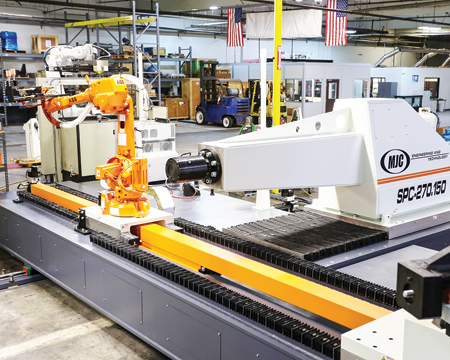
Machine designed by MJC Engineering to form 270" diameter aluminum sheets, typically 5/8" thick, into lip skins for the nacelle on the engines of Boeing 737MAX and 777X aircraft
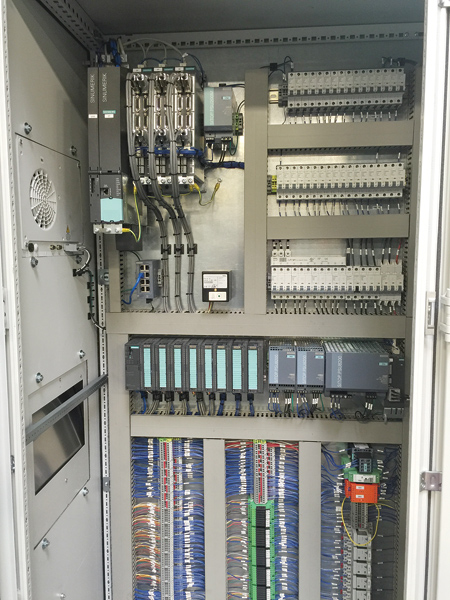
Siemens flagship Sinumerik 840D sl CNC, along with Sinamics drives, Simotics motors and Simatic PLC control the seven axes of motion on the machine and the 32 programmable movements of the robot, to which the heating torch is affixed.
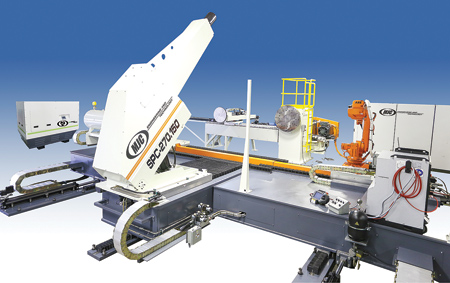
CAD illustration depicts the machine in operation, with worker shown for size relationship.
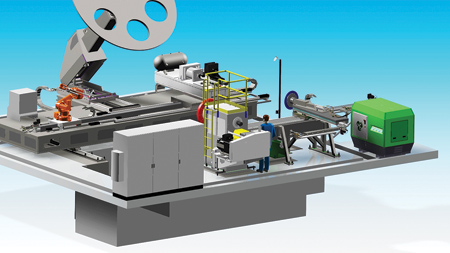
The MJC Engineering Green Power hydraulic unit is on the far left. Driven by Sinamics servo-pump from Siemens, this hydraulic power unit provides up to 40% energy-savings during operation.
MJC Engineering is a custom machine tool builder in Huntington Beach, CA, specializing in metal-spinning machines for such applications as sheet spinning, flow forming, wheel spinning and rotary forging. Recently, the company was commissioned to build a series of metal-spinning machines for GKN for use at its plants in Camarillo, CA, and Orangeburg, SC. These machines are currently in use, producing lip skins for the engine housings on Boeing 777X and 737MAX aircraft. "Using advanced CNC from Siemens and robotic handling technology, plus its proprietary servo-pump-controlled Green Power hydraulic power unit that saves up to 40% on energy, the team at MJC devised a unique solution to an engineering challenge, brought to them by GKN," said a company spokesperson.
The key aspects of the solution comprised how to spin-form production run components out-of-round by 8-1/2" to 9" in various aluminum alloy blanks measuring up to 270" diameters and 5/8" thickness, while holding tight tolerances to be verified by thermo-imaging cameras and fed back by the CNC for accuracy tracking, plus integrate the heating torch for in-process adjustments. Carl Lorentzen, President, MJC Engineering; Per Carlson, Vice President and General Manager; plus Don Hebert, Electrical Engineer, were involved in the task.
Each day at MJC, Lorentzen and his team combine this same metal-forming process that has been around for ages with modern CNC controls and robotics to create the state-of-the-art manufacturing process used to produce laminar flow lip skins for Boeing's newest flagship 737MAX and 777X aircraft. The lip skin is the highly engineered aerodynamic structure that makes up the leading edge of jet engine nacelles.
Metal-spinning is a forming process in which a blank of material is rotated on a spinning machine similar to a lathe. The blank of material is clamped onto a spin-forming mandrel and rotated by servo-controlled motors and drives. During rotation, heat is applied by a gas torch affixed to a robotic armature and a roller on the spinning machine makes contact with the part blank, forcing the part blank to flow over the spin-forming mandrel surface.
"Spin-forming, like no other metal-forming process, has the ability to form very large and thick plates quickly and accurately," said a company spokesperson. The 737MAX and 777X CNC metal-spinning machines built by MJC and currently located at GKN in California and South Carolina are reliant upon the precise and consistent application of heat throughout the metal-forming cycle. Even the slightest variation in heating would contribute to undesirable results in the formed part.
Until recently, manufacture of these lip skin components relied upon human intervention to control the direct application of heat throughout the spin-forming cycle. While this method could certainly produce a functional part, the associated variations in part consistency created downstream difficulties and challenges in subsequent fabrication and assembly operations. In the past, lip skins were produced by other methods, including draw-forming, bulge-forming and drop-hammering. The spin-forming and machining techniques now used at GKN have been found to reduce overall manufacturing time and tooling costs, while improving part consistency.
In an effort to reduce variation in the CNC spin-forming process to support high-rate programs such as the 737MAX and 777X, GKN Camarillo joined forces with MJC Engineering in Huntington Beach, to create an automated CNC solution. That solution is now a reality and consists of robots that apply heat in a precise and absolutely consistent manner, tied directly to a program that shapes the part. This careful interplay between the heating and spin-forming operations is made possible by the Siemens Sinumerik 840D sl CNC, which integrates and monitors every movement between the spinning machine controller and the heating robot controller, resulting in a smooth-flowing production scenario with perfect timing and high marks for efficiency, according to James O'Sullivan, GKN General Manager.
Before this combination, variation in product output was much less predictable. But today, part heating difficulties and variations are a thing of the past, according to Per Carlson of MJC. "CNC spin-formed lip skins with automated robotic heating exit the process as consistently as a stack of quarters, to draw an analogy. The results are no less than phenomenal, yet are derived from straightforward mathematical computations made possible by modern CNC technology from Siemens. Variation is the number one contributor to low manufacturing yields and increased operating costs. Study your process, understand where variations occur and then eliminate them with cost-effective solutions. The improvement literally catapults a production floor to new levels of manufacturing excellence. It certainly has at GKN."
In operation, the machine takes the overhead crane-loaded 270" diameter blank, fixes it to the tailstock of the machine and rotates it on a 150 HP motor-driven spindle, then progressively applies heat via the gas torch on the robot arm. Raytek thermal imaging cameras closely monitor the heat readings over the entire surface to create multiple control cones. When inconsistencies are detected, the heat is appropriately adjusted in real time by the controllers. The heated material is then formed over the mandrel into the desired size, with out-of-round conditions ranging from 8-1/2" to 9" typically. Siemens Simatic S7 PLC technology is onboard the machine, controlling the various mechanisms, while the CNC integrates and feeds back all data.
Solid Edge is the CAD program for the design of the lip skin, while Siemens NX CAM translates the design data into machine execution steps. Each MJC machine involved in this project also incorporates Sinamics drives and Simotics motors from Siemens. As electrical engineer Don Hebert explained, "There are seven axes of motion controlled by the CNC. We created custom screens for teach-in and playback on the machine to facilitate faster commissioning and troubleshooting onsite for the GKN operators. Zone Pro and Spin CAD were used to create the tool paths. On the robot, there are 32 pre-programmed moves, fully integrated with the heating and thermal imaging processes. The robot runs with an external PLC through G-code on the CNC, which dictates the on/off heating and cooling controls, based upon feedback from the temp zones monitored."
Carlson added, "From the time we built the first machine for Camarillo to the latest machine in Orangeburg, we have transitioned to newer technology; that is how fast things are moving."
Lorentzen concluded, "When we were also able to provide our proprietary Green Power technology and, in the process, save the customer substantial energy costs, the advantages of this machine design ratcheted up to a great degree. Using Sinamics servo-pump technology, Green Power provides exactly the hydraulic pressures needed, offering the customer energy-savings up to 40%, compared to a conventional 'constant on' hydraulic pump motor manifold."
For more information contact:
MJC Engineering & Technology, Inc.
15701 Container Lane
Huntington Beach, CA 92649
714-890-0618
www.mjcengineering.com