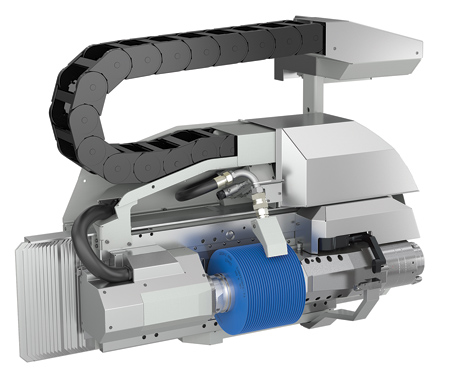
Largest grinding head for optimum service life and chip removal performance
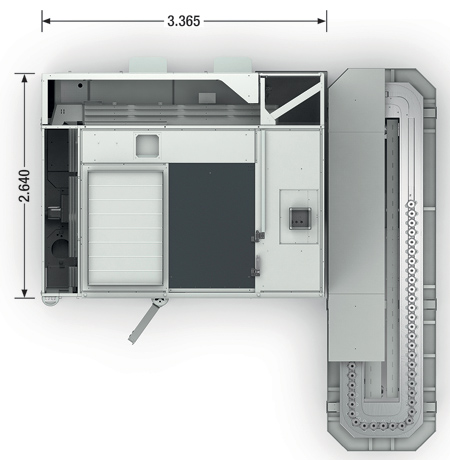
The space requirement of each machine compared
Liebherr-Verzahntechnik GmbH has expanded its LGG range of grinding machines. The standard LGG 180 / 280 machine has been upgraded to an LGG 180 / 280 L "large version" to meet special customer needs. A new machine for large workpieces, the LGG 300 / 500, has also been added to the lineup. Liebherr is introducing new grinding heads for all LGG machines.
The LGG 180 / 280 L combines typical mass-market requirements with those of job shops. "As a single-table solution with only one clamping fixture, it can machine planet and sun gears, ring gears and beveloids very cost-effectively - achieving short load / unload times often less than four seconds," said the company spokesperson. This machine can also grind drive and output shafts - the "large" version can handle shafts of up to 660 mm long. Longer shafts can be accommodated upon request. Given its increased working space, it is suitable for machining smaller batches typical in job shops and aerospace suppliers.
The new LGG machines are ideally suited to generating grinding of tooth-flank modifications.
- TF - Twist-Free
- DFT - Deviation Free Topological
- NEO - Noise Excitation Optimized modification
- GER - Generated End Relief
- SSG - Silent Shift Grinding
- DIP - Dresser Independent Profile modifications
"The LGG 300 / 500 provides state-of-the-art grinding technology in a relatively compact footprint for parts up to 500 mm in diameter," said a company spokesperson. "Modern materials are the basis for a highly thermostable grinding machine. The fully enclosed machine and direct-drive system deliver maximum quality over the grinding machine's entire service life. Like the smaller LGG 180 / 280, the LGG 300 / 500 has been approved for the use of grinding tools with cutting speeds of up to 100 m/s. The new LGG 280 L and LGG 500 also utilize the GH 6.0 grinding head featuring grinding worms with diameters up to 320 mm."
Enhanced Design Grinding Heads
Liebherr uses an automatic, spindle-integrated, two-level balancing system for its new GH 5.0 und 5.1 grinding heads. Depending on which version is used, the grinding arbor is clamped using HSK 50 / 40 or 40 / 32 tapers. The smaller interface is located on the counter-bearing in each case. That enables small grinding worms to be used, which is particularly important for grinding of tooth-trace modifications. Smaller worms also make it possible to grind parts with clearance restrictions. Since the balancing heads are positioned outside the grinding arbor, they are less expensive to produce and not sensitive in terms of handling. The larger GH 6.0 grinding head features this two-level balancing system in the arbor. The interface on both sides is an automatic HSK 80. These are even more rigid and can handle even larger tools.
These new grinding heads were engineered to allow for the use of multi-rib dressing tools, without making the grinding arbor unnecessarily long. Short distances between grinding worm ends and spindle bearings ensure maximum rigidity. All new grinding heads (GH 4.0, GH 5.0, GH 5.1 and GH 6.0) can be used on the LGG 180 / 280 L machine. Combining the LGG 180 / 280 L with the large GH 6.0 grinding head enables shafts or gears to be machined on a relatively small machine. All grinding heads can be used on the LGG 300 / 500, although the grinding head of choice would be the GH 6.0. The proven characteristics of the LGG 180 / 280, such as a high degree of machine thermostability and fast installation, are retained. A further benefit is the ability to grinding internal gear teeth - making the machine an all-purpose basic tool.
For more information contact:
Liebherr USA
1465 Woodland Drive
Saline, MI 48176
734-429-7225
info.lgt@liebherr.com
www.liebherr.com