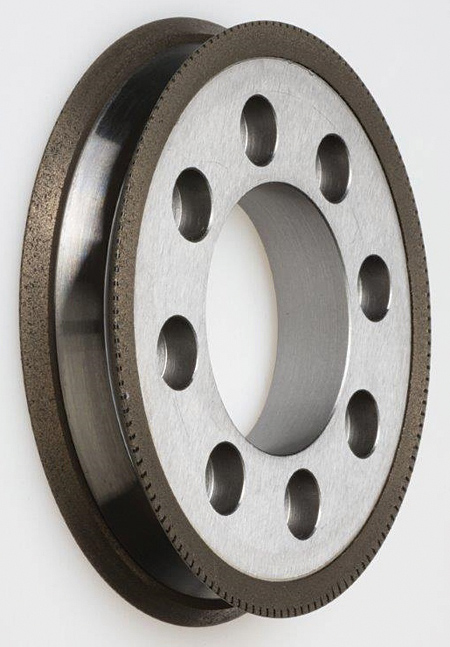
Meister's new micro-precision CNC Dressing Tools are suited for grinding applications with form tolerances down to 2 µm.
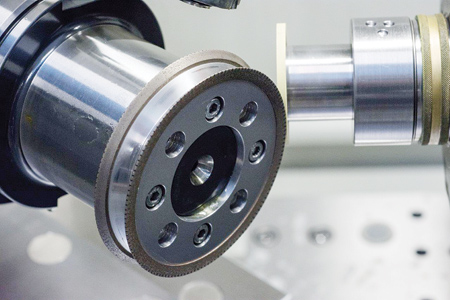
Suited for truing and sharpening of grinding wheels used with automotive and aerospace bearing races, high-precision gear grinding, plunge grinding of fuel injection armatures and needles and other demanding applications."
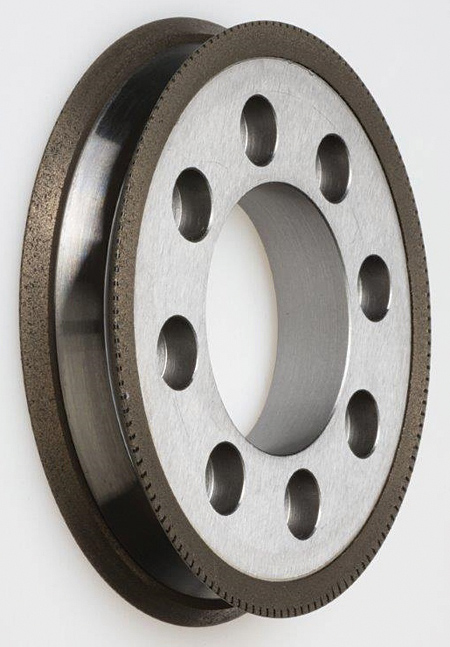
Meister Abrasives USA, Inc. has introduced a new generation of cDD Diamond Dressers that deliver certified, tight tool radius tolerances which are essential for today's most demanding micro-precision grinding applications. The radius form tolerance of these new micro-precision diamond dressers can be certified accurate to within 2 µm (+/- 0.001 mm) if the application requires.
Bruce Northrup, Vice President and General Manager of Meister Abrasives USA said, "To dress grinding wheels for ultra-high precision applications the user needs to have a precise, certified radius value to plug into his CNC dressing program. Very few dressing wheel manufacturers have been able to achieve this degree of certified precision. Meister's introduction of micro-precision certified cDD dressers is the result of a multi-year R&D project which culminated in a major investment in manufacturing, measurement and verification systems."
This degree of certified precision makes micro-precision cDD Diamond Dressers suitable for the CNC truing and sharpening of grinding wheels used in manufacturing automotive and aerospace bearing races, high-precision gear grinding, plunge grinding of fuel injection armatures and needles and other critical grinding applications that require form tolerances as tight as 2 microns.
"Meister Abrasives broke into new territory with the introduction of diamond dressers that excelled both at truing and sharpening CBN wheels," said a spokesperson. These cDD dressing tools rely on a unique structure in which high quality CVD diamond inserts are strategically embedded within Meister's hDD porous hybrid-bond matrix.
According to Meister, the cumulative advantages of the cDD technology for both dressing and subsequent grinding processes are:
- Superior truing (accurate and consistent profile generation on the grinding wheel)
- Superior sharpening (does not dull the grinding wheel)
- Low dressing forces
- The grinding wheel cuts better and achieves better part quality
- Lower dress in-feed or higher skip dress is possible
- The dressing tool stays sharp (no conditioning required).
For more information contact:
Meister Abrasives USA, Inc.
201 Circuit Drive
North Kingstown, RI 02852
401-294-2530
sales@meister-abrasives-usa.com
www.meister-abrasives-usa.com