

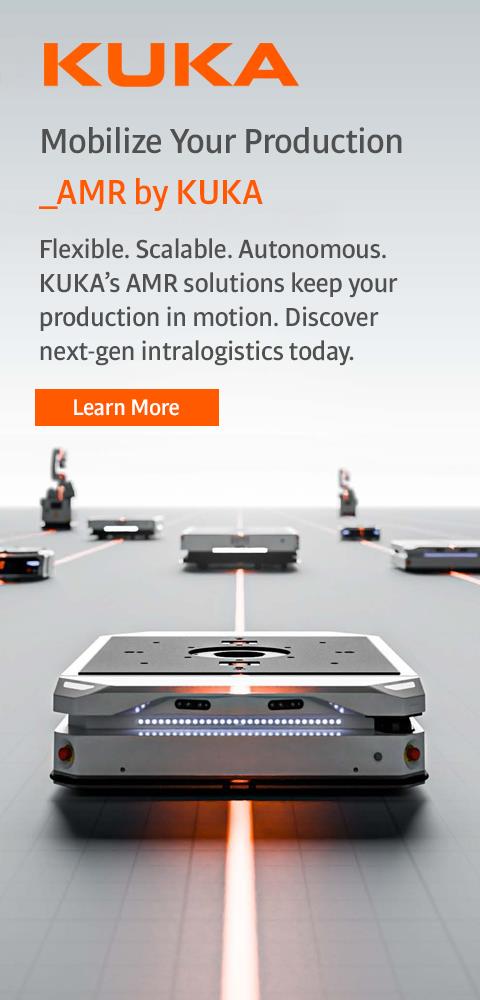
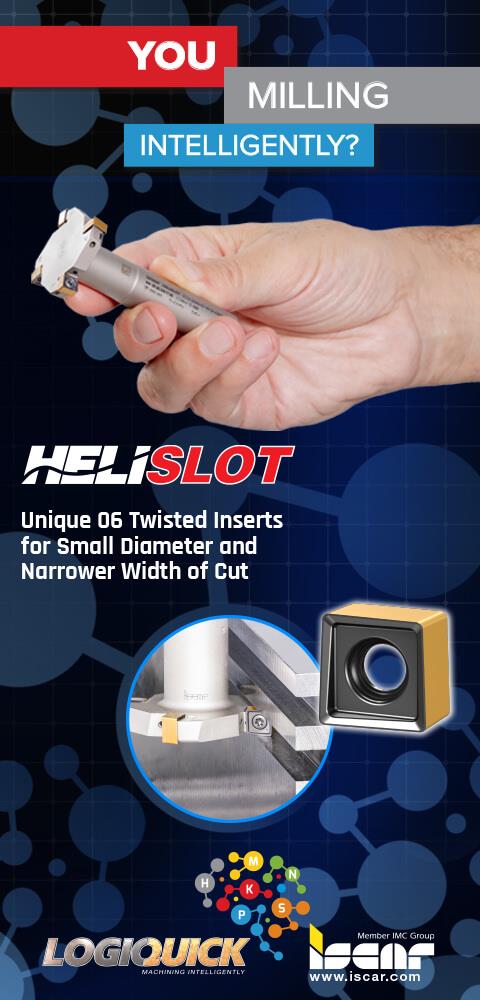
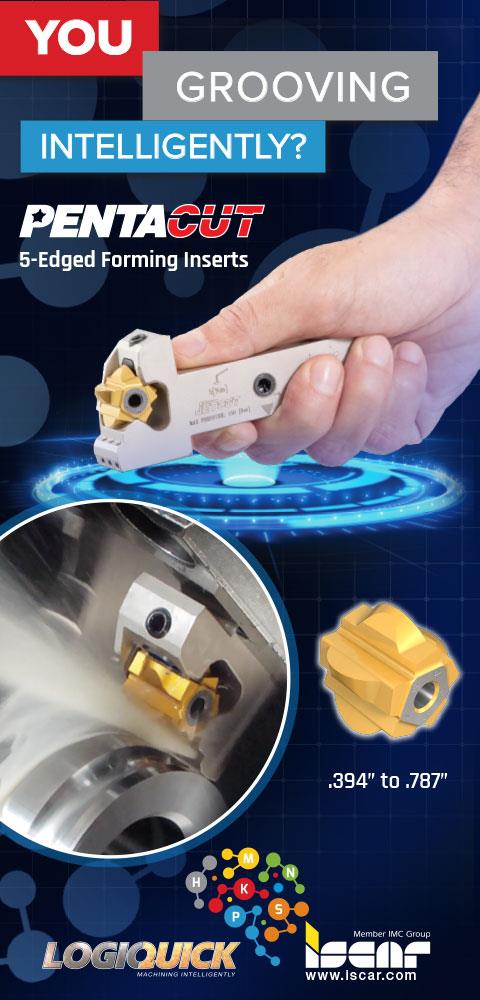
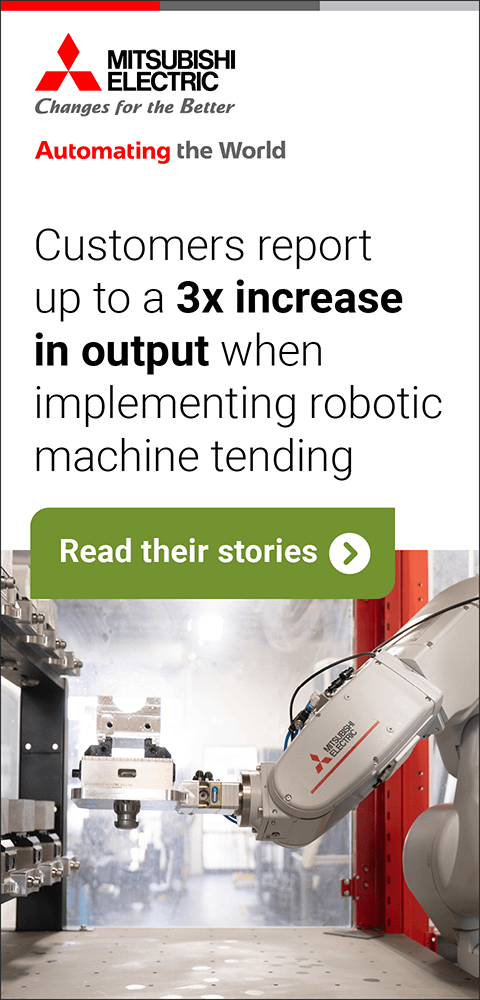
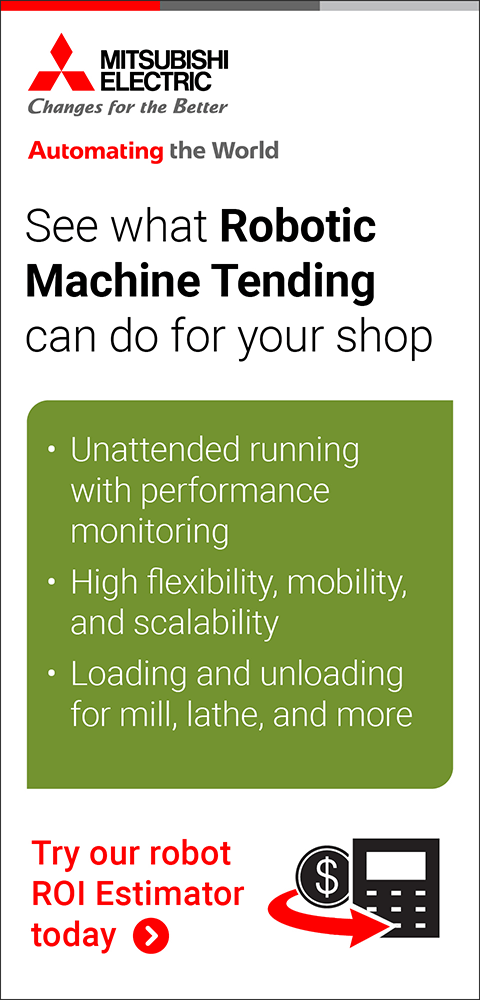
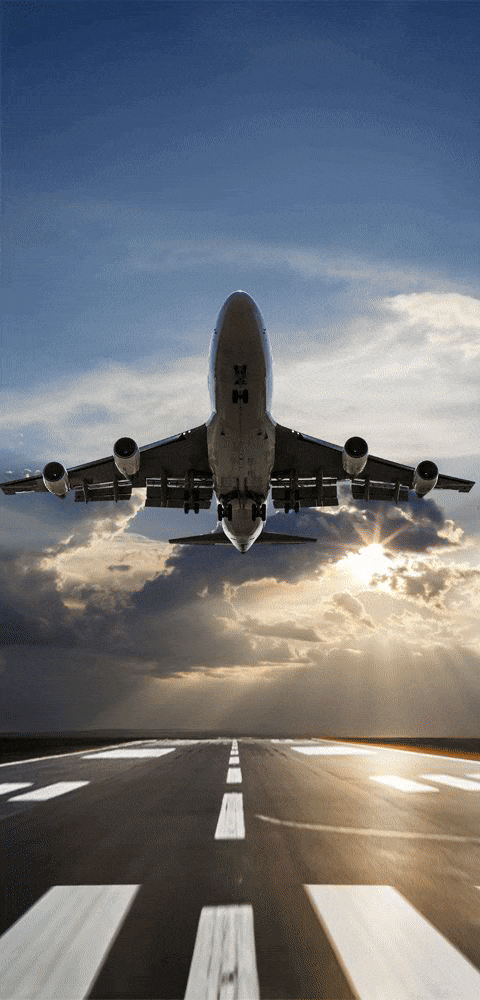
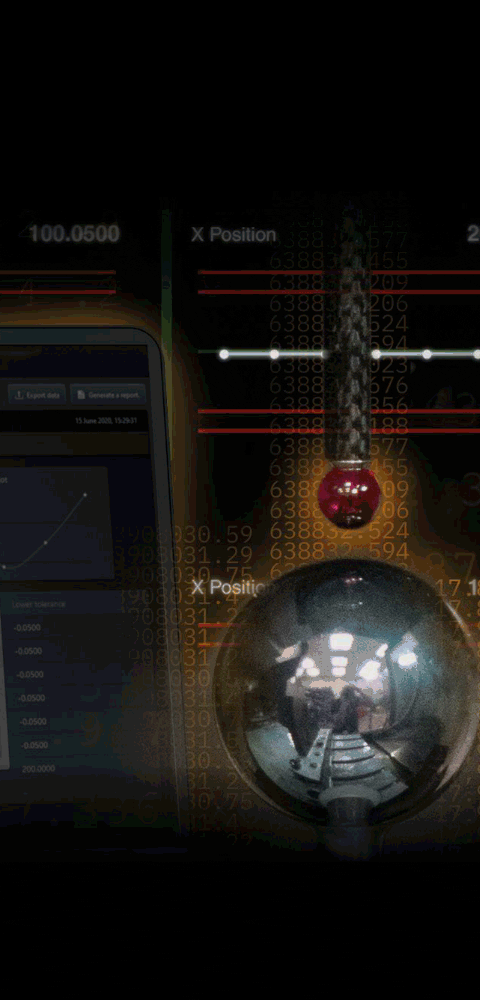
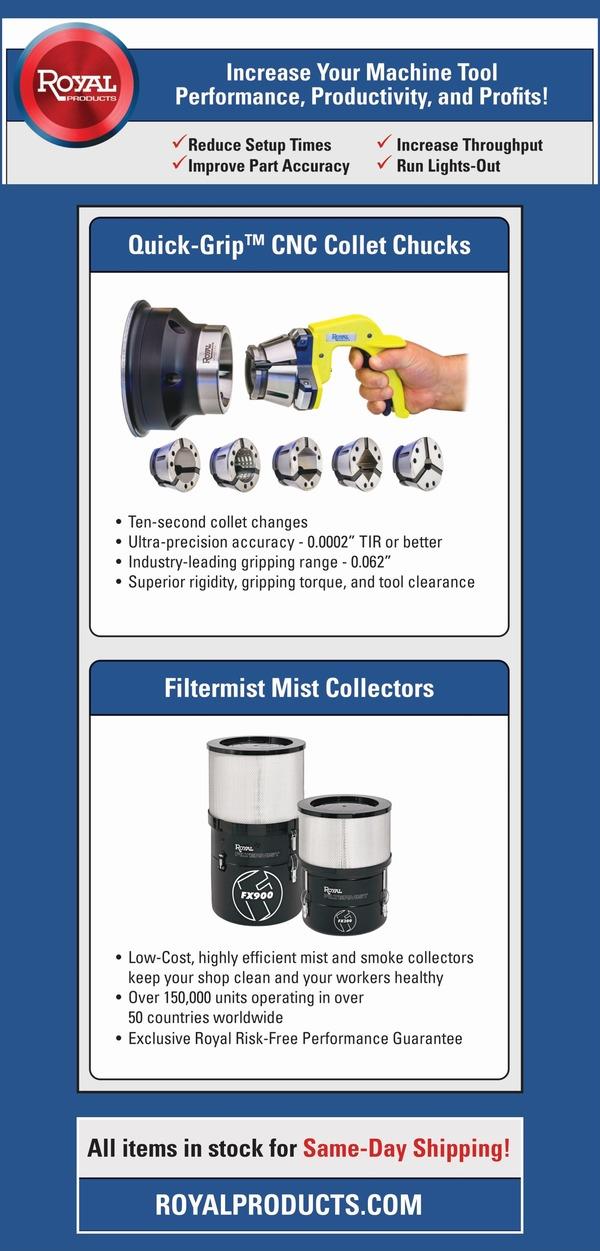
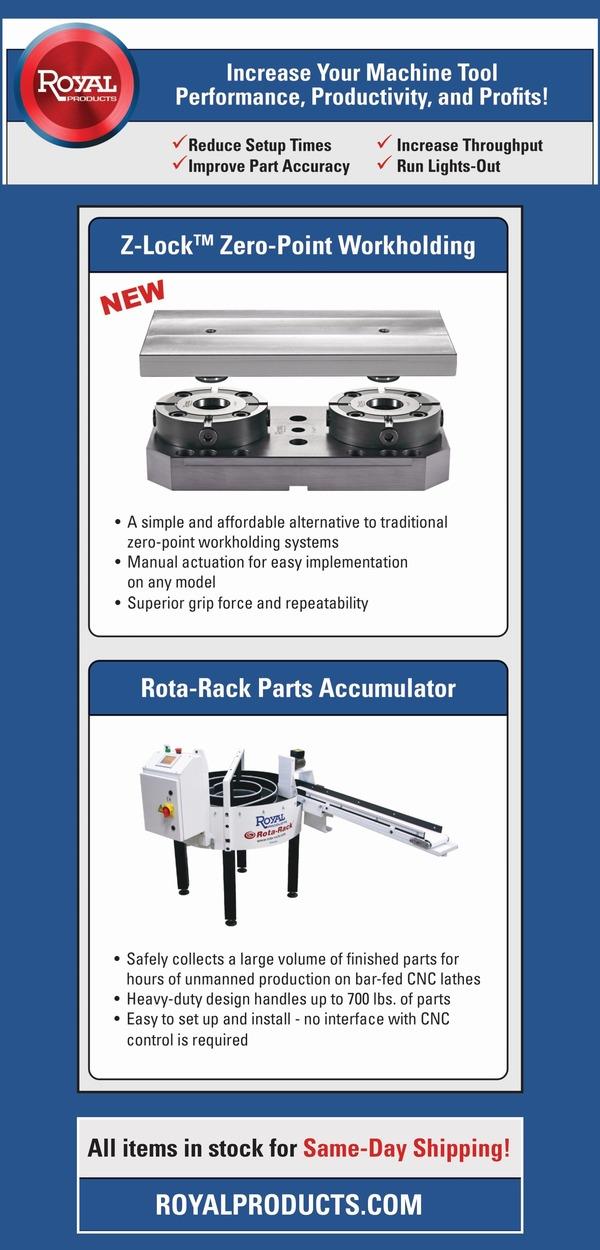
Expanded Welding Information Management Software
February 1, 2016
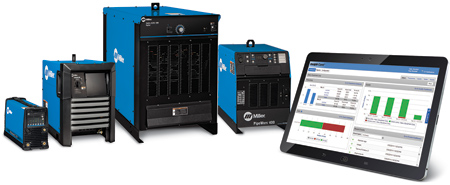
As part of its Welding Intelligence solutions, Miller Electric Mfg. Co. has expanded its welding information management software to multiple power sources, including the Continuum advanced MIG welder, Dynasty 280 DX TIG welder, PipeWorx 400 welding system and SubArc Digital series.
As part of its Welding Intelligence solutions, Miller Electric Mfg. Co. has expanded its welding information management software to multiple power sources, including the Continuum advanced MIG welder, Dynasty 280 DX TIG welder, PipeWorx 400 welding system and SubArc Digital series.
Miller Welding Intelligence is a category of active and passive software that transforms data into meaningful insights and actionable information to drive continuous improvements in the welding operation. The focus of these solutions is to help increase productivity, improve quality and manage costs. Additional benefits include:
- Complete fleet coverage: Solutions available for new and existing Miller equipment, as well as non-Miller machines
- Complete application coverage: MIG, TIG, pipe and submerged arc machines now available with Welding Intelligence solutions
- Scalable solutions: The choice of simple passive systems or more sophisticated active systems.
For example, Insight Core monitors, collects and rapidly transmits electronic weld data to any Web-connected device, whereas Insight Centerpoint is a solution that provides real-time operator feedback and process control. ARCAgent, from the recent IMPACT Engineering acquisition, allows customers with mixed power source fleets to implement Welding Intelligence solutions on non-Miller machines.
Insight Centerpoint has been upgraded to Centerpoint 9.0 software. This software offers feature improvements, such as a Library Manager tool that better organizes weldment drawings and photos, and a more visual dashboard layout with speedometer-style performance indicators. Insight Centerpoint 9.0 also offers a persistent operating system that automatically picks up in sequence where the operator left off, following a power cycle. Other improvements include:
- Smart Part Tracking: This feature calculates the deposition required for the weld when the welding operator enters a weld symbol and fillet size, helping ensure consistent weld quality
- Standard AWS weld symbols: These provide annotation of the weldment to help save production and planning time. Previous versions required these to be created individually by the customer
- Codes and Standards module: Captures required information relating actual welding parameters to a specific welding operator, contract, joint and weld pass to ensure productivity and quality requirements are met.
For more information contact:
Miller Electric Mfg. Co.
P.O. Box 100
Lithonia, GA 30058
800-426-4553
info@millerwelds.com
www.millerwelds.com
< back