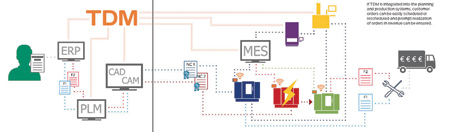
If TDM is integrated into the planning and production systems, customer orders can be easily scheduled or rescheduled and prompt realization of orders in revenue can be ensured.
The focus of Industry 4.0 is to optimize manufacturing through an overall approach, a logical development in recent years. It is nothing more than the automation and networking of production systems. Such systems are able to provide information in the form of a great deal of data. The challenge is to prepare and use it so that it brings economic advantages.
"Tool Data Management plays a central role in Industry 4.0 connecting technical and business departments," said Thomas Mücke, TDM Systems Senior Consultant. "In many companies today, there are two fundamental structures side by side. A technical process, realized through Product Data Management (PDM) or Product Lifecycle Management (PLM) systems, and a business management process, controlled by Enterprise Resource Planning (ERP) systems."
Tool Data Management is networked with PLM/CAM systems or BDE/MDE/MES systems, but also to the orders from the ERP system. Real-time information from the machine helps to optimize the processes of both areas even more and to reduce product and manufacturing costs.
"It has long been known that about 70 percent of a product's cost is already defined in the design. An example: changing the diameter of a hole from 10 to 10.2 millimeters requires only a mouse click. However, if the tool for the new diameter is missing from the workshop, this causes problems that interfere with the process," said a company spokesperson.
By accessing appropriate tool data, the designer can already see in his or her CAD system whether the production of the desired hole is possible in terms of efficiency.
"Prerequisites are tool data with tool geometry and technical information about cutting data, production processes, as well as machine information," added Mücke. "With this information, the designer can perform a preliminary calculation to evaluate the feasibility and the cost of the machining operations."
A seamless flow of data from the machine is a prerequisite for process optimization. A significant amount of information in the form of cutting data needs to be organized, controlled and stored to facilitate the remaining tool life, machine utilization, or feeds and speeds of tools. "TDM can collect and store this data easily and provide comprehensive benefits in various areas," said the spokesperson. The remaining tool life can be utilized for transparent crib planning.
Tools are inventory-optimized and promptly ordered, which helps reduce storage costs and capital commitment. Real-time information on machine utilization and condition of the tools allows a flexible and prudent scheduling of production orders on the machine. The condition and machine and crib location of the tools are also taken into account. Orders can be rescheduled with short notice and produced with alternative tools; set-up cost and times are reduced.
The lead-time of a customer order should be as short as possible. Bottlenecks can cancel out most any other achievement. Countermeasures can be taken through alternative operations in the work plan or in the production order.
The necessary NC programs require automated CAM programming. "Automatic feature recognition in the CAM process with subsequent virtual simulation with data from TDM ensure the pace and consistent quality. The optimal scheduling of production orders on the appropriate machines and tools requires networked thinking. For this purpose, Advanced Planning Scheduling (APS) and Manufacturing Execution System (MES) systems must be integrated," said the spokesperson.
A few typical examples show how this works in practice. During maintenance, the machine sends information to TDM, which is processed so that the downtime of the machine can be planned for and minimized. If an operation is moved to another machine, TDM can immediately release tools again for other jobs and thus reduce the capital lockup. With real cutting data from the machine, CAM systems can reduce the machining times and help the operation. "Such information will be available in the future on all devices in real time. Since the data is always assigned to the production order, it can be tracked. Networking promises increases in production because the machines will ultimately produce more," said the spokesperson.
For more information contact:
TDM Systems
1665 Penny Lane
Schaumburg, IL 60173
847-605-1269
info@tdmsystems.com
www.tdmsystems.com