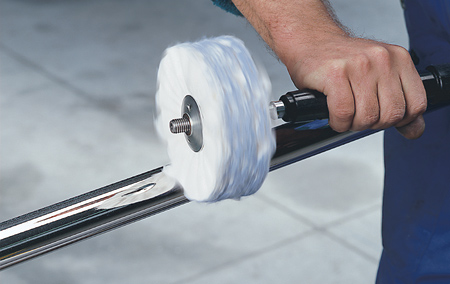
The final step in achieving a mirror finish on a stainless steel tube is using a buffing wheel and polishing paste.
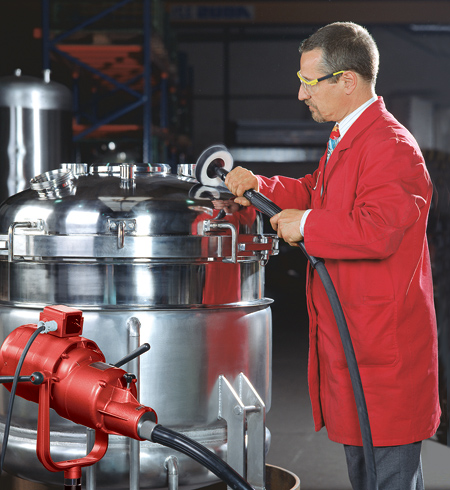
A nylon flap brush, followed by polishing with a buffing wheel and cutting/polishing compound, can create a satin finish on a pressure vessel.
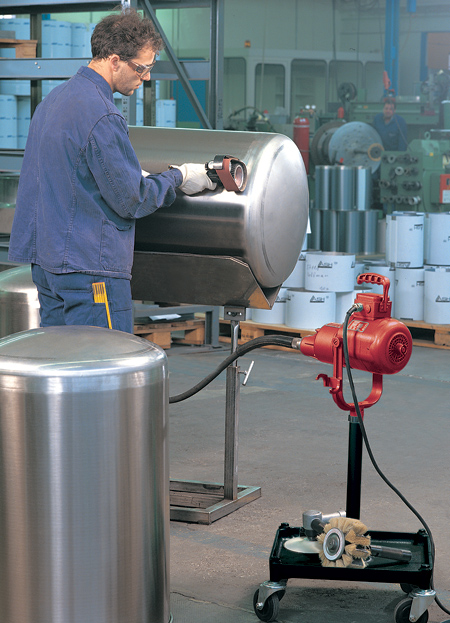
Grinding on a cylinder surface is made easier with a flex shafted tool, so the weight of the power unit is not carried by the operator.
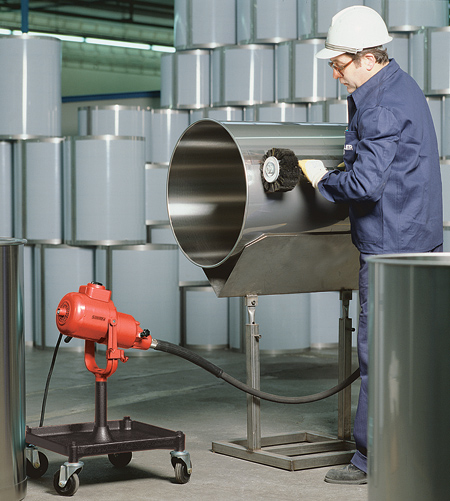
Tube polishing is made easier with an independent tool.
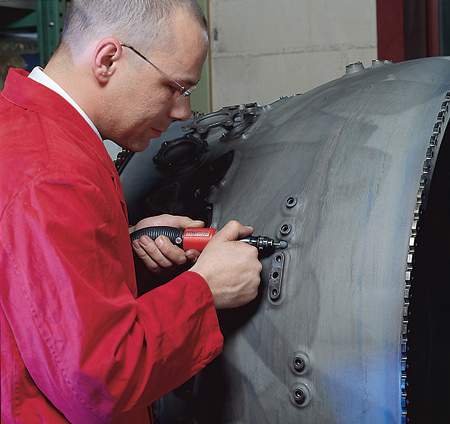
Precision drilling work is possible on a contoured surface with a handheld unit.
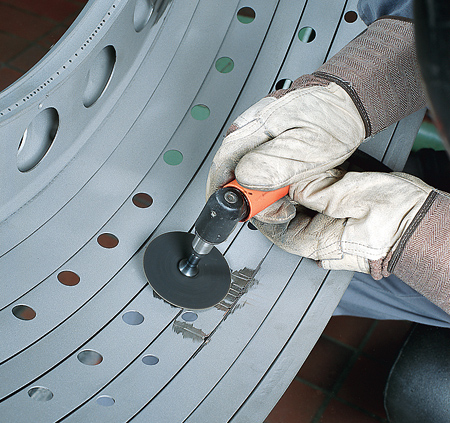
Deburring multiple holes on a stainless workpiece
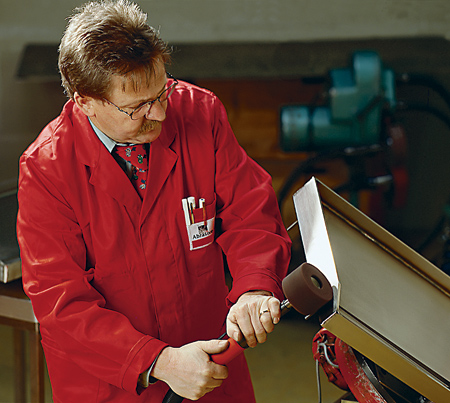
Endpiece and decorative plate edge polishing is made easier when the light weight of the tool allows multiple movements.
Fine grinding, by definition, is the blending of the weldment to the surface of the metal for a smooth, consistent and attractive appearance. When working on stainless steel grades - whether for appliances, structural parts, sheet metal housings that are visible on the finished product without being painted or coated, or architectural adornments - choosing the right equipment and consumables for each step of the process will help produce the desired result.
Following are some typical applications and tips on how today's handheld grinding equipment and consumables can affect a better outcome in the shop or production department.
Blending Welded Connections on Railings
Blending welded surfaces on corners, squares and rounds is the key to producing attractive welded connections on railings. Use 40, 60 or 80 grain belts in a belt grinder to grind down the weld. Then, use a coarse, medium, fine or ultrafine conditioning belt to blend the surface. For flat surfaces, use an elastic drum and nonwoven nylon flat brush. For pipes and tubes, use a tube polishing wrap. Grain sizes to 320 will produce the desired results, even on extremely small radii.
The proper use of the regulated speed on the grinder will help operators achieve the optimal finish, so choose tools with speed regulators. An adjustable belt grinder arm on the tool will make the tool easier to use, lessen operator fatigue and yield better results.
Prepping and Finishing on Pressure Vessels
For a typical No. 4 finish with RA 15-25 on a pressure vessel, use a 40- to 320-grain belt grind and finish with a flap brush. A satin finish can be achieved by using a nylon flap brush followed by polishing with a buffing wheel and a cutting/polishing compound.
Many popular tools offer quick-change tooling systems to reduce downtime and many are portable. Operator fatigue is reduced when the portable tools have detachable hand pieces so the weight of the entire drive unit does not need to be carried. Some models are available for working in very confined and hard-to-reach places.
Look for dust-sealed units with low noise levels and vibration-free operation. Air-cooled induction motors provide long service life and minimum wear.
Grinding Work on Commercial Foodservice Grills
Reducing surface weld beads is a key challenge when working on commercial grade foodservice grills. Start by rough grinding with a pneumatic grinder with 36 to 80 grit discs. Finish grind with a pneumatic drum with a 40 to 220 grit abrasive belt.
Then, work all surfaces with an extended pneumatic straight grinder and 60 to 240 grit fiber brushes. Finishing discs of synthetic fiber, grit and resin will eliminate welding discoloration.
Polishing Stainless Steel Tubes to a Mirror Finish
To polish a stainless steel tube to a mirror finish, begin by preparing the surface with a belt grinder using an 80 to 120 grit zirconia belt. Then, switch to a surface conditioning belt for medium to ultrafine finishes. Use a pre-polish wheel and polishing compound.
Polish with a polishing wheel and polishing compound, and then complete the mirror finish using a buffing wheel and polishing paste.
Grinding Weld and Miter Joints on Structural Steels
Remove the weld beads from structural steel miter joints using 60 to 150 grit zirconium fiber discs. Then, use a drum sander with a 40 to 220 grit zirconium blend belt. Cover with a template.
Use a surface conditioning belt for a fine finish. For a satin finish, use a 100 to 200 grit fine flap brush.
Graining of Stainless Steel Welds
Begin the graining process on a stainless steel weld with a pregrind using a pneumatic right-angle grinder with a plastic support plate with a cooling effect and an 80 grit fiber disc. Finish with a pneumatic drum using a straight grinder.
Grain the surface using a right-angle grinder with nonwoven, medium or high hardness finishing discs. Grind the weld bead with a 120-grit grinding belt and a 40 to 320 grit finishing belt.
Eliminating the Orange Peel Effect
To smooth the orange peel effect, begin with a rough prep using a 40 grain belt. Then fine grind with a soft contact roller and A160 Trizact belt. Satin finish with a soft contact roller and medium surface conditioning belt.
Achieve an industrial-grade finish by using a flap brush and 220 grain abrasive pad.
Grinding Inside Corners on Stainless
To finish the inside corners of a stainless steel component, begin by smoothing the weld with an electric angle grinder with an 80 grain mini flap wheel. Then, fine surface grind using an electric angle grinder and soft disc - between an A160 and A16 grain - with a Trizact grinding wheel.
Use an electric file and between a 60 and 400 grain range nonwoven pads to define the surface grain.
Grinding and Polishing Extruder Feeds
Start with a preliminary grind on an extruder feed shaft using a belt grinder and between a 40 and 80 grain zirconium corundum belt to grind and polish extruder feeds. Work the flanks with 80 to 120 grain Velcro fiber wheels. Fine grind the shaft and flanks with a roll attachment. Polish with twisted polishing rings and polishing paste, especially when working with stainless.
The guidelines here provide a starting point to plan finishing jobs, but most tool and abrasive suppliers are ready to offer suggestions for everyday or particularly challenging applications. If you have questions, take advantage of their experience.
Authored by Aaron Beck, National Sales Manager, Abrasives and Power Tools, Suhner Industrial Products
For more information contact:
Suhner Industrial Products, LLC
Hwy 411 S. / Suhner Drive
P.O. Box 1234
Rome, GA 30162
706-235-8046
info.usa@suhner.com
www.suhner.com