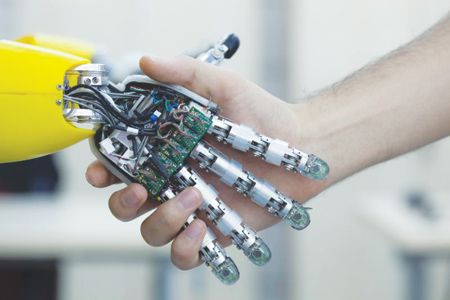

Pilz helps implement and automate safe man-robot applications, with a product and service portfolio that is tailored to the individual robot system.
Today's robots are going where no robot has gone before. In each case, safety aspects must always be considered on an individual basis and the appropriate safety solution implemented for each application. Safe sensor technology has a key role to play: a modular approach to sensors is required in order to satisfy all applications with regard to safety.
Many of today's applications that use robots have a very high level of automation. Human intervention into the production process is always undesirable. To guarantee safety and availability in such applications, mechanical guards enclose plant and machinery. Generally speaking, the robot cell only needs to be accessed for service purposes. Safety gates are suitable for this type of access, although they must be safeguarded using safety gate sensors. If a safety gate is opened, the sensor detects this and generates a shutdown signal for the safe machine control system.
Basic Protection and More
A variety of actuation principles and designs are used, depending on the requirement, installation and application-based boundary conditions.
Non-contact, safe magnetic sensors represent a very economical solution for concealed installation, while safe RFID-based sensors such as the safety switch PSENcode from Pilz enable maximum freedom during assembly and guarantee the greatest possible manipulation protection.
If safeguards need to be positioned close to a hazardous movement, when space is at a premium for example, then there is a risk from a hazardous overrun. In this case, it is absolutely essential to use a safeguard-locking device. Mechanical guard locking devices with spring interlock, such as the PSENmech, or integrated safety gate systems such as PSENsgate and PSENslock can perform these tasks.
There is a wide range of unit types for all these technical sensor principles, so that almost every conceivable monitoring scenario can be implemented. For example, PSENcode coded safety switches are used in areas of a robot-assisted car body plant; these can monitor up to three positions with just one sensor. Application areas in this case are the interfaces between man and robot, where manual access is also required to load and unload metal parts from robot cells enclosed by guards, for example.
With robot applications that require human control, insertion of parts or reworking, for example, electro-sensitive protective equipment such as safety light curtains are often used to provide access protection. It may also be necessary to fit protection against encroachment behind the protected area in the form of vertically installed safety light curtains or a safety laser scanner. In many cases safety mats are the preferred choice, if the optical systems experience availability problems due to process-related boundary conditions such as dust, smoke, mist or steam, for example.
When Man and Robot are Expected to Collaborate
Man-robot collaboration is a whole new field. In an ideal scenario, man and robot will share the same workspace. These new application fields create synergies and therefore productivity benefits by combining the strengths and benefits of the machine, such as reliability, durability and repetition accuracy, with human strengths such as dexterity and flexibility. With this type of human-robot collaboration, the workspaces of the human and robot overlap in both space and time. Human-robot collaborations, particularly in the service robot sector, are a good example - robots with low payloads are generally used here, for pick and place applications for example.
Every effort is made to implement the safety of the application through safety components and safety functions in or on the robot. For example, safe motion functions in the robot are combined with close-range sensors, with integrated torque monitoring in the robot or with tactile sensor technology around the robot. With this type of robot application, the movements are generally much slower than in fully automated applications. Today, such safety philosophies are implemented in the service robot sector in conjunction with man-robot collaborations; applications can also be implemented when other safety requirements are considered.
Hazard-Free Zone - Dynamic Safeguarding
When human-robot collaborations are used with robots with larger payloads, the safety concepts detailed above are pushed to their limits - other concepts are needed. A more clearly graduated view of events is required. For example, it must be possible to distinguish whether a person is within the potential action radius of a hazardous movement (warning zone) or has already accessed a zone with an increased safety requirement (detection zone). Ideally it must be possible to adjust these zones dynamically and to track the safely monitored movements of the machine or robot, for example. In this environment it is possible to implement human-robot collaborations in which static safeguards are pushed to their limits.
New camera-based processes, such as those provided by the 3-D camera system SafetyEYE for safe zone monitoring, are capable of monitoring protected fields and detection zones safely in several dimensions. Due to their 3-D operating principle, such sensor systems open up new possibilities for the design of applications. Further, detection zone arrangements can be re-adjusted at each step of the process.
Further developments in this field are dependent on the requirements of future applications: by combining a safe robot with a safe 3-D camera system with better communication, a variety of strictly separate process steps can be merged and optimized. The safe robot knows its safe position, its safe speed and its safe direction of movement; the safe camera system knows the position of objects (people) around the robot's operating range. Instead of a rigid shutdown, the whole system can react much more flexibly, avoid unnecessary downtimes and, in turn, increase plant productivity.
Modular Technologies for Safe Robots
The proportion of man-robot collaborations will definitely rise, but growth will depend heavily on innovations in the sensor technology and robotics environment. Even in the future there will probably not be one safe robot or one safe sensor technology to cover all potential application cases with regard to safety. That is why a modular system is needed that comprises a variety of technologies, from which users can choose the appropriate tool.
Robotics Services from Pilz
Each robot application requires a separate safety-related assessment. Ultimately a safe HRC application is the result of several factors: interplay between normative framework conditions and a complex risk analysis on this basis, selection of a robot with the relevant safety functions, selection of appropriate, additional safety components and finally, validation through a systems integrator. Pilz, the complete safe automation supplier, provides support with a services portfolio that is tailored to the individual life phases of a robot system: from process analysis to risk assessment and CE marking. A special training package on robot safety completes the range of services.
For more information contact:
Pilz Automation Safety L.P.
7150 Commerce Blvd.
Canton, MI 48187
734-354-0272
info@pilzusa.com
www.pilz.us