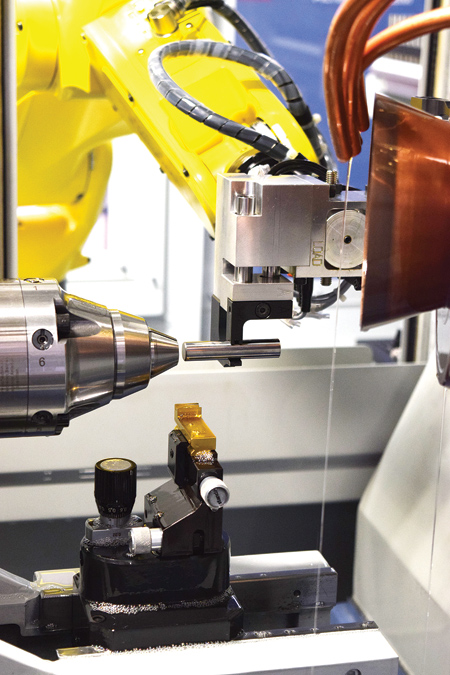
Autoloading a carbide blank into the ANCA collet
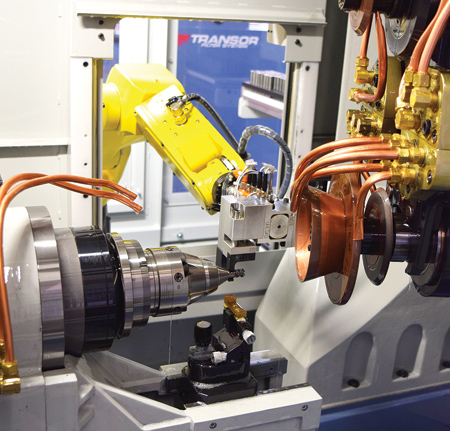
End mill production is fully automated at Supermill
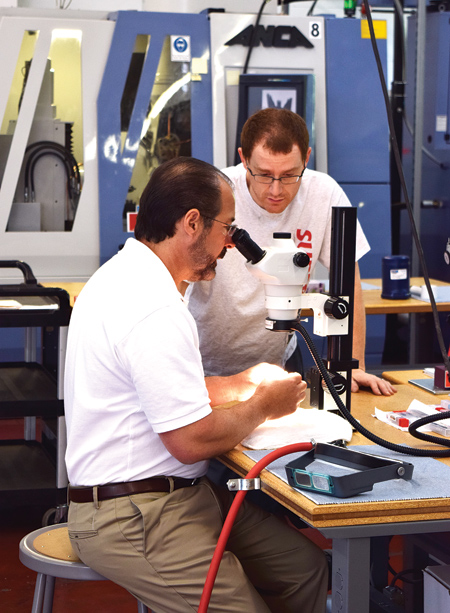
Quality is in the details. Tom Hale examines a finished tool.
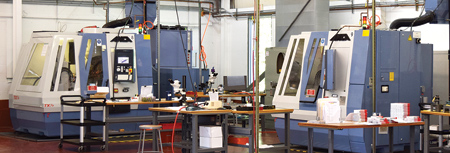
Supermill production floor
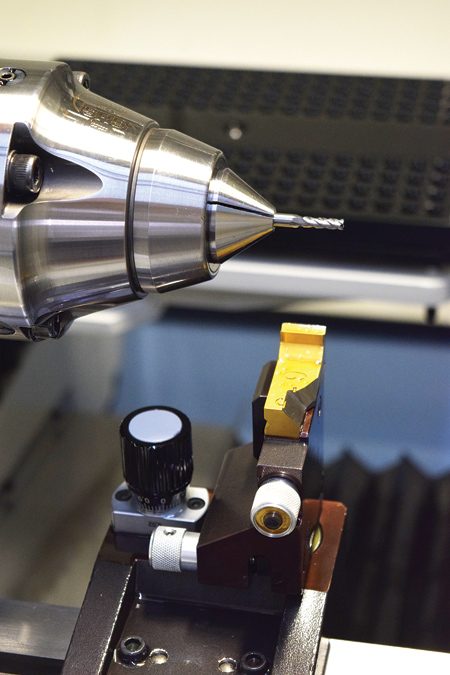
Supermill tool in collet
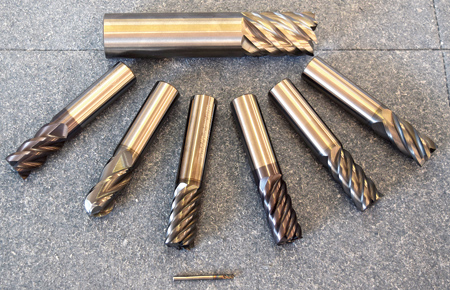
Supermills
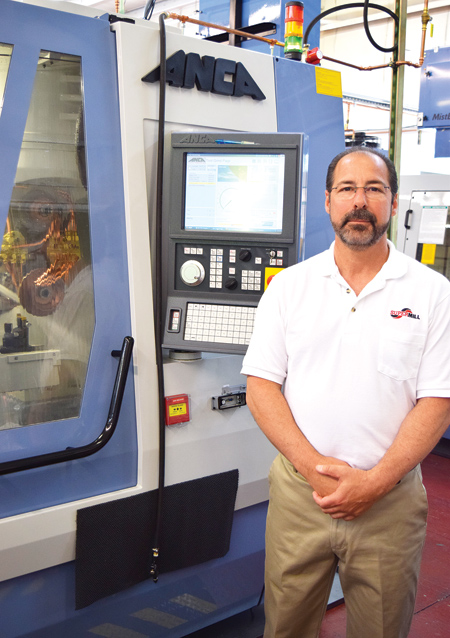
Thomas J. Hale, President, Supermill, with an ANCA grinder
Supermill (Berlin, CT) had made a good name for itself regrinding cutting tools end mills mainly used by area shops, large and small. President Thomas J. Hale learned the cutter grinding trade in the aerospace industry in Connecticut, and offered his regrinding tool skills for the aerospace and defense shops in the area. Business was good. But Hale was looking to do more to serve the machining industries.
So, from the old Cincinnati tool grinders he started with in 2001, Hale moved into CNC tool grinders. He purchased two ANCA RGXs, the first new CNC tool and cutter grinders it acquired. The machines are still in top condition mechanically. He has added a number of ANCA machines since then, always investing in available automation to reduce handling and improve the shop's flexibility to produce many different tool designs.
As can sometimes happen when a curious mind is at work, the company began to think how it could design tools differently for better performance. By 2004, it decided it wanted its own brand of high-performance carbide cutting tools that would be available across the nation.
"In order to survive and prosper, we needed our own brand, and we called it Supermill," Hale said. "We had to back that up with a product. We cannot be as large as the big names in the industry, but we knew that we could be a good as them. The idea was that when a job was being laid out, we wanted to be in the room with the tool user.
Managing High Volume Production, Tool Variety
"Today, we have high volume numbers for production, but they are on high-end tools; we do not make a standard tool," said Hale. "Every tool here has a special design to serve a specific purpose. Our brand is more material-specific than most. We are designing for material to be cut. Period." The Supermill catalog has more than 21 different style tools–a very broad line specifically designed to cut a variety of materials.
Over the years, tool production volumes have increased, and Supermill has kept up with tool development and production with a range of ANCA CNC tool grinding machines. Key goals at Supermill are to produce high volumes and a wide variety of specially designed tools while minimizing idle time, including achieving 24/7 operation.
To address these goals, each machine includes automation that reduces handling and eliminates idle time. Wheel exchangers permit the machines to produce a range of different tool designs without changeover. Robot loading of the carbide blanks and removal of the finished tools eliminates handling.
To get into tool production, the company invested in its first two ANCA TX7 production tool grinders to make 1.5" to 1/8" tools. In addition, Supermill installed four smaller MX5s, each with a 2-position wheel exchanger, and a versatile MX7 with a 6-position wheel changer that allows the machines to run unattended, producing a variety of tool designs. "Up to 18 wheels are on the MX5s, giving us the flexibility to make any tool at any time," Hale said.
"In 2011, we bought a third ANCA TX7 machine with no place to put it, so we started taking over space in the building from the other tenant," Hale said. "Shortly after that, more machines were coming in the door, and the other tenant left the building to Supermill and its ANCAs. Today, we are running two to three shifts generating our own design tools that are highly valued by users in the aerospace, defense and medical industries."
The TX7s are production tool and cutter grinders, and are equipped with a robot pallet loader and an autoloader that takes blanks from the pallet and loads them into the machine collet. This means the machines can be set up to run many hours unattended while grinding a variety of tools from the Supermill catalog.
In all, eight of the machines at Supermill have autoloaders. "It is about production," Hale said. "When we go home at night we can still be making tools."
ANCA Software Advantage
"One of the biggest advantages to me," Hale said, "is the iGrind tool grinding software version 32 with the on-board simulator. We can design the tool in the office and if any changes are needed in the tool, we can make the change out on the shop floor at the machine. This allows us a lot of flexibility and offers us time savings during tool development. The operator can see what is going on with the tool. This gives us the ability to make just about anything."
"The ANCA's software is so easy to use and we use it to build any feature into the tools we design," Hale continued. "We choose the grinding operation, and then we need only change numbers in the grinding process to alter the tool geometry. This allows us the versatility to use the grinding wheels in many different ways.
"Basically we can grind my way, which is a big advantage to us in designing and making efficient, effective tooling for our customers. Some machine manufacturers want operators to use a certain wheel a certain way. The ANCA lets us use a wheel the way we want to use it."
A new end mill wizard within iGrind helps Supermill program ball nose, corner radius, square and chamfered end mills. "This lets us automatically generate production-ready tools directly on the machine," Hale reported. "Since it is completely customizable, we can set our own wizard behavior to suit our tools and production methods. Plus, we can create multiple customization sets to suit our different product ranges. Automatic wheel selection and recommendation is a helpful element in the software, simplifying end mill programming and reducing operator training time."
Another helpful feature of iGrind is the display of a 3-D model of the tool on the machine control interface with each grinding operation color-coded. The operator can program the tool and verify the geometry on the machine, and tool models update within seconds of changing any design parameter. Easy-to-use touchscreen controls allow full manipulation of the model on the machine.
At Supermill, cycle time does not come before the quality of the tool. "Sometimes you have to slow things down to make a better tool," Hale said. "We can go from 5 minutes on a smaller tool to up to an hour on a larger tool. We are not going to rush a tool through. We want quality.
"We are always looking for productivity and tool life for our customers. The result is we save them machining time. Our tools are designed to run faster and last longer. Some tools are not even products; they are just being evaluated. In a sense, we give the tools away."
Hale designs tools working in cooperation with his customers. "When we have a design we agree on, we run the tool and apply the tool," he said. Once we have completed the design, the customer is satisfied that the tool will work as required. Customers love being part of the process of tool design. When the tool is perfected, we are allowed to produce it.
"When a product is done, though, it is not done forever. We keep track of new developments in grades of carbide and coatings."
Capital Spending Strategy
When it comes to buying machines, dollars are not the issue for Hale. The issue is capability. "We are competing with people from all over the world," he said. "Machines, workholding, inspection equipment, wheels, etc. If you do not keep up with the latest technology available, you fade away. You end up doing less and less. But the companies that invest in new equipment produce for less. We pick up one or two machines a year to keep up with demand for various tool diameters. You have to have new equipment."
For more information contact:
Supermill
59 Deming Rd.
Berlin, CT 06037
860-828-9703
www.supermill.com
ANCA, Inc.,
31129 Century Drive,
Wixom, MI, 48393
248-926-4466
www.anca.com