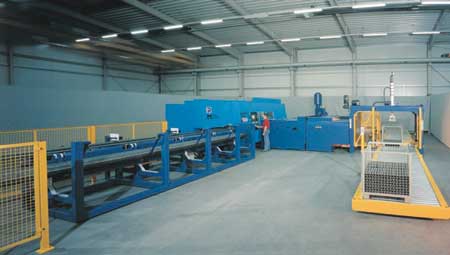
Rattunde ACS + CFMtwin machine for simultaneous dual tube processing; can produce up to 5,000 parts per hour.
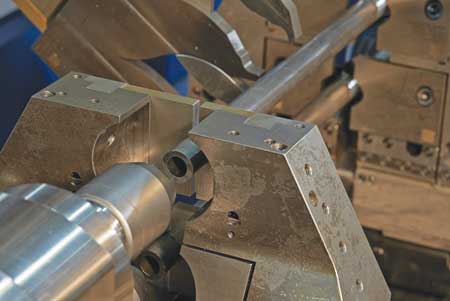
Close-up of twin cutting head; machine cuts two workpieces simultaneously.
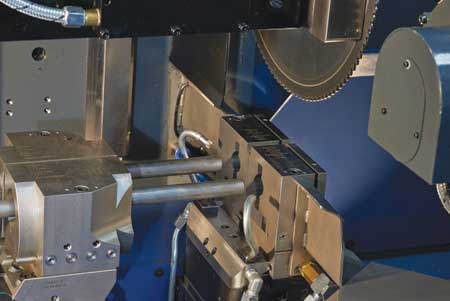
Each end of the two workpieces is simultaneously chamfered before automated transfer to the cleaning and final packaging stations.
Rattunde Corporation, a German-based manufacturer of finished length tube and solid bar production, announced the introduction of the ACS + CFMtwin machine, the newest member in the company's family of tube production systems. Equipped with a specially-designed twin machining head that fits onto the standard head, this new machine can cut two tube or bar sections simultaneously, then machines both ends of both workpieces, also simultaneously. This new Rattunde machine can produce up to 5,000 finished pieces per hour. The option also exists for single tube or bar production on the same machine.
The ACS + CFMtwin machine, when in twin mode, can process two workpieces of 10 mm to 41.5 mm O.D. each into finished lengths from 10 mm to 1,500 mm. Example: 21 mm O.D. x 3.5 mm wall x 45 mm length cut from a 6.5 meter mill length of stock material, based on carbon steel. When the twin head is removed, the standard machining head can process a single workpiece up to 105 mm O.D.
In addition to the twin workpiece processing, this new Rattunde machine offers the OEM or production house all the capabilities found on Rattunde's ACS family of tube and bar production systems, including secondary brush deburring, end machining (chamfering and facing), inspection, washing, drying and robotic packaging. The entire machine and all auxiliary workstations are motion-controlled by CNC from a single operator station for maximum efficiency. The ACS + CFMtwin is built on the same platform as the existing and popular Rattunde ACS + CFM and ACS + CFMcurve systems.
Other standard features on this new Rattunde machine include data management on all workpiece parameters (approx. 10,000 workpieces), data logging of every part produced for full part traceability, material lead and end edge detection for minimized crop cut and tag end. All operating limits are set from the control panel, with continuous tool break monitoring for the saw blade and all cutting tools.
Even when processing in twin mode, the setup time for a new job can be under 15 minutes, according to Rattunde engineering.
Alec Banish, Director of Business Development at the company, states, "With the standard machining head still in place on the machine, the ACS + CFMtwin can be a highly flexible, adaptable production system for many types of manufacturing operations."
Because the machine offers essentially double the production in the same machine footprint, up to 40% energy savings have been documented on a 25 mm O.D. x 3 mm wall x 42 mm long piece from a stock length of 6 meters in a typical batch count of 45,000.
For more information contact:
Rattunde Corporation
4980 Kendrick Street SE
Grand Rapids, MI 49512
616-940-3340
company@rattunde-corp.com
www.rattunde-corp.com