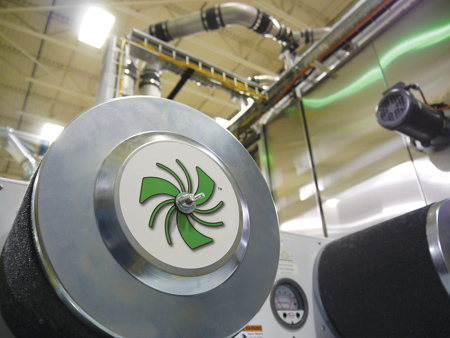
Maxum LLC, a new company with an innovative science-based approach to parts drying.
Maxum LLC part drying technology is built on science, plus decades of application expertise. Its full line of industrial-duty air blow-off systems, including energy saving blow-off devices like the patented Nozzle Bar and its full line of Maxumizer blowers, nozzles and air knives, is able to embody the design motto: use less energy, blow stronger and last longer.
A prime example of Maxum's science-based approach is its new converging and laminar flow technology. With traditional blow-off devices, the focused air starts to expand as soon as it leaves the nozzle. With Maxum's converging and laminar flow technology, the air reaches the part in a stronger, faster, more concentrated form, improving efficiency while saving energy. All Maxum air blow-off devices employ this technology.
"Additionally, the internal air flow design of all Maxumizer Air Blower systems is specifically optimized to provide higher output with less energy in the best performance range for surface blow-off and drying applications," said the company spokesperson. "In most cases this design will use 30-50% less horsepower while running at much slower speeds."
Maxum's unique approach is also illustrated in its innovative drive system. Maxum developed its Bearing Bridge drive system to replace the typical belt-driven approach. The Bearing Bridge uses separate bearing cases located on either side of the drive pulley. "This design provides properly positioned bearing load to reduce heat and dramatically extend service life," said Jim Freers, President and CEO. "In fact, this design provides 10 to 15 times the 'L10' bearing life of older cantilever drives that rapidly fail from the uneven overhung belt load."
Maxum has also engineered blower enclosures that reduce the operating sound level below 75dB at a three-foot distance. These corrosion resistant polymer enclosures have a small footprint, standard gauges to monitor performance, oversize filters with pre-filters and an integrated skid mount.
The company's newly designed web site, www.maxumair.com, provides information about the company and its products, including videos on key aspects of Maxum parts drying technology.
"Maxum's innovative air blow-off and drying equipment remove water, liquids and debris successfully," said the spokesperson. "The equipment is ideal for preparing products for assembly, packaging, labeling, inkjet printing, inspection, powder coating and more. Whether it is bottles, cans, metal parts, circuit boards, extrusions or any other air blow-off application, the Maxum mix of creativity and science ensures the success of your application."
For more information contact:
Maxum LLC
P.O. Box 70025
Rochester Hills, MI 48307
248-726-7110
www.maxumair.com