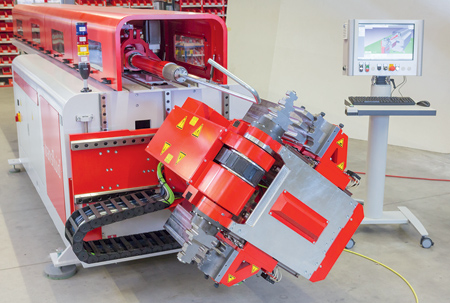
transfluid software offers reliable processes with collision tests before the actual bending process.
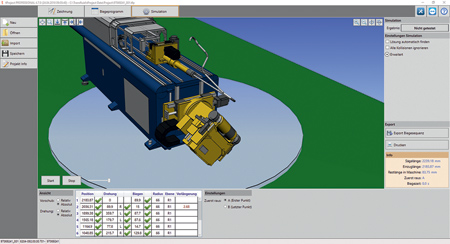
The bending processes are safe when planned with transfluid software.
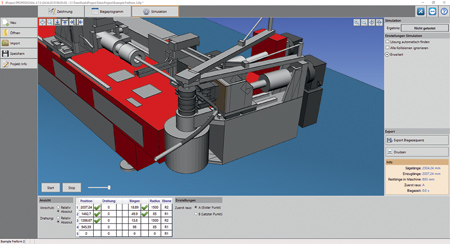
To achieve accurate bending results with safety, the transfluid software takes into account data that is specific to the materials used.
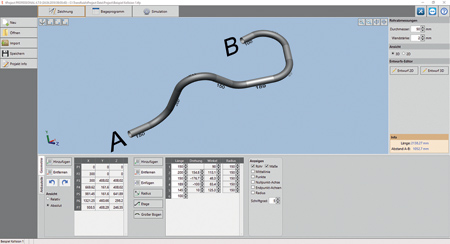
Additional modules contain the whole processes for better control, and manage the data for the forming part of the process.
The two latest versions of the t project software by transfluid are designed to make the tube manufacturing process safer.
The idea behind the t project software is a systematic approach to controlled tube manufacturing. What is complex becomes simple. To do this, it is possible to connect it to CAD, BDE or ERP systems, tube bending machines or bending robots. All of the most common interfaces can be used. The processes can be visualized and validated. Two versions of the software have been developed and play key roles in different areas of tube processing and custom solutions. They can be used depending on specific process requirements.
A main feature of the software is that it reduces the number of steps necessary to manufacture a finished component, making production less exensive. For that reason, it is an effective solution for bending machines and it can be used together with all the usual CAD systems. The software is designed to eliminate any possible collisions with the equipment, tools and environment before the actual bending process starts. It tests the feasibility of the tube geometry. The necessary tool and machine parameters are delivered online through the CAD system. If a robot is used for the bending, the software will process the data, without expensive reprogramming of the robot. To do this, it is possible to load data in the same way as for a standard bending machine. The pre-installed software will calculate all the necessary movements for the robot. The automatic product-specific adjustment of the bending speed for all transfluid machines makes it possible to process long tube safely and without oscillations.
The software solution also helps with the economical cutting of tubes. With integrated cutting systems, the transfluid software will optimize the cutting pattern. The cutting lengths are calculated with precision and fewer raw materials are used. This is particularly effective with transfluid's t cut equipment for orbital chipless cutting. A cutting sequence is prepared at the same time as the manufacturing process. The cutting is automatically improved and the semi-finished tubes can be used with as little waste as possible. With the individual marking, linked to the data for the connections or bending sequences, the component can be tracked at all stages of the process. The data transfer happens via an interface with CAD, ERP and other programs.
t project is based on the Windows operating system and the use is intuitive. To achieve accurate bending results with safety, the transfluid software takes into account data that is specific to the materials used. Various additional modules contain all the details of whole processes in order to have better control over the process and manage the process data of the forming techniques. The t project software can be connected directly to the company's internal network (intranet) to have better data safety. The two versions of the software are available as isolated or networked options. The first option, t project Basic, offers an almost complete digital basic package. This makes it possible to transform isometries into bending data directly and also to calculate the correction and over-bending values automatically. By entering the diagonal data for the space, it is possible for the operator to control the bent component in an easy and manual manner. If the tubes have not been designed in the CAD system, it is also possible to enter the geometry manually.
The t project Professional version has the same functions and some more. Any necessary extensions are calculated automatically. Additional production safety comes from the collision tests mentioned earlier. If a potential collision is found, the software will find an alternative by itself. The Import module has 30 interfaces for many of the most common programs, such as IGES, STEP, JT or PCF, to connect them to CAD, measuring equipment and Office programs. The system has 10 export interfaces to export data, for instance as IGES files.
The option to run simulations on the tubes is helpful for practical applications that include flanges or forming. To calculate a whole package of tube geometries and to test that there are no collisions, the software has a Multitest function. It tests all the geometries by running calculations in the background and filters out the process sequences that are not possible. If necessary, the geometry will be adjusted.
Visit https://www.youtube.com/watch?v=-1HFY3DmCak for a video.
For more information contact:
transfluid Maschinenbau GmbH
sales@transfluid.de
www.transfluid.net