
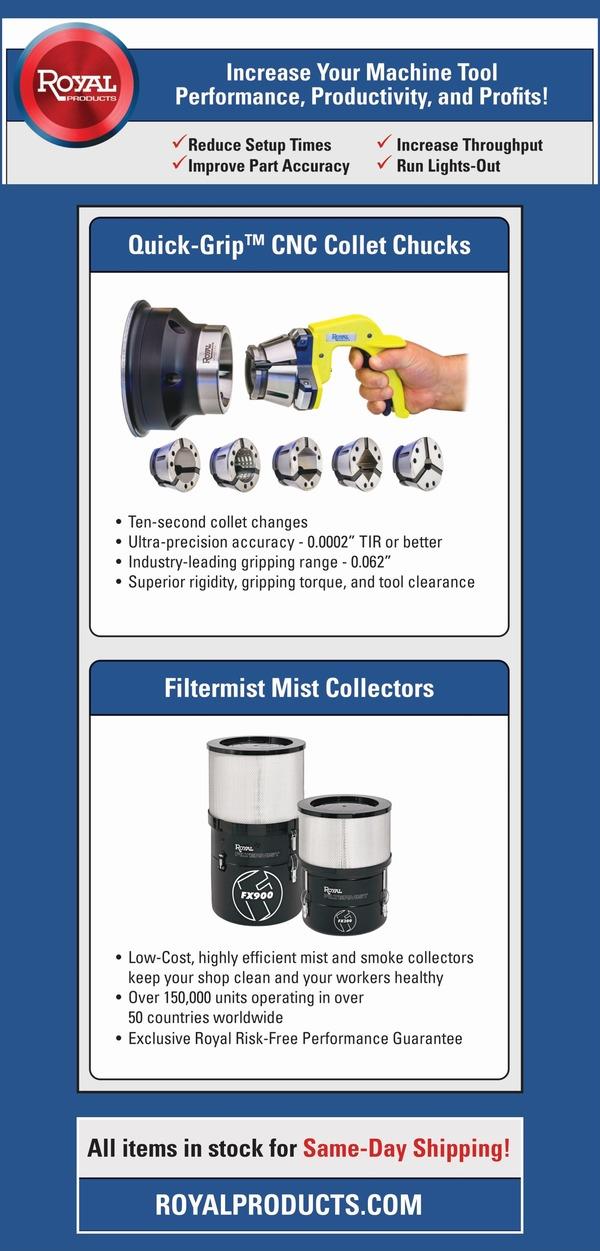
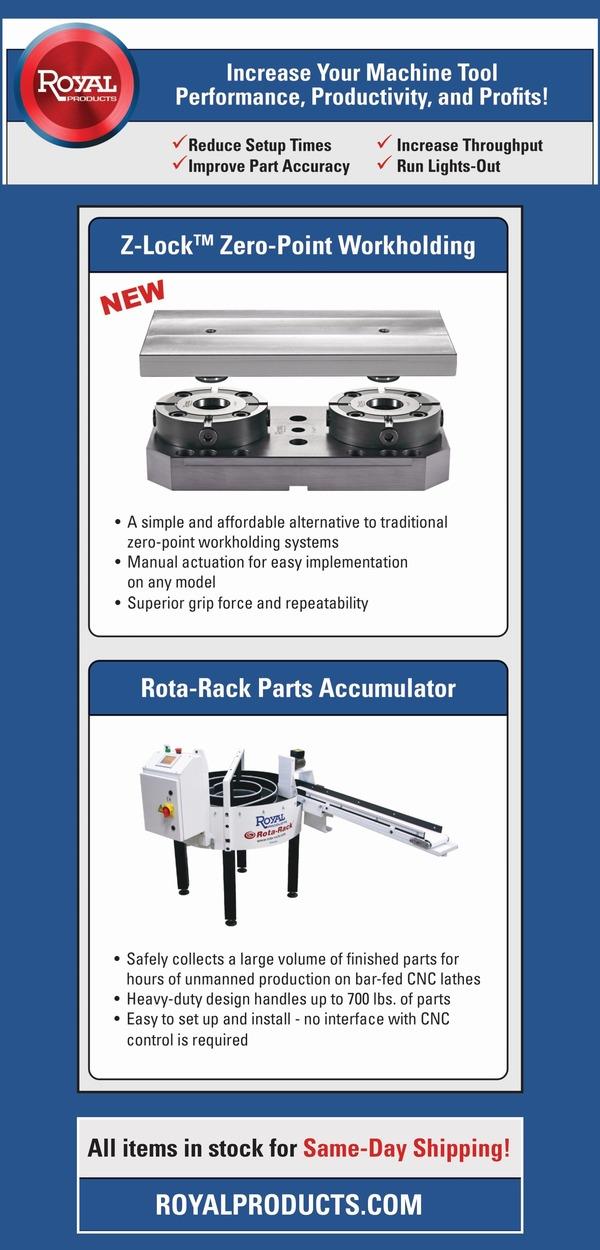

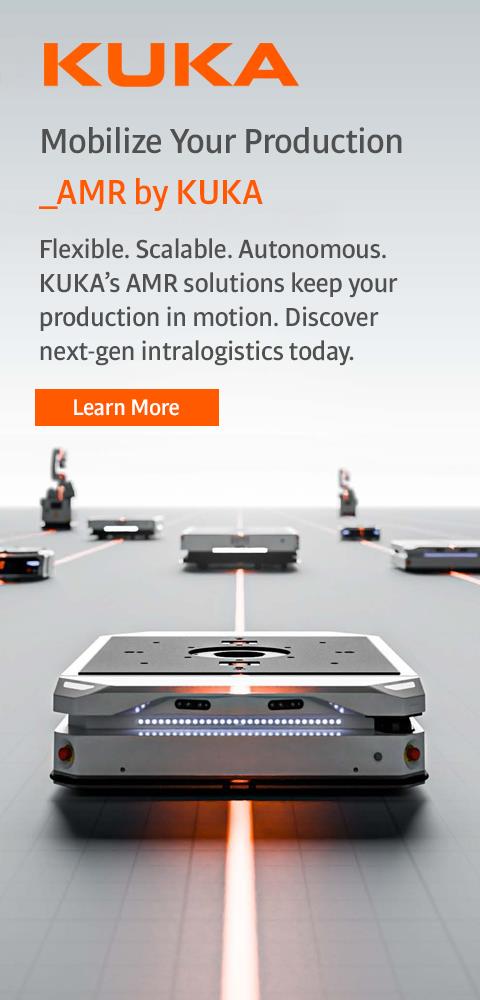
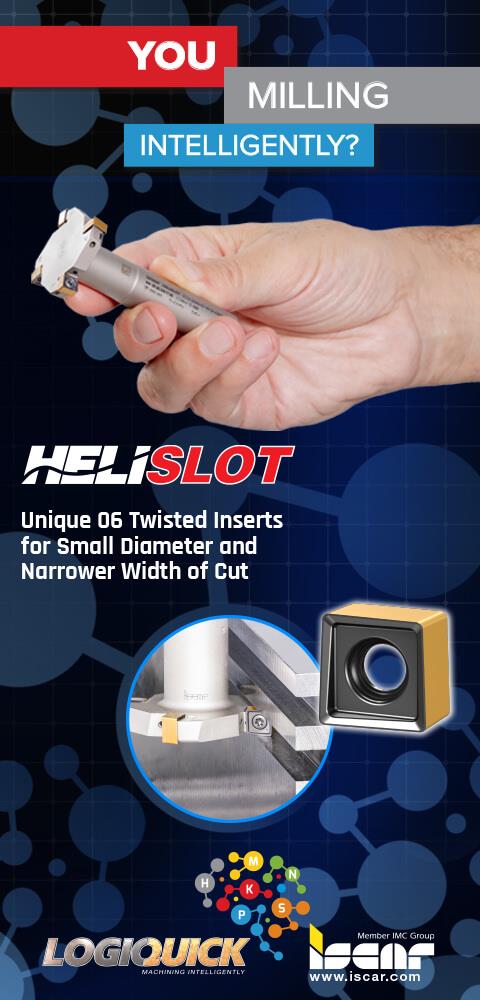
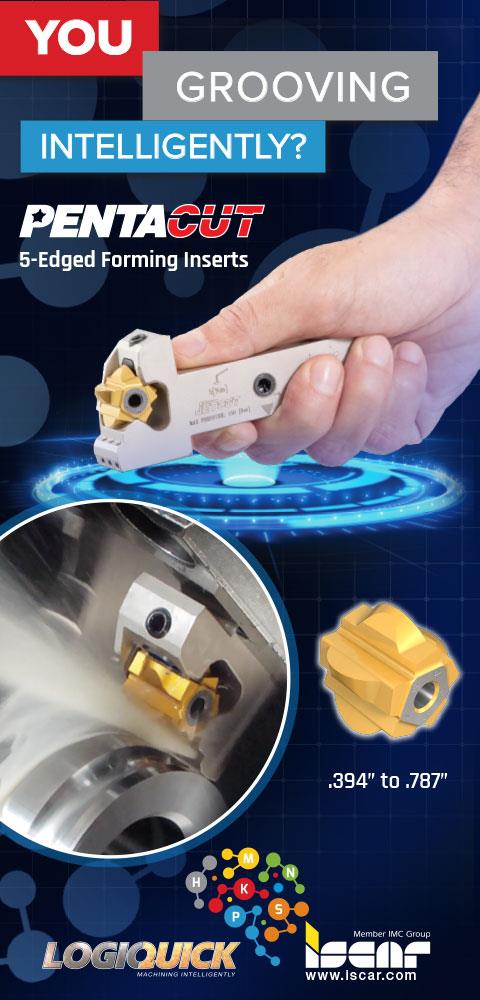
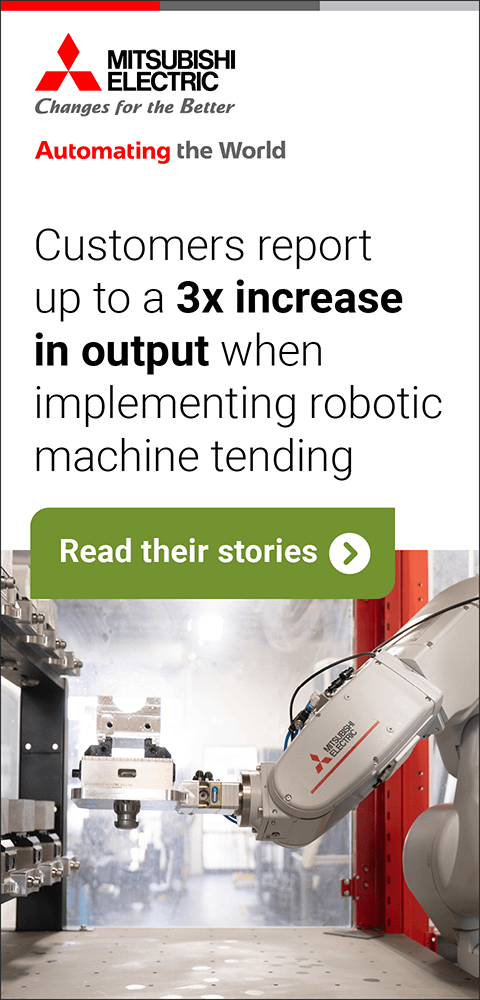
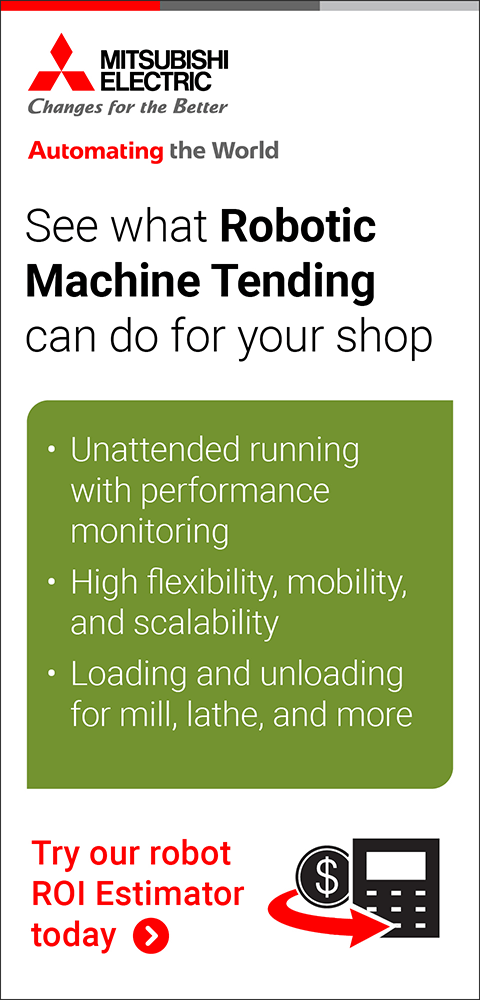
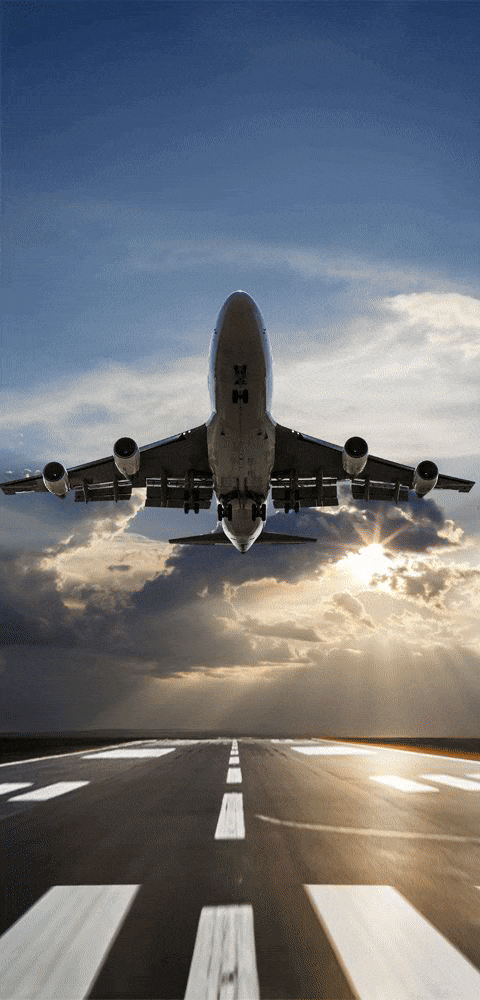
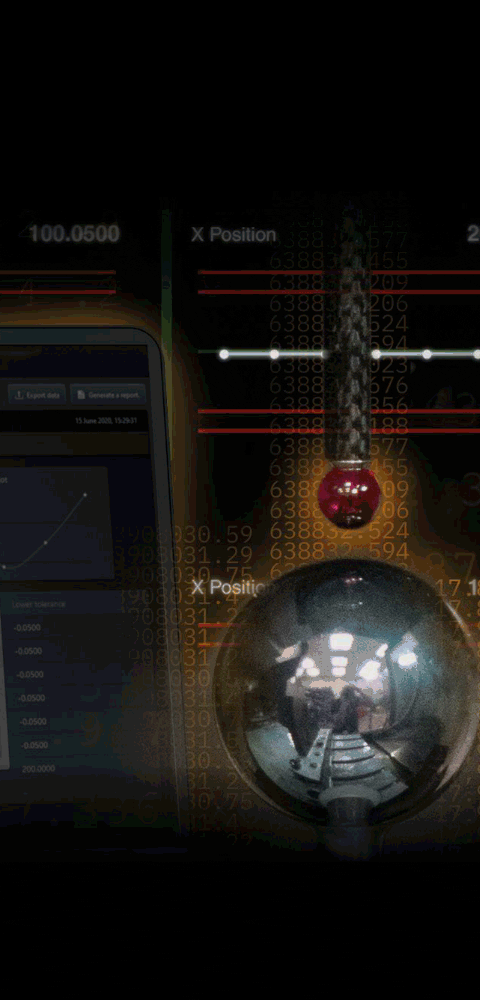
Optimizing Engine Design with Metal Additive Manufacturing
November 1, 2019
Renishaw has worked with Michigan-based Cobra Aero to improve the engine manufacturer's design processes for aircraft and motorcycle engines. After completing the project with Renishaw, Cobra Aero invested in an AM 400 system to increase its in-house additive manufacturing (AM) capabilities.
To optimize the design of its engine cylinders and to gain expertise in AM, Cobra Aero visited a Renishaw AM Solutions Center. There they collaborated with Renishaw engineers to discover how AM could improve the design of a cylinder for an unmanned aerial vehicle (UAV).
"Staying at the cutting edge of manufacturing is important to us," explained Sean Hilbert, President of Cobra Aero. "Investing in AM allows us to develop tools and new products for high value, small volume applications, speed up the manufacturing process and produce designs that would not be possible using conventional subtractive machining.
"We decided to redesign the cylinder because it would improve the overall performance of the engine," continued Hilbert. "Modifications to this high-value part were evolving rapidly, which is why we chose AM to manufacture this component."
"By using metal AM, Cobra Aero was able to design a part that was unique to the application," explained Stephen Anderson, AM Business Development Manager at Renishaw Inc. "Thanks to our laser powder bed fusion technology, they were able to produce a single part with complex lattice structures that performs better than one produced with conventional manufacturing techniques."
For more information contact:
Renishaw, Inc.
1001 Wesemann Dr.
West Dundee, IL 60118
847-286-9953
usa@renishaw.com
www.renishaw.com/additive
< back