
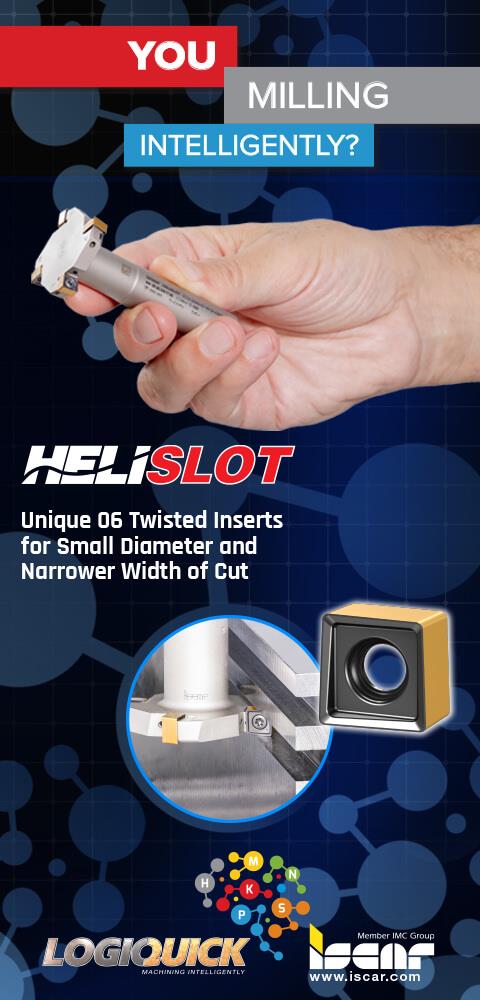
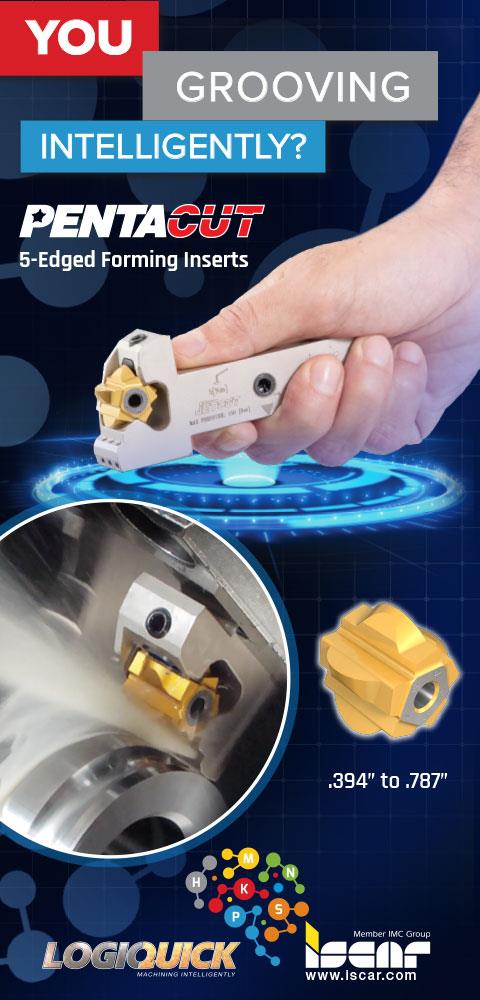
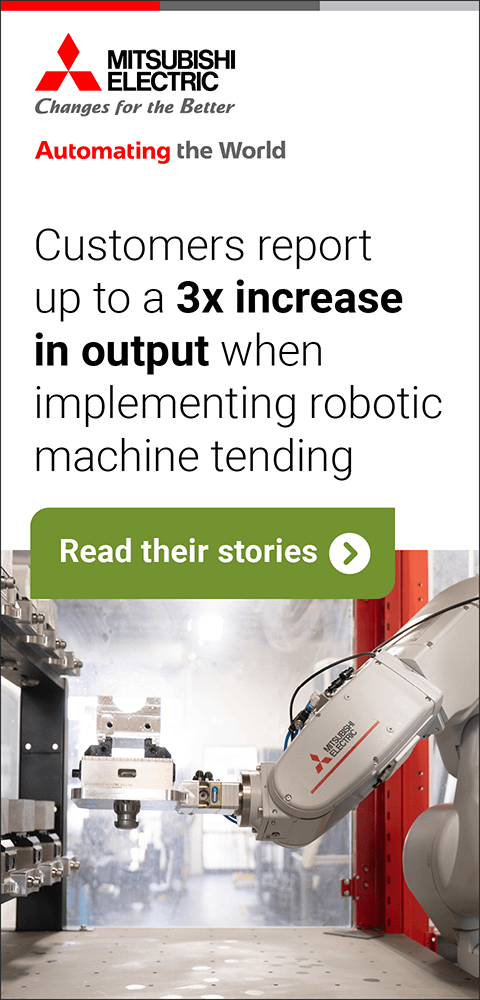
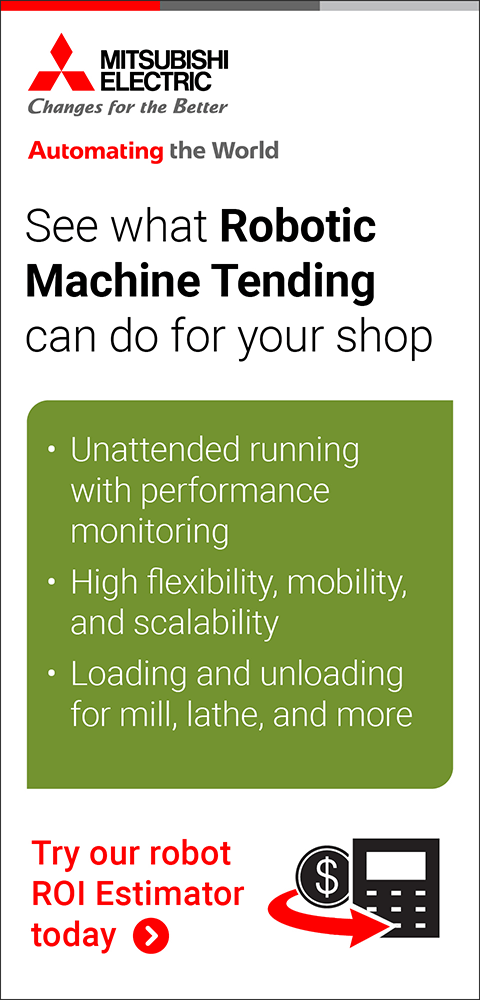
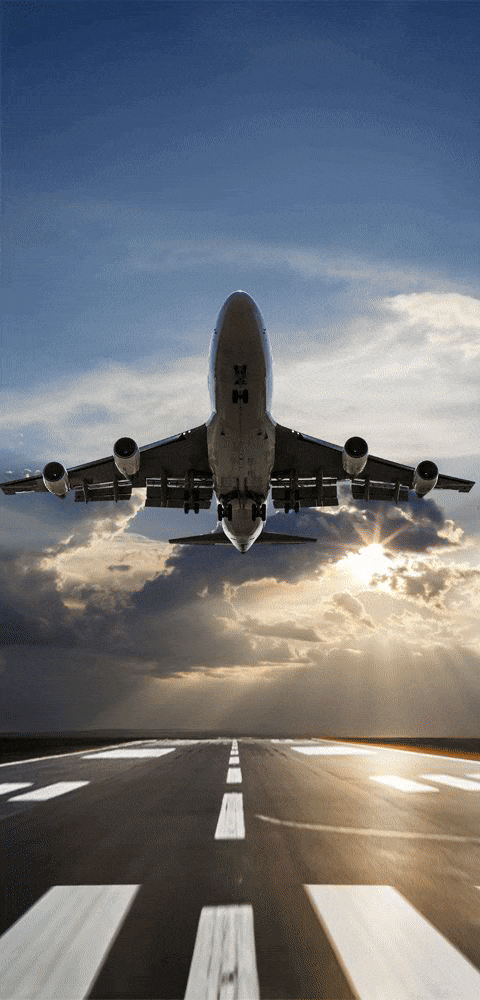
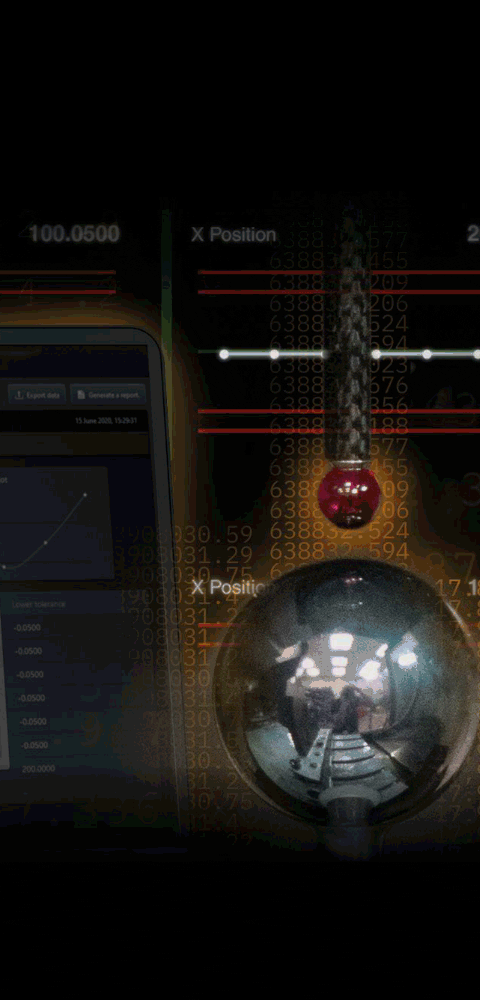
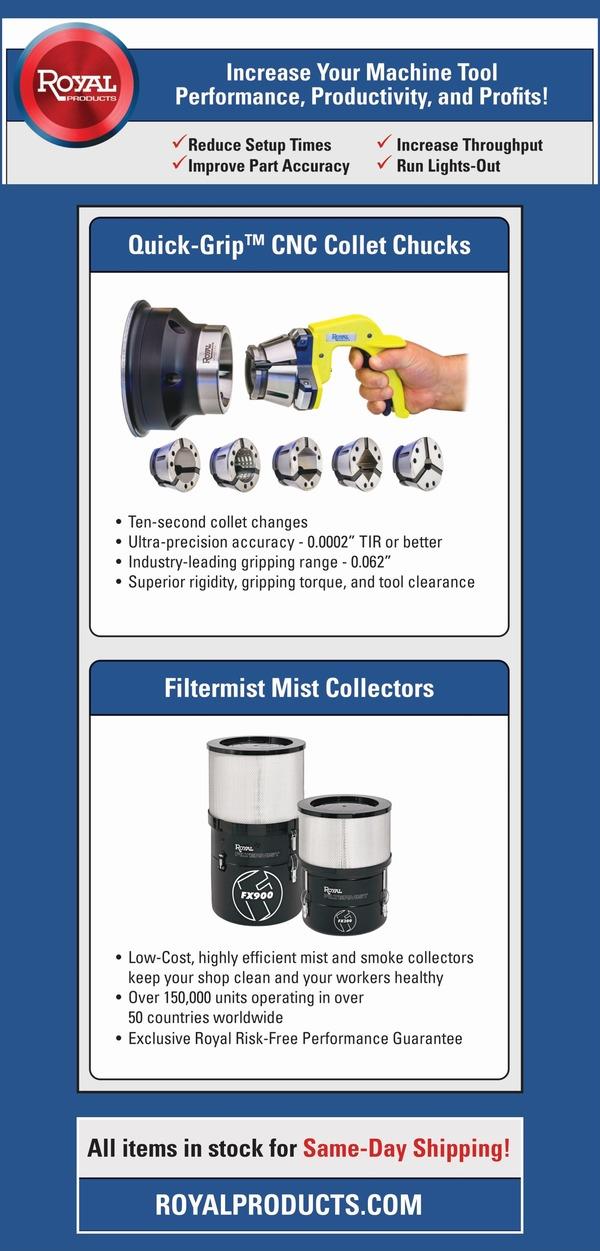
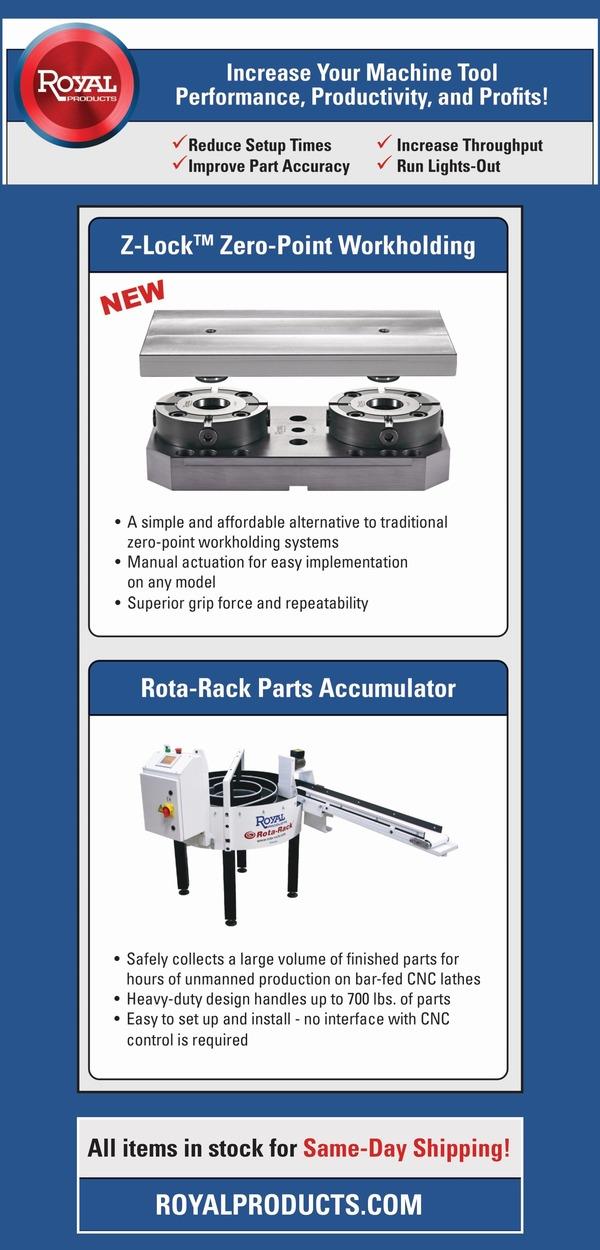

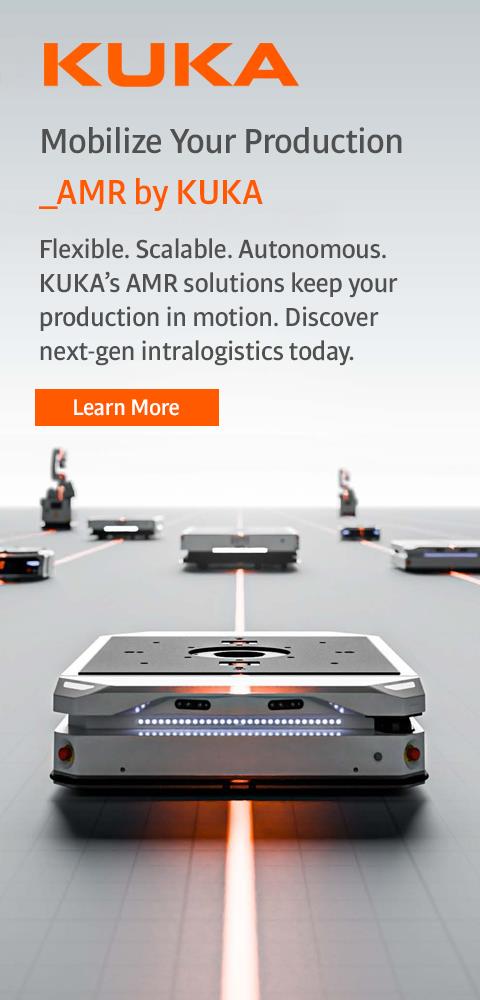
AGV and Flow Rack System
November 1, 2019
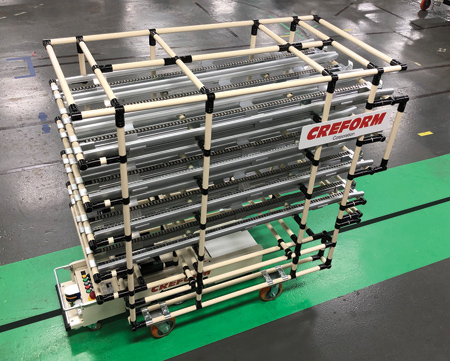
Creform built BST AGV Tugger with kitted flow racks for an automotive parts manufacturer.
Creform Corporation has built an AGV and flow rack system for an automotive parts company. The AGV Tugger (with racks) transports powertrain components as they travel between machining to the clean room area for assembly. Full carts are delivered, and empty carts returned.
The BST AGV, Model CA2-A3800C, with brushless motor, works as an automated tugger and pulls each of the eight flow racks through the system. It can travel up to 50 m/min. and has a load capacity of 1,322 lbs. (600 kg). The BST Tugger moves along a magnetic guide path and travels approximately 600'. It makes a circuit of the route every hour during production over a two-shift operation. The AGV automatically exchanges (drop/pick-up) full carts and empty carts during the run. It is manually started to allow flexibility in the operation: the associate can either press a dispatch button on the AGV or remotely start with an optical transmitter. It comes with a manually operated battery exchange to swap the battery at the end of each shift.
All Creform BST AGV Tuggers come with an optical sensor, bumper, E-Stop, audible warning device and indicator light.
Each of the flow racks is made utilizing the Creform system of 28 mm pipe and joints. They were kitted and assembled onsite by the Creform team. The rack's dimensions are 63" L x 31" W x 65" T. There are four ergonomic levels per cart and each shelf/level is rated for a distributed load of 200 lbs. The parts flow down gravity lanes with no packaging. This helps ensure damage-free parts handling and production efficiency. Integral to the flow racks are wear-resistant, stainless steel covered Creform Placon skatewheel rollers. The carts feature 6" casters to handle the frequent movement of the AGV. The casters also allow an associate to easily move the carts manually for positioning. Each cart also features a special hitch plate to accommodate AGV coupling.
Options with Creform AGVs can include: multi-course control with the addition of "Course-10" module, opportunity charging system to minimize the need for manual battery changes and a Creform Preventive Maintenance program.
The Creform System is used to create an array of material handling and efficiency enhancing devices and is a proven component in continuous improvement and Lean Manufacturing programs. The company partners with customers in developing and implementing these programs.
For more information contact:
Creform Corporation
P.O. Box 830
Greer, SC 29652-0830
800-839-8823
SCsales@creform.com
www.creform.com
< back