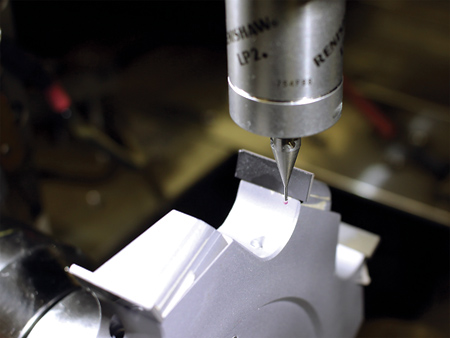
Probing the rough product
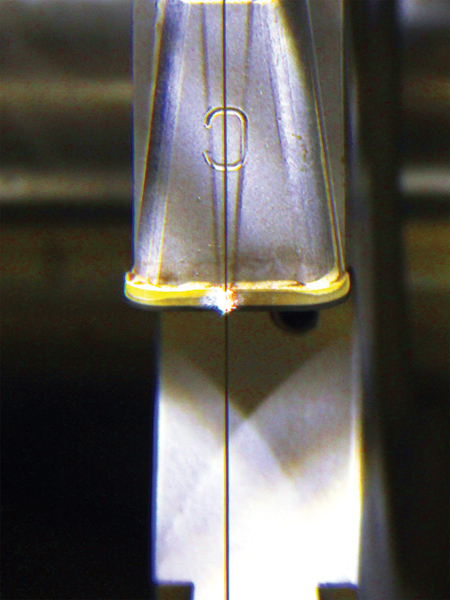
An underwater view of the EDM process on the FANUC RoboCut.
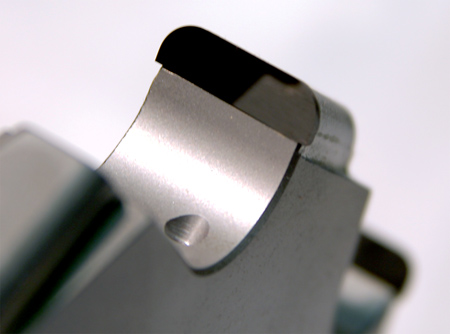
A close-up of the finished edge cut onto the diamond.
Competitive Carbide Inc. manufactures application-driven special carbide cutting tools in quantities ranging from one to hundreds of pieces. The company needed a way to quickly and accurately EDM polycrystalline diamond (PCD) cutting tools in a seamless process, from set-up through production. Edge integrity was of paramount importance, along with the ability to rotate parts underwater and cut intricate forms.
PCD inserts feature a diamond cutting edge that provides wear resistance and high cutting precision, particularly in non-ferrous materials. PCD is a composite of diamond particles mixed with a metallic binder that, together with a carbide base, is sintered and then cut into shapes or blanks. The composite blanks are then brazed onto inserts or tool shanks, finish cut and ground if necessary.
Optimized Turn-Key Solution
To manufacture the PCD inserts, Competitive Carbide selected as its solution a custom turn-key system from Methods Machine Tools, Inc., a FANUC RoboCut supplier. Methods is the exclusive North American source of sales, service and training support for FANUC vertical machining centers and wire EDM machines. The solution consisted of a FANUC RoboCut CiA-Series wire EDM equipped with a Hirschmann 4th axis underwater table and Renishaw probe.
Competitive Carbide also opted for PCD Edge software, which is designed to speed and simplify wire EDM profiling of complex edge contours on PCD cutting tools. "The PCD Edge software can program the part from a DXF file, probe the part to orient it and correct any discrepancies in prewire manufacturing," said Tom Cirino, President, Competitive Carbide. "For example, if a tooth is off by one or two degrees, the software will probe every tooth for flatness or angularity and then correct for these discrepancies."
According to Cirino, the entire turn-key package has met every challenge. "We have fast set-ups, excellent dimensional quality and very fine edge quality," he said. "We have yet to find a problem or tool that the turn-key has not been able to handle."
Competitive Carbide cuts steel, carbide and PCD parts on the turn-key solution, each with their own power settings, which can be optimized.
Standard features of the RoboCut CiA-Series:
- Discharge control AiP2: By accurately counting the number of effective discharges and monitoring the uniformity of energy density and the discharge gap, AiP2 enables high precision cutting at high speeds.
- Anti-recast power supply
- Auto wire feeding AWF2 measurement function
- FANUC 31i-WB controller
- Wire size: .004" to .012" (.002" optional)
- Inverter controlled chiller
- Cutting and power consumption monitor functions
- Positioning accuracy: ± .0001"
- Linear glass scales (.000004").
Nano Interpolation, with servo commands to 0.00000004", is standard on all CiA-Series machines. With Nano Interpolation, an accumulation of axis movement errors is eliminated, resulting in high workpiece tolerances. Smooth axis motion and enhanced circularity is possible even at high speeds.
The RoboCut's auto wire feeder anneals wire over the entire Z-axis, eliminating misfeeds and increasing threading reliability. The AWF2's Intelligent Retry Stroke function detects wire deflection and automatically searches for the start hole. The Twin AC Servo Wire Tension Control reduces tension variation, enhancing cutting accuracy and surface finish. The Ai Auto Repair System can thread through the kerf while submerged to a depth of up to 6.0" without returning to the start point.
The FANUC Series 31i-WB LCD touchscreen selection uses dedicated menu keys and split screen displays, allowing operators to monitor multiple functions. FANUC's high-speed controller incorporates five microprocessors, fully digital technology and fiber optic cable to help provide ease of use and reliability.
The PCD Edge software system combines sophisticated cutting functions with automatic precision measuring of 3-D plate positions (rake angle and shaft angle). The software allows adjustment of the relief angle on each contour element.
With PCD Edge, operators design tool edge contours in their own CAD system. When the design is complete, the operator simply exports the file in DXF format for importing into the PCD Edge software. PCD Edge allows operators to proof their programs by reviewing a contour cutting simulation with relief angle representation.
Competitive Carbide has several FANUC RoboCuts, including a 1iC, 1iE, C400iA and two C600iAs. According to Cirino, "The EDMs provide outstanding accuracy and surface finish."
Exceeding Quality Special Cutting Tool Needs
Competitive Carbide designs and builds special indexable cutting tools, solid carbide round tools, PCD diamond round tools and special form inserts at a state-of-the-art manufacturing facility, utilizing only the latest in machine tools and software to create customers' special tooling needs. It is committed to providing total customer support in every area, from design to manufacturing implementation.
Competitive Carbide's manufacturing methods are "fixture based" on 5-axis equipment in each department. The company's dedicated employees are constantly focused on the quality and accuracy of each and every job.
"When working with Competitive Carbide, you speak directly to our engineering staff to design and ensure the correct tool for your particular application," said Cirino. "This includes your preference of industry standard inserts and hardware.
"The goal is to be a complete solution for a large variety of industrial needs with our special cutting tools. Our engineering department uses 3-D modeling software, which gives us the ability to create and examine the tools we design like never before, helping to eliminate errors and giving our customers the confidence that the cutting tools we manufacture will do the job they are designed to do."
Quality starts in the engineering room, where everything from that point is solid model driven. All CAM and inspection machines have their programs written off of these models to reduce errors in checking a tool for conformity.
"With quality, consistency and the customer in mind, let Competitive Carbide show you how we can turn your manufacturing line into a profit powerhouse," said Cirino.
Competitive Carbide was founded in 1991. The Cirino family has been in the cutting tool business for over 70 years.
For more information contact:
Tom Cirino, President
Competitive Carbide Inc.
9332 Pinecone Drive
Mentor, OH 44060
440-350-9393
tcirino@competitivecarbide.com
www.competitivecarbide.com
Methods Machine Tools, Inc.
65 Union Avenue
Sudbury, MA 01776
877-MMT-4CNC (877-668-4262)
www.methodsmachine.com