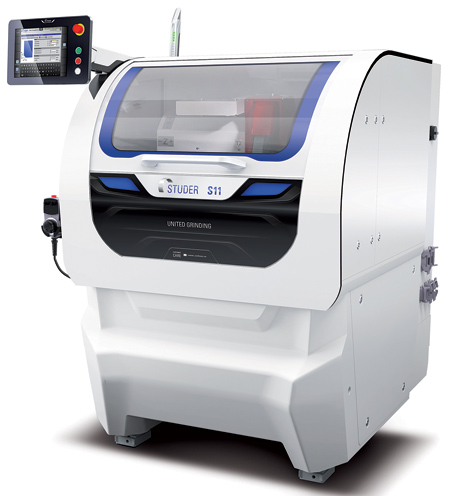
The STUDER S11 offers enhanced performance in a small footprint.
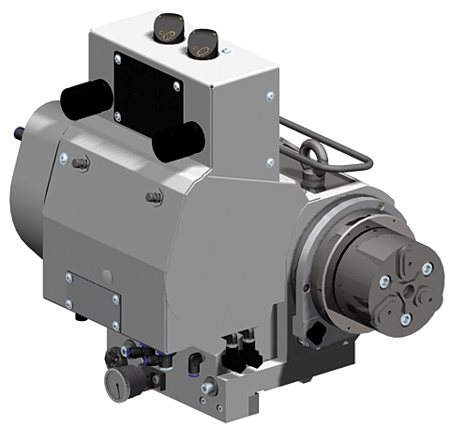
With the external tools from StuderGRIND and the new chuck workhead, threads and polygons can be ground with the S11.
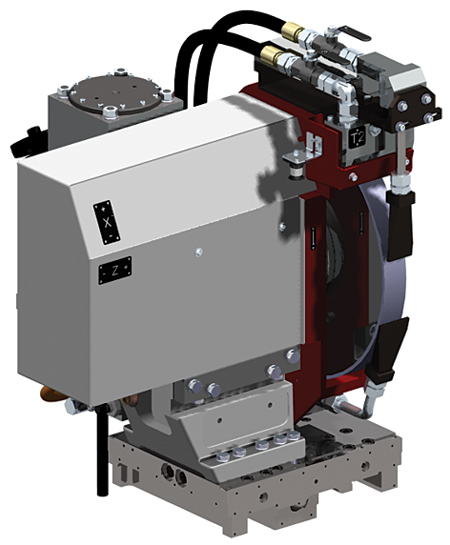
The new HSG spindle enables cutting speeds up to 140 m/s.
United Grinding has announced expanded functionality for its redesigned S11, the smallest production cylindrical grinding machine in the STUDER portfolio. This was showcased at the company's recently held Motion Meeting 2017 at its headquarters in Thun, Switzerland. This annual meeting offers the company's global distributors hands-on experience in the latest technology offerings from United Grinding as well as an introduction of the newest products and developments.
"Now S11 users can profit from the diverse advantages of the STUDER standard grinding cycles and StuderGRIND grinding software for offline programming. Using StuderWINfocus software together with the FANUC control enhances its capabilities," said a company spokesperson.
StuderWINfocus programming software includes optimized input masks in which the user simply enters the application specific grinding parameters. StuderGRIND offline programming software is made up of a variety of modules. The following modules are available on request for the S11:
- StuderDress for optimized clearing strategy, for profiling grinding wheels
- StuderThread for thread grinding
- StuderForm for form grinding
- StuderContour for grinding longitudinal contours
- StuderGeoImport for convenient use of workpiece geometry straight from a DXF file.
"The customer still has the opportunity to design programs using micro functions," said Christian Josi, Project Manager at STUDER. "With the STUDER standard grinding cycles, however, more convenience and support is available with the S11. The uniform control platform provides program consistency on all machines running Windows operating systems. This is regardless of whether the program is programmed directly on the control or is generated externally with StuderGRIND."
The conversion to the new control in the S11 provides further advantages. Up to now, operators were only able to work at grinding wheel speeds of 50 m/s (in exceptional cases max. 80 m/s). Now, with the combination of a FANUC control and StuderGRIND, high-speed grinding is possible with CBN grinding wheels and grinding speeds of up to 140 m/s. A new high-speed spindle has been designed especially for the S11. "The S11 achieves high abrasion performance in a minimum amount of space," said the spokesperson.
The S11 now enables typical C-axis applications such as thread and form grinding. This is made possible by a new version of the workhead with C-axis function in combination with StuderThread or StuderForm software modules. The new and re-profiling of grinding wheels, due to an optimized clearing strategy with StuderDress and machining of longitudinal contours with StuderContour, extends the scope of application of the S11.
The new S11 also features the SBS Dynamic Balance System. This combined system for contact detection by means of vibration measuring for semi and fully automatic balancing of the grinding wheels reduces downtime because of less air grinding. It also enables the process to be monitored, for example observation of grinding level noise.
STUDER offers the S11 in two different machine housing designs. The existing version is specially designed for manual loading or can be combined with small handling systems. The new machine housing is optimized for vertical loading with a top hatch. It is suitable for interlinked production in which the machines are loaded and unloaded via portal cranes. Both designs offer enhanced accessibility and ergonomic features.
For more information contact:
UNITED GRINDING North America, Inc.
510 Earl Blvd.
Miamisburg, OH 45342
937-859-1975
info@grinding.com
www.grinding.com