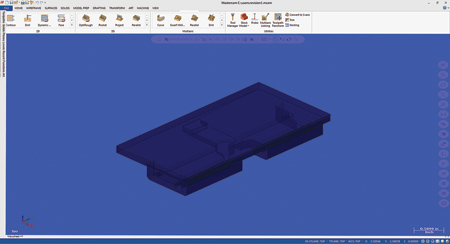
One of Fowler's favorite features is Solids, a CAD solution that allows programmers to draw and manipulate models in an intuitive, streamlined interface.
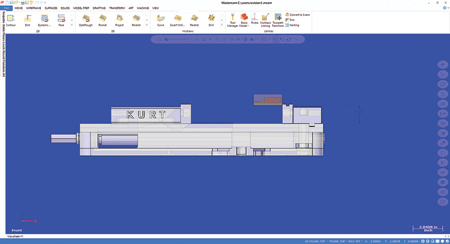
The Backplot and Verify features simulate the machining process and predict any issues that may occur. Knight can see exactly where the stock is sitting in the vise and create a stock model. As long as the tools are in the right place, any mistakes are obvious.
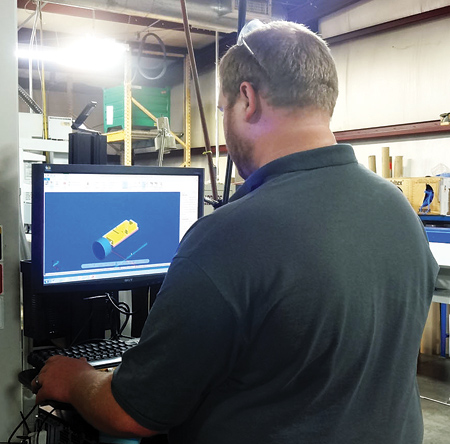
Programmer Caleb Knight uses Dynamic Motion Technology to push the machines as fast as they will go.
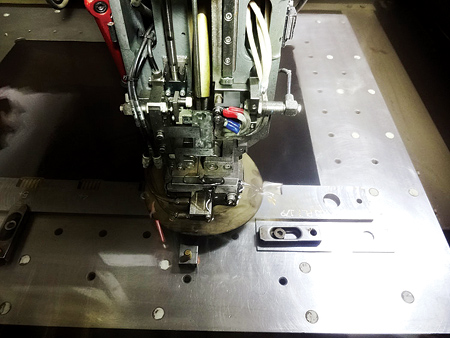
Hi-Tech purchased the wire EDM machine for battery components and mold work. Machinist Mark Freeman is especially excited about the wire EDM, which has just been outfitted with a new spindle driver.
In 1987, Robert Fowler began machining parts in his backyard in Spartanburg, SC. In 2000, he outgrew the space and moved to a shop space just a few short miles from Interstate 85, convenient for shipping out the numerous parts his shop had been manufacturing. Now run by his son, Robbie Fowler, Hi-Tech Machining Company, Inc., has grown immensely. This expanding company serves its clients through the design, machining and repair of custom parts and molds. Most of its work involves repairing highly specialized components. President Robbie Fowler calls Hi-Tech's focus "industrial support."
Hi-Tech is well-suited to repairing and re-machining complex parts, and much of the company's success lies in producing 3D profiles. The shop has a Swiss machine for plumbing fittings, special fasteners and bushings; and a wire EDM machine for battery components and mold work. Machinist Mark Freeman is especially excited about the wire EDM, which has just been outfitted with a new spindle driver. Last year, Fowler thought it would be a good idea to set up a PC on a rolling cart that can be taken from machine to machine for programming on the fly. Almost every single employee on the floor can program; the one person who cannot yet was recently hired and is quickly learning.
Most of the parts are made from plastic, A2, aluminum and steel. Because the majority of the jobs are custom, Hi-Tech rarely repeats the same part. Machining so many unique, complicated parts requires a dedicated team, advanced equipment and powerful software to run the wire EDM, three vertical machining centers and three CNC turning centers. The Swiss machine is programmed manually.
Fowler shared that the only CAD/CAM software that Hi-Tech uses is Mastercam (CNC Software, Inc., Tolland, CT), and it has been that way since 2000. "A friend had introduced me to it and I just stuck with it. Once we got more CNC equipment, we purchased our own version of the software," he said. The company is on a Maintenance plan with Barefoot CNC (Morganton, NC), their local Mastercam Reseller. Fowler calls Jimmy Wakeford, Barefoot President & CEO, whenever his team has a problem. Wakeford is always more than happy to help and even urges him to call more often. The team at Barefoot keeps Hi-Tech's Mastercam Mill, Mill 3D, Lathe and Wire seats up-to-date and helps programmers navigate the complex problems they face every day.
The first step to Hi-Tech's process is creating a program from the models that the customer provides. Often the customer cannot provide a model, though, and the team instead draws a new model within the software. "We rarely ever get repeat jobs, so most of the time it is the first process we do in manufacturing the parts. We hit Mastercam and create a program," Fowler said. "The software is a huge part of our first few steps. With its 3D pictures, we did not realize it was as good as it was or we would have started using it much earlier." When the programmers repair molds, they either re-machine the whole part or just cut sections from it. "Sometimes it was an engineering error where the previous manufacturer left out too much material, so we go back and re-machine," he added. "Sometimes it requires removing a section of it and bolting a new section in or welding a section up. It just depends on how the part has been damaged."
One of Fowler's favorite features is Solids, a CAD solution that allows programmers to draw and manipulate models in an intuitive, streamlined interface. Hi-Tech's employees can control every aspect of wireframe, surface and solid models-something that was not possible before Barefoot Applications Engineer Jason Parks introduced the programmers to Solids. "We would have to import stuff in as a surface," said Fowler. "We had not realized the huge benefit of working with Solids. Now we can push, pull, manipulate-everything." His team has noticed the difference most clearly with their lathe, because it is much easier to get at chamfers now. Fowler also appreciates the freedom Solids provides his programmers, who frequently work with difficult parts. "There are all kinds of geometries we see that people want to get machined these days," he said.
The programmers also incorporate the software's Model Prep features (which are a part of Solids) when making precise adjustments. "We use it several different ways. A lot of times you bring just your blank material in and see how it machines it. And then if you are concerned with over-machining it or removing material that you should not, we will just call the model stock and see what kind of discrepancy we get between the two," said Fowler. Although this is a powerful troubleshooting feature, Hi-Tech also finds the Backplot and Verify features useful. Both simulate the machining process and predict any issues that may occur. "It will show you exactly where the stock is sitting in the vise," said the newest programmer, Caleb Knight. "If you made some kind of a mistake, it tells you exactly what it is."
Once they have modeled and simulated the part, the six machinists rely on Dynamic Motion technology to ensure efficient machining. This feature, also referred to simply as Dynamic, continuously monitors the material as it is being cut. Proprietary algorithms allow the feature to anticipate and avoid air cuts, tool breakage and material damage before it occurs. As a result, programmers can run parts at astonishing rates. "We push them pretty much to the top of the limit with Dynamic. It took a while for us to trust what it was doing, but once we did it was great," said Fowler.
Recently, Hi-Tech was commissioned to machine a fork plate. Knight explained the process: "It is made out of 41/40 steel. The vertical machining center actually drills both ends with a trunnion that rotates up, so it drills one end and then the other. The basic operation on this is 2D High Speed with some pockets." He went on to share that each of the successive angles, ranging between 11° and 90°, requires its own turn and operation. "If it were not for the trunnion, it would take a lot more operations. With the turning, you really get everything in one or two operations. It saves a lot of time. It probably takes about 45 minutes to set up this whole type of part. Before, it took two hours to get different set-ups," Knight said, "It can be kind of tricky sometimes, but the software really helps." The combination of Dynamic toolpaths and the trunnion table adds 4- and 5-axis machining capability to shave considerable time.
"This part is kind of complex," said Knight, "because zeroes are usually on the part or the zero is at the center of the rotary axis. So instead of touching the part off, you have to move the part to zero. That can be kind of tricky, but the software really helps in trying to see your parts." Knight pointed out that he can see exactly where the stock is sitting in the vise. "You can bring the actual curve vise in. Then we get a stock model," he said. As long as the tools are in the right place, any mistakes are obvious. The new programmer marveled at the fact that the whole part could be made with the same 3/8" end mill. The radius is later built out with 1/8" and 1/16" end mills. The ability to create stock models and modify them as needed saves significant time when machining new parts for new customers. Common parts such as special nuts, bolts, washers, bushings, etc., can be machined quickly and easily.
With operations running so smoothly, Fowler is looking to the future. The first step of his plan is to add new machines. "Our largest machines are 40 inches in X and 20 in Y and Z. We are looking at getting bigger equipment to see if we can get our shop rate up a little more," he said. "It seems like there is a lot of competition in the size that we have now. We are trying to separate ourselves from mom-and-pop shops." To match these increased capabilities, Fowler also plans to invest more resources to marketing. He explained, "At least 99% of the work we get just comes to us. We are ready to take on more."
Once Hi-Tech's machining capabilities and customer base have evolved, Fowler hopes that the company will start manufacturing larger quantities of parts. Currently, a 1,000-part lot is considered big because Hi-Tech does not stock pre-engineered material due to space constraints. That should change soon with the acquisition of more shop space. With a solid plan and reputation for excellence, though, Hi-Tech will be achieving its newest goals soon.
For more information contact:
Hi-Tech Machining Company, Inc.
360 Mt. Pleasant Rd.
Spartanburg, SC 29307
864-582-6937
www.htmcinc.com
CNC Software, Inc.
671 Old Post Road
Tolland, CT 06084
800-228-2877
info@mastercam.com
www.mastercam.com