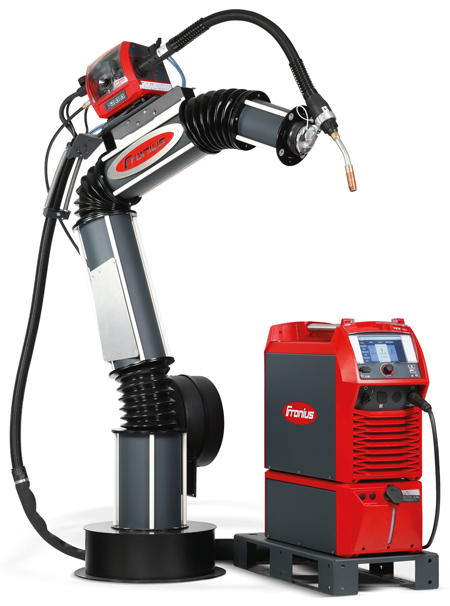
The new robotic welding solution, TPS/i Robotics, features enhanced welding speed, system availability and reproducibility.
Fronius has announced the TPS/i Robotics power source, which is designed to meet the demands of robot-assisted welding. "Due to its interconnected and fully synchronized system components, it enables robotic welding to be performed faster and with a higher degree of reproducibility," said a company spokesperson.
"Fronius engineers have drawn on the power source's consistently implemented digital system architecture and new communication technology features to cover and address all the major influencing factors crucial to the welding process with high definition and reaction speed. The result is an exceptionally stable arc and optimum welding results," said the spokesperson.
The modified dip transfer arc (LSC – Low Spatter Control) and the modified pulsed arc (PMC – Pulse Multi Control) are designed to give the welder a higher level of control over the arc. The user is also supported by new stabilizers: while the penetration stabilizer ensures that the penetration remains constant – even if stick out fluctuations occur – by adjusting the highly dynamic wire feeder, the arc length stabilizer keeps the arc at an optimum length when the arc geometry (e.g. due to a change in the weld seam profile) or weld pool temperature changes.
"As a result, TPS/i Robotics not only makes the welding process considerably quicker than ever before, but also enhances the weld seam quality. One of the visible improvements is the minimal amount of spatter produced," said the spokesperson.
Another benefit of the power source's consistent digitalization is the continuous collection of information on the current status of the power source and on every weld seam, which is made available to the user. This detailed data can be used to monitor, analyze and document the welding process. Using the central server unit (WeldCube), the data gathered from several power sources via their Ethernet interfaces can be combined and managed from a company-wide perspective.
"Fronius is also forging new paths in the area of communication between the welding system and robot control. Like all other process control components, the TPS/i system's new robot interfaces are incorporated into the system bus architecture and are therefore able to provide data relevant to the robot control in real time," said the spokesperson.
A new Interface Designer allows the robot interface to be programmed quickly and conveniently offline using a graphical user interface. Users can configure and adapt the interface to their own individual requirements at any time. In addition, Fronius provides pre-prepared interfaces to the control systems of robot manufacturers.
For more information contact:
Stephanie Gibson
Fronius USA LLC
6797 Fronius Drive
Portage, IN 46368
219-734-5701 / 877-376-6487
gibson.stephanie@fronius.com
www.fronius.com