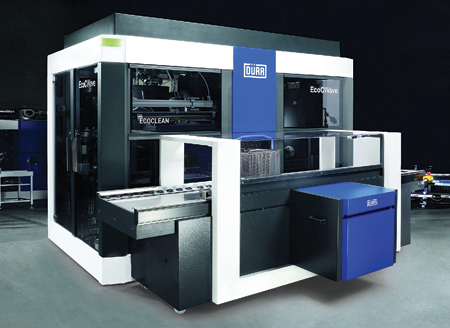
The new EcoCWave is engineered to provide optimized quality and efficiency in cleaning processes.

Round tanks prevent the formation of chip and dirt traps.
With its EcoCWave, Dürr Ecoclean has developed an equipment system for aqueous cleaning processes that is designed to handle a wide range of tasks - from rough to fine cleaning - in an efficient manner.
"Aqueous part cleaning, with alkaline, neutral or acidic media, ranks among the most widely employed technologies in many industries, with application levels ranging from rough to intermediate to fine cleaning," said a company spokesperson. "Dürr Ecoclean's new EcoCWave system covers this entire application spectrum due to its modular technology. With its small footprint, the system can easily be integrated into any production process. It also provides versatility by being easily adaptable to changing cleanliness and throughput specifications." The new cleaning machine rounds off Dürr Ecoclean's product range for aqueous cleaning with the Universal 81W, Mega 86W and EcoCMax.
The EcoCWave is equipped with two or three flooding tanks, depending on customer requirements. The tanks are upright and their rounded geometry allows for optimized flow, which prevents the formation of chip and dirt traps. This results in improved cleaning quality and longer cleaning fluid service life. Moreover, each tank has its own separate fluid circuit with full-flow filtration. The cleaning and rinsing fluid is filtered while filling and draining as well as in the bypass. Bag or cartridge filters can be fitted in combination-type filter housing. The system's filtration characteristics can be adapted to changing cleanliness requirements quickly and without any hardware modifications.
It is designed to ensure that the fluid and mechanical cleaning devices - e.g., ultrasonic units and spraying nozzles - can reach the product effectively from all sides. In addition, the design of the rollover unit minimizes fluid drag-out.
"Powerful pumps and large-diameter piping used throughout the EcoCWave accelerate the operations of filling and draining the work chamber and tanks," said the spokesperson. "As a result, idle time is minimized, product throughput is increased and costs per cleaned unit are reduced. These improvements also apply to spray cleaning processes. In this case, additional nozzles are working in an optimized sequence to deliver a more effective cleaning performance, and consequently shorter cycle times, even when removing harsh contamination. In order to shorten cycles still further, the vacuum drying system available in addition to hot air drying has also been improved."
Due to the use of variable-frequency driven pumps, volumetric flow rates can be adjusted, resulting in energy savings. Additionally, the cleaning process can be selectively adapted to meet specific requirements. For example, different work chamber filling levels may be defined in the immersion processes to allow for filling and draining cycles that are suitable for cleaning parts having blind holes or complex geometries. An intense fluid exchange in critical component areas boosts the system's cleaning performance. In spraying processes, the jet strength can be adapted exactly to the part being processed. The ability to control the spraying pressure expands the range of cleaning agents that can be used.
Continuous processing of the rinsing fluid is provided by an Aquaclean system that can be integrated into the machine. The cleaning fluid in the first flooding tank is heated entirely by waste heat recovery from the evaporation process.
The EcoCWave has a vacuum-tight work chamber designed for batches measuring up to 670 x 480 x 300 mm. As an alternative, an enlarged work chamber for 670 x 480 x 400 mm containers may be installed without enlarging the footprint. The volume adapted batch configuration reduces per-unit costs.
A new color display with self-explanatory images is designed to make the EcoCWave easy, fast and reliable to operate. Diverse process data such as the work chamber fluid level are indicated in real time by the built-in process visualization system. The availability of all relevant process parameters (e.g., for the development of cleaning programs) can be implemented optionally.
An EcoCWave configured with two flooding tanks needs only approximately 59 sq. ft. of floor space. The EcoCWave features an integrated loading system and all-round safety-glass enclosure.
For more information contact:
Dürr Ecoclean, Inc.
26801 Northwestern Highway
Southfield, MI 48033
248 450-2000
sales.usa@ecoclean.durr.com
www.durr-ecoclean.com