
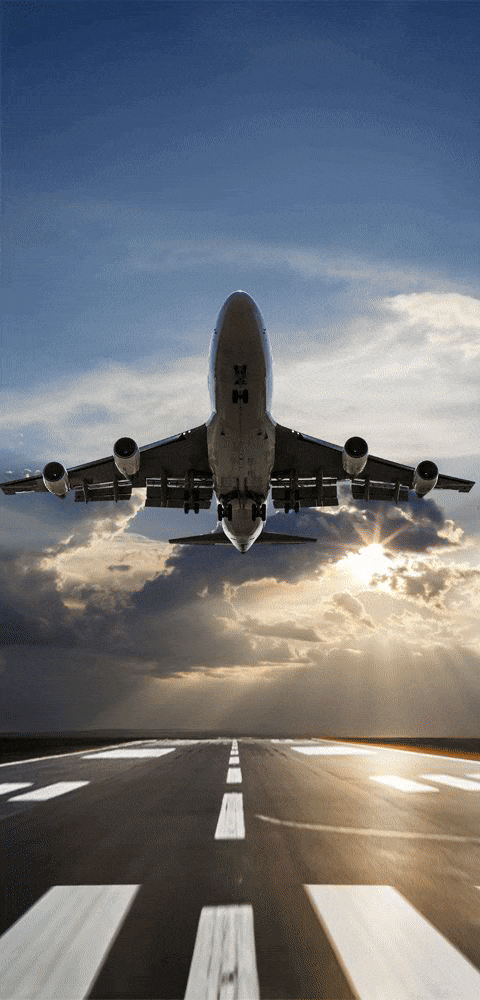
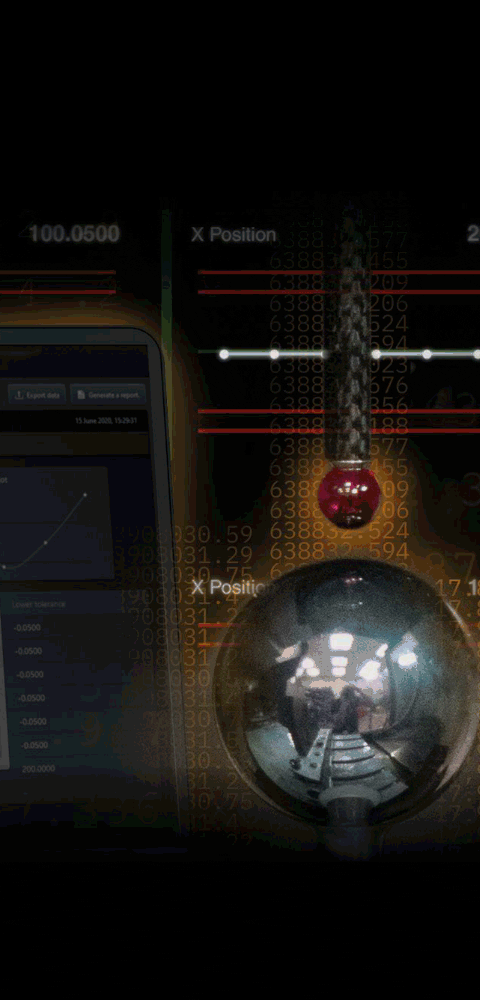
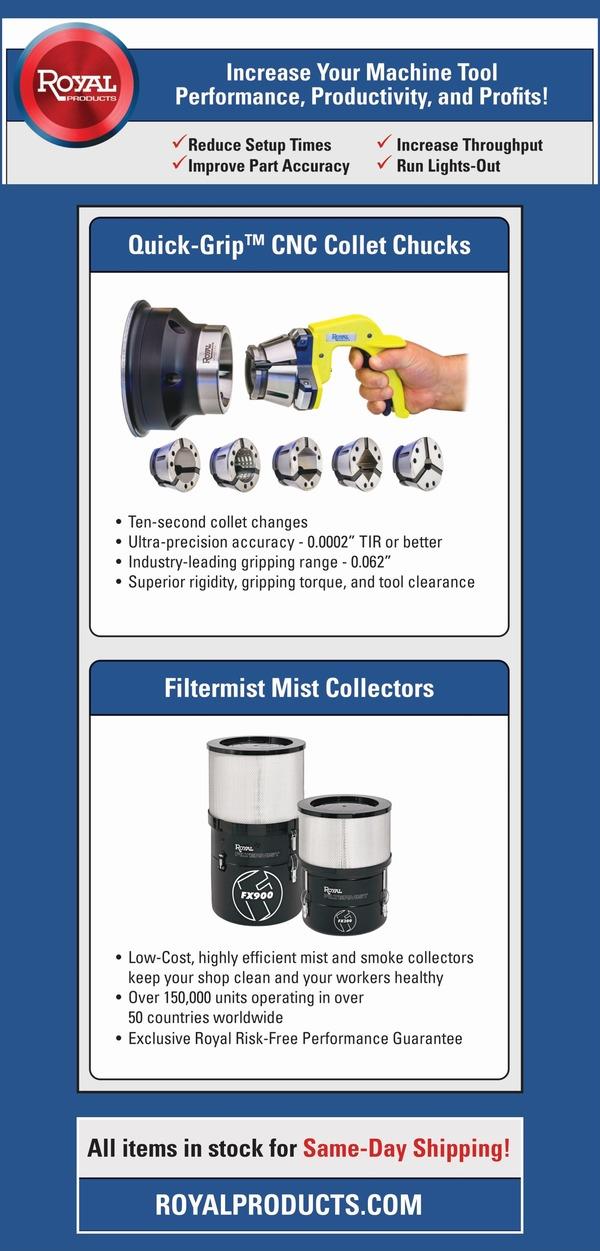
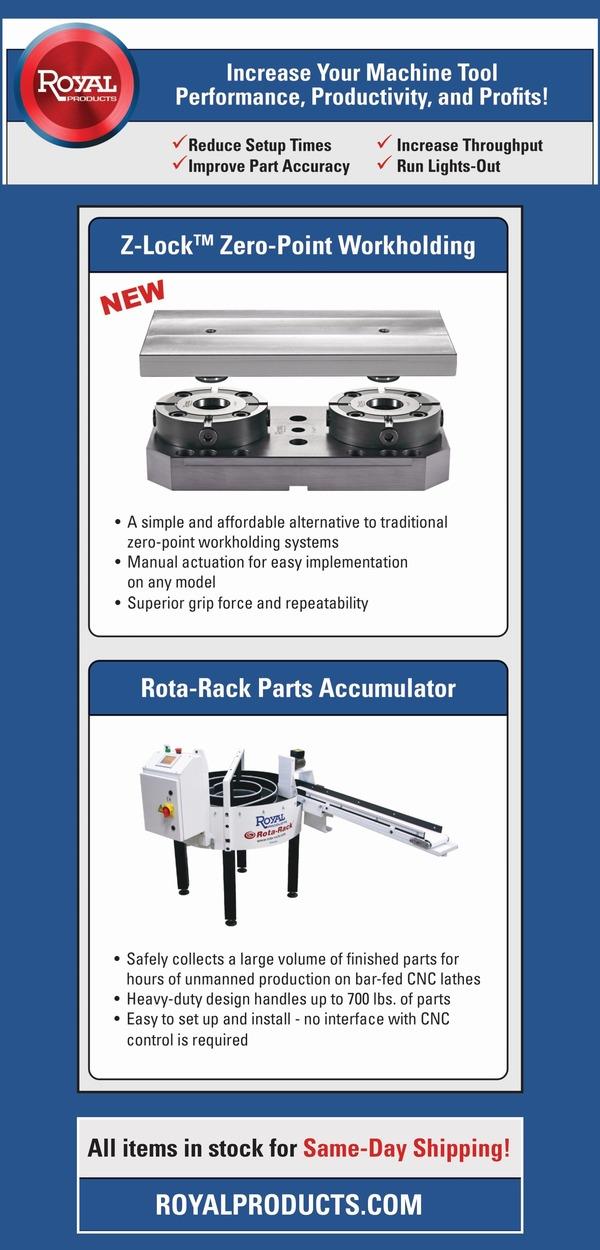

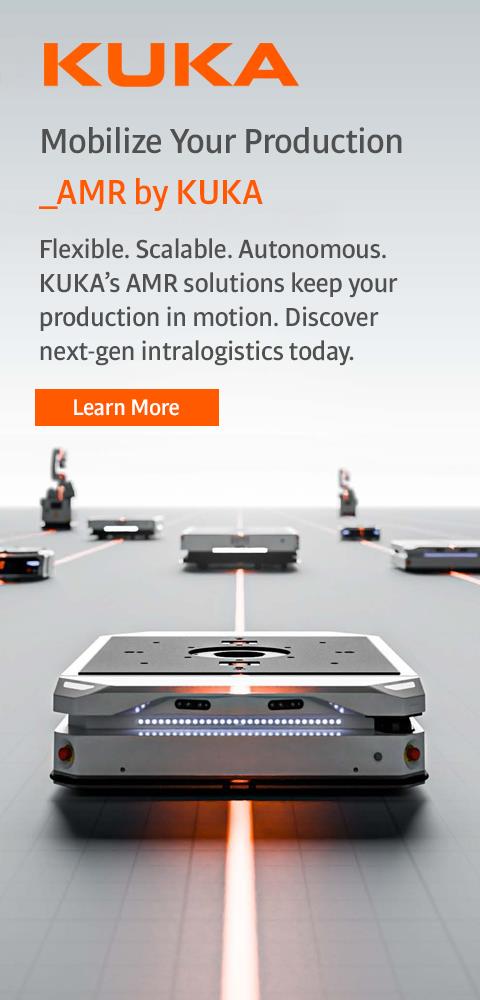
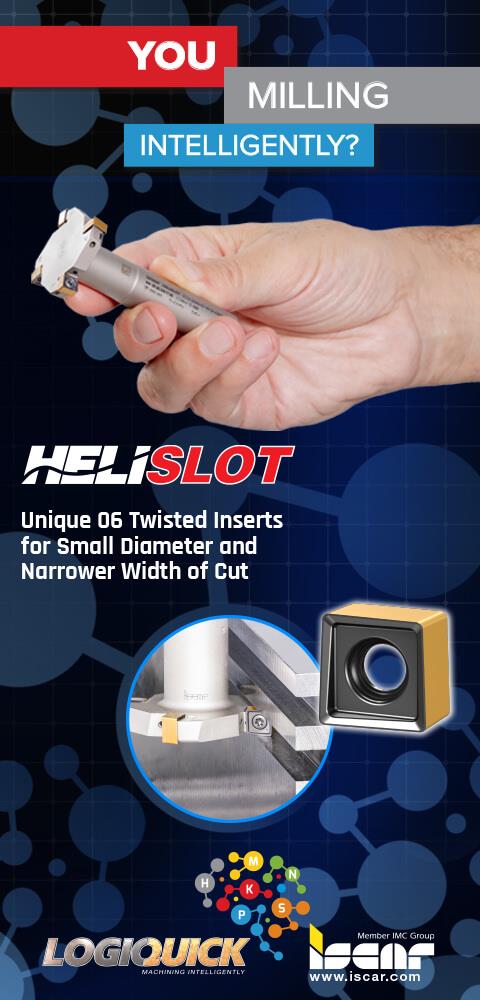
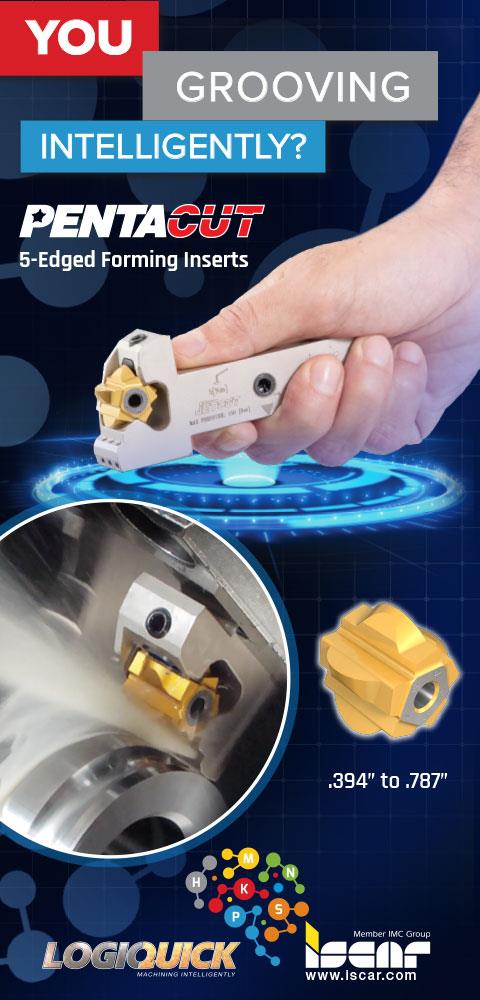
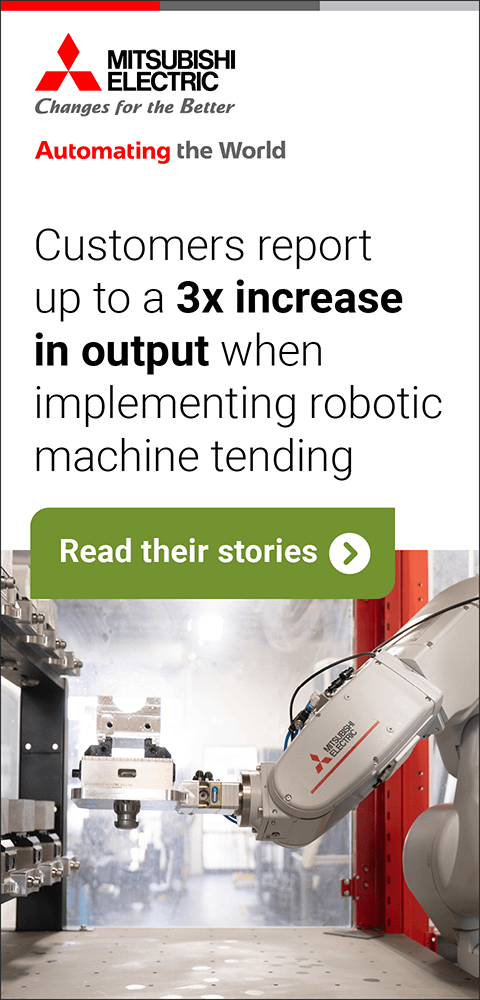
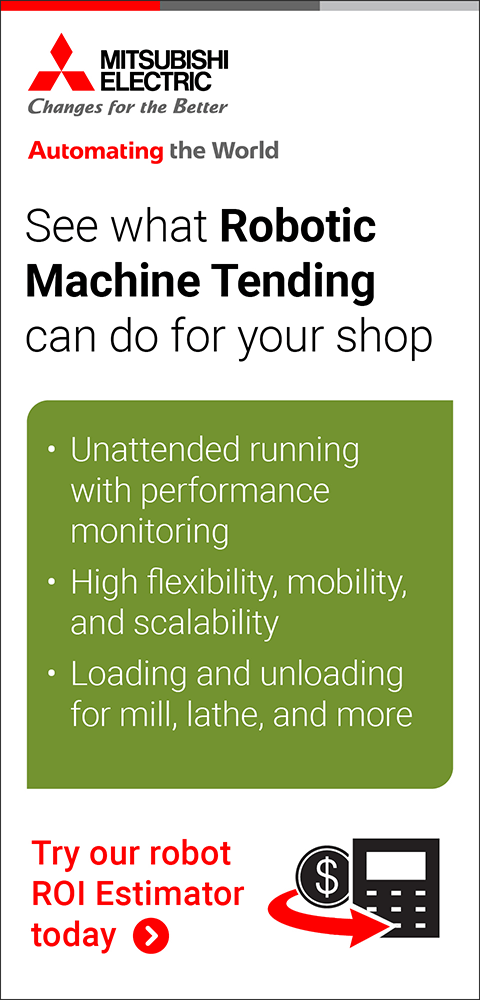
Modular System for Direct Workpiece Clamping
February 1, 2016
"Applications that require minimal batch sizes, high precision requirements and complex geometries need high-tech solutions to get the job done. SCHUNK's new modular system for direct workpiece clamping designed for complex jobs," said a company spokesperson.
"Modular clamping columns enable direct clamping of molding plates, free-form parts and other workpieces on the machine table within seconds, without additional clamping devices or interfering contours. The clamping pillars are built to guarantee collision-free processes, a defined clamping situation and a reliable simulation of the machining. In addition, changes in the workpiece can be implemented quickly due to the high precision of this clamping solution," said a company spokesperson.
The modular system consists of VERO-S WDB base modules for the machine table, VERO-S WDN clamping modules (o 99 mm) and combinable VERO-S WDS stacking modules. The latter have a standardized height of 30 mm and 50 mm, to allow fine graduations of 10 mm in the height of the clamping columns starting at a height of 80 mm. The connections between the single modules are designed for high machining parameters, with a high pull-in force of up to 25,000 N. To help ensure distortion-free workholding, height differences can be compensated by an adjustable, hydraulically clamped VERO-S WDA compensation element.
All interfaces feature scope-free taper centering, which is designed for a repeat accuracy of < 0.005 mm between the single components. An integrated air feed-through allows actuation of the clamping modules and monitoring of the presence of a workpiece. The workpieces themselves remain securely clamped even if the pressure in the air system should suddenly drop. A pneumatic system pressure of 6 bar is sufficient for opening the clamping modules. "For a longer life and increased process reliability, all functional parts such as the base body and slide assemblies are made of hardened stainless steel, are corrosion-resistant and easy to clean," said the spokesperson.
For more information contact:
SCHUNK Inc.
211 Kitty Hawk Drive
Morrisville, NC 27560
919-572-2818 / 800-772-4865
info@us.schunk.com
www.schunk.com
< back