling and gear skiving, as well as A-axis part transfer to the 2nd spindle, we wanted a system that offered maximum versatility in both machining operations and changeover."
Edward Reames, Southeast Regional Sales Manager for HAINBUCH America Corp., explained, "The centroteX system is designed for the fast and efficient changeover of larger workholding devices. This is accomplished through the installation of a machine mount and clamping device adapter capable of handling collet chucks designed for multiple-size parts, as well as standard 3-jaw OD chucking operations. Repeatability between the machine mount and the clamping device adapter is better than .002 mm without alignment. Maximum clamping device diameter is 260 mm and the change time can be as little as 5 minutes."
To facilitate the easy and safe handling of heavy chucks and clamping devices, the HAINBUCH Monteq mounting aid offers an efficient, safe and ergonomically-friendly assist. Suspended above the chuck, the Monteq uses quick-acting screws to secure the clamping device as it is being loaded or unloaded.
A further accessory is the compatible storage container designed to keep all clamping devices at hand and prevent contamination.
Curtiss-Wright also opted for HAINBUCH's Mando T212 adapter for ID operations incorporating quick-change capability. Without detachment of the basic clamping device, the Mando secures the workpiece, since it provides vibration dampening and protection from disfigurement due to vulcanized clamping elements.
Crawford commented, "Because all grip lengths on the part ID are of different lengths, HAINBUCH worked with us to develop an end stop with a diamond locating pin that guarantees accuracy in the machining process. A hole in the part is located on the diamond pin during A-axis transfer from first spindle to the second spindle. The pin is located in the ring gear during part transfer to provide positional accuracy and act as a part driver for heavy machining operations for secondary operations."
Crawford added, "Our part order quantities are typically from 25 to 100. Because of the limited order size, quick changeover time is essential to reduce costs."
Al Dopf, HAINBUCH America National Sales Manager, stated, "For low to mid quantity part runs, changeover time can be the critical determinant when it comes to production and profit. The right workholding system combines speed, precision and versatility to allow fast set-up, maximum repeatability and the ability to handle multiple part sizes and configurations. Sometimes, as with Curtiss-Wright, the customer's needs require specialized engineering solutions. For instance, our HAINBUCH team analyzed customer requirements for fast and efficient part location, and developed the diamond locator pin to provide a solution that is fast and accurate."
"The HAINBUCH team worked with us all the way in designing and implementing the system that we needed," said Crawford. "We have been able to initially improve production through set-up reduction, and have also set the standard to include HAINBUCH workholding systems on all DMG MORI NT 4250 turn-mills. By combining technologies such as multi-purpose machining and precision workholding, as well as working with DMG MORI and HAINBUCH to develop specific advances in technology, we are able to improve productivity and maintain our rigid product quality goals. The founders of our companies were among the earliest pioneers in aviation, and it is our continued goal to remain in the forefront of innovation."
For more information contact:
Curtiss-Wright Actuation Division
201 Old Boiling Springs Road
Shelby, NC 28152
704-481-1150
www.curtisswright.com
HAINBUCH America
W129 N10980 Washington Dr.
Germantown, WI 53022
800-281-5734 / 414-358-9550
sales@hainbuchamerica.com
www.hainbuchamerica.com