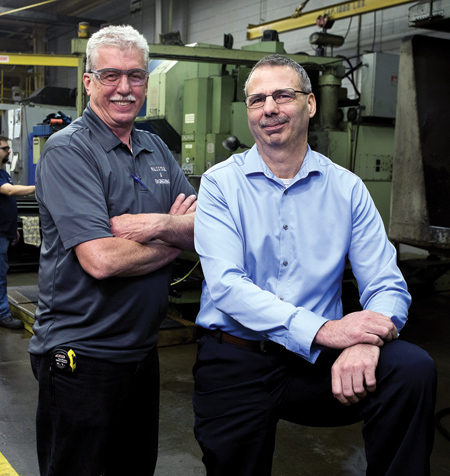
(l-r) Ed Biniak, Continuous Improvement Manager, and Bill Bucciarelli, President, Walco Tool & Engineering
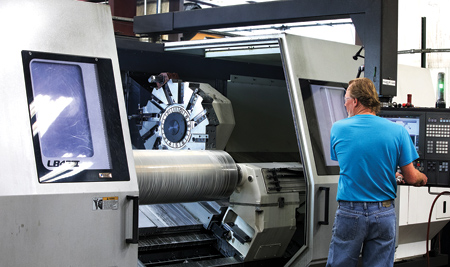
Because of its mixed batch of exotic part materials, Walco frequently acts as a test site for Seco products that are new or under development.
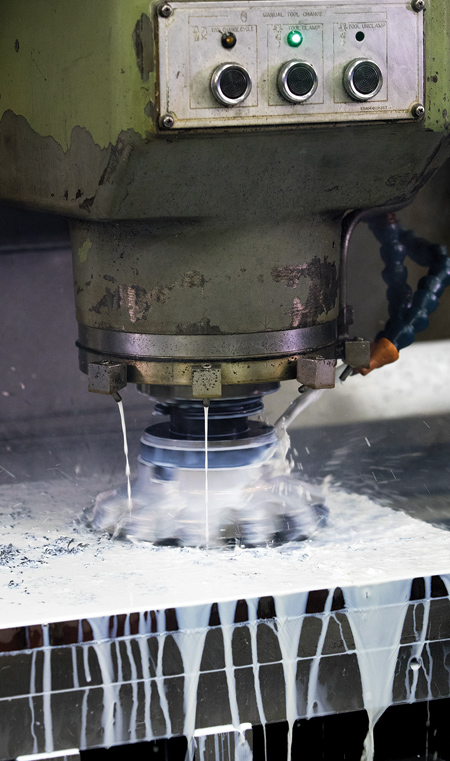
Walco Tool & Engineering machines cast iron and low-carbon steels as well as some aluminums and exotic alloys with cutters and inserts from Seco Tools.
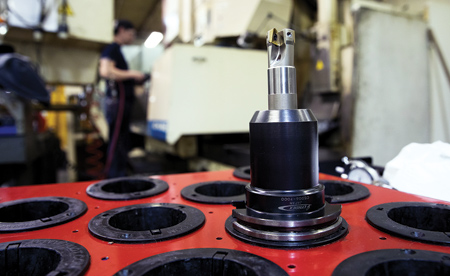
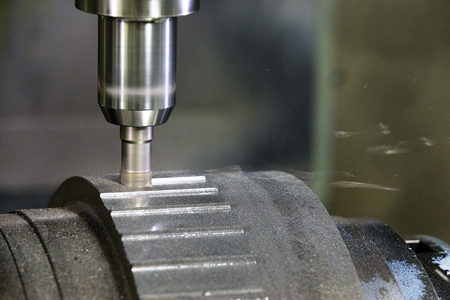
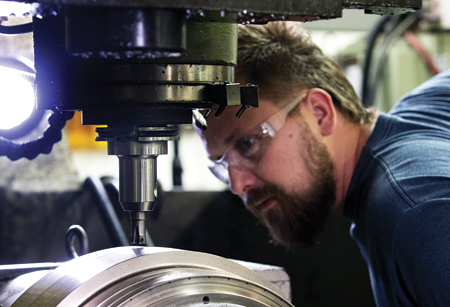
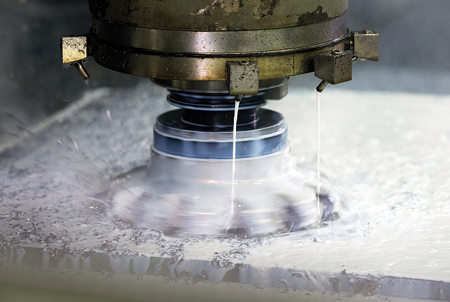
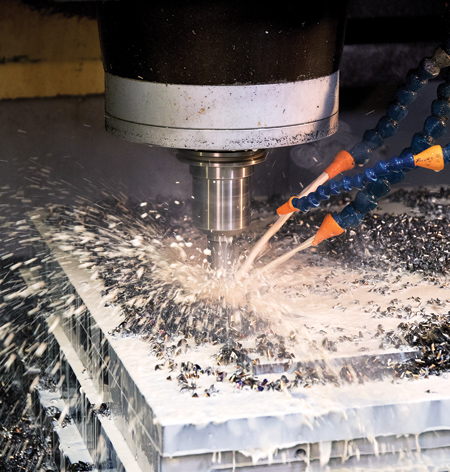
Machine shops today are compelled to produce increasingly complex and precise parts on tight schedules. At the same time, they must work to overcome the challenges created by the skills gap. To accomplish this, manufacturers have tried a wide range of solutions-some more effective than others. But a fifty-year-old Chicago-area shop has found the surprisingly simple answer: growing and sustaining its own team of skilled and dedicated machinists by partnering with local community colleges-and its tooling supplier.
Established in 1968 by machinists Dave Walsh and Fred Cook, Walco Tool & Engineering Corporation began with two men, a conventional lathe and a garage with a dirt floor. Today, Walco is a 63,000-sq. ft. operation that employs 95 people in Romeoville, IL. And to Bill Bucciarelli, Walco's current President, that is a very nice size: "It is big enough that we have capital, we can reinvest both in training and equipment, but it is small enough that it is still a shop environment. Everybody knows each other and we work as a team."
Walco serves a wide variety of customers, including food processing, energy and transportation equipment makers as well as telecommunications and high-tech companies. As a result, the nature of Walco's work demands much from the shop's machinists. "Our machinists carry a lot of responsibility," Bucciarelli said, "They set up and check all their own work and make their own improvements, and that requires high-level skills, especially for parts as difficult as we tackle. Besides the part print tolerances, the challenge is maintaining continuous training and constantly improving and building upon the skill levels of our machinists to keep producing for our customers."
However, maintaining this level of institutional knowledge in the face of the growing skills gap in manufacturing presented a serious challenge that led Walco to develop a comprehensive, multifaceted training program. Since the late `90s, when the shop began struggling to find good machinists, the shop worked toward the creation of a comprehensive training program-a goal it accomplished in 2011.
"We invest in the right equipment; that is the easy part," Bucciarelli said, "The harder part is the machinist training and the sustainability that gives us." When people ask Bucciarelli what happens when Walco invests time and money training employees who later leave, he says, "The thing is they do not leave. We invest in them and they stay."
The Walco training program begins with pre-testing and screening of applicants to determine their mechanical aptitudes and attitudes toward manufacturing careers. After successful applicants are hired, they circulate through every department in Walco. Following pre-testing and post-testing at the department stage, the new employees move to the shop floor, all the while taking required classes at the local community colleges. In total, "With their training on the outside and our training on the inside, it is a good four-plus years to graduate a skilled CNC machinist," Bucciarelli said.
Walco also further improves their new hires' understanding of manufacturing technology with help from their tooling partner, Seco Tools. Once or twice a year, Seco presents training seminars at the shop, essentially a condensed version of the Seco Technical Education Program, better known as STEP. Bucciarelli said the benefits of those seminars are practically immediate: "I heard on the floor a couple of weeks ago that a younger machinist was running a face mill faster because of the chip thinning concepts that he learned at one of the STEP seminars that same month. That is how fast they are applying it on our floor."
Walco's comprehensive training program, and the skilled workforce it produces, represents a competitive advantage. "Over the last couple of years, it has helped differentiate Walco," Bucciarelli said, "I have heard from some of our customers that they receive no quotes from other suppliers due to a lack of skilled labor. I never want that to be the case at Walco. We are manufacturing parts for which many of our customers receive no quotes from others because of their difficulty. Price is always important, but not particularly at the top of their list. Customers come to Walco for the quality and the service we provide them."
The training program goes a long way, but Walco also depends on an array of advanced equipment for both small and large workpieces. On the larger side, machines such as a big 5-axis bridge-type high-speed machining center with a 167" X-axis, 108" Y-axis and 56" Z/W-axis work envelope and a vertical turning center with travels of 90" x 79" x 67" and five-sided machining capability offer unique capabilities to Walco's customers. Three CMMs facilitate quality control and documentation, and the shop also provides large-part surface grinding, polishing, and MIG and TIG welding services.
Despite its diverse collection of manufacturing equipment, the shop has always used tools from Seco Tools to some extent, and that usage has grown over the years. "Seco is very responsive to our needs and their tooling is outstanding," Bucciarelli said. "In this day and age where seconds count on some of these parts, having that optimal grade insert or chip geometry is very impactful on improved part profitability."
Tony Curatolo, Regional Manager for Seco Tools in Illinois and Wisconsin, said that Walco has become more of a partner than a customer, often acting as a test site for Seco products that are new or under development. "With their mixed batch of production and exotic material, Walco is always at the top of the testing list," Curatolo said, including a recent example in which Walco was machining food processing parts and wanted to increase productivity but also limit the dangerous noise generated by the operation.
To accomplish this, Seco partnered with Walco to test the new LP09 milling inserts and High Feed 2 cutter bodies. The inserts, which combine high corner strength with dual cutting edges, were well-matched to the milling cutter bodies, which featured reinforced cores and more teeth per diameter to enable higher feedrates and faster material removal rates. The rectangular shape of the inserts and the close-pitched cutter bodies helped extend tool life beyond that of square inserts. The new cutters were more productive than the original tooling and offered longer tool life-but perhaps most importantly, they performed their task at a far more reasonable and safe level of noise.
Bucciarelli said Seco provides ongoing tool application support, which is important considering the variety of workpiece materials Walco handles. "The food industry has led us into a lot of stainless steel expertise," Bucciarelli said, and added that the shop also machines cast iron and low-carbon steels as well as some aluminums and exotic alloys. "Exotics are a smaller portion of our shop's work, but when we do that kind of work, that is where the Seco tooling and application advice really becomes very important," Bucciarelli said. "We get lots of guidance from Seco on how the tools are to be applied along with optimal speeds and feeds, and what the machining boundaries are."
Walco focuses on low-volume production with the goal of adding significant value through the shop's expertise. Jobs may consist of five or 10 or as many as 50 pieces, but often as few as one or two. Parts range in size from those that can be held in one hand to others that fill the 14' x 9' table of the shop's 5-axis gantry machining center. Tolerances routinely meet or exceed ±0.0002".
Some of Walco's customers build food-processing equipment used to make food items for national and international fast food franchises, among other companies. "Most people do not think of that food group as tight tolerance," Bucciarelli said, "but when you consider the volume that some of these producers handle, millions of units per day, and the equipment being off by even one-hundredth of a gram can add up to tremendous waste."
Walco also uses Seco tooling to produce more obviously tight-tolerance parts, such as the components of a device used to pre-accelerate photons in a linear accelerator at Argonne National Laboratory. The semiconductor industry is also a growing market for Walco, specifically manufacturing parts for the direct-drive motors used to move and polish wafers in computer chip manufacturing.
Customer requests for short lead times on high-quality, low-volume parts have led Walco to run a three-shift, five-day-a-week schedule. Responsiveness is a competitive advantage. "If we get out past three weeks lead time, we start becoming noncompetitive. So typically, we are looking at three weeks all the way down to, with some customers, one and two days," Bucciarelli said.
Engineering services represent a key element of Walco's offering. As Bucciarelli pointed out, "`Engineering' is in our name, so we promote that, both with reverse engineering and value-added engineering." A Walco project engineer is assigned to larger projects and is the focal point for the customer, managing the project from beginning to end. Bucciarelli said the key is to be proactive: "By the time a part or project makes it out to the machine, we need to have all questions answered."
A major responsibility of the project engineering department is seeking out new processes and tooling that fully utilize the shop's equipment. "That can give us an edge that we did not have a year or two ago," Bucciarelli said, "With the help of Seco Tools and other suppliers, our engineers get the tooling solutions squared away."
For more information contact:
Walco Tool & Engineering Corporation
18954 W. Airport Rd.
Romeoville, IL 60446
815-834-0225
engineering@walcotool.com
www.walcotool.com
Seco Tools LLC
2805 Bellingham Drive
Troy, MI 48083
248-528-5200
secotools.us@secotools.com
www.secotools.com/us