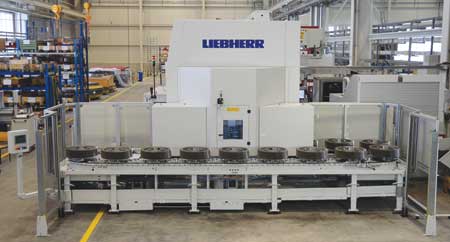
Liebherr's heavy-duty line to serial manufacture work pieces weighing up to 400 kg.
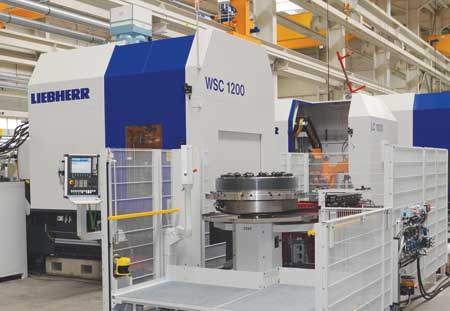
Liebherr's WSC 1200 shaper with pallet changer.
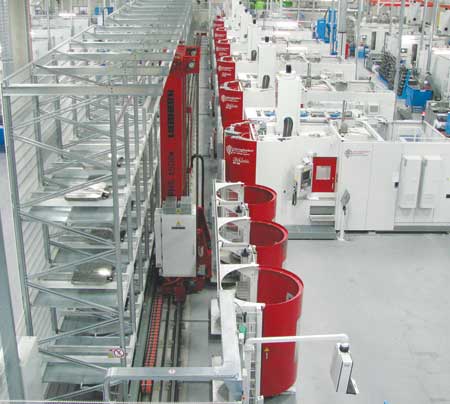
Automation solution involving the PHS 1500 pallet handling system at a major German vehicle manufacturer.
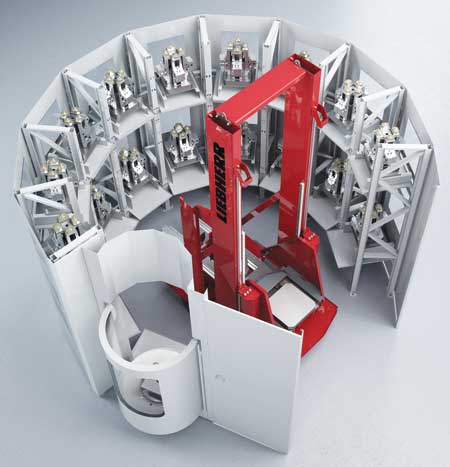
The new rotation loading system for high-efficiency manufacturing.
Batch sizes have a significant influence on what is required of any automation solution. The main difference is between high-volume production and contract manufacturing producing batch sizes of one or low-volume batches.
As far as serial manufacturing is concerned - a machine needs to be loaded and unloaded as quickly as possible and the components need to be transported to the next processing operation. There should also be a sufficient buffer for set-up operations to prevent downtime and to balance and minimize any line cycle time mismatches. In such production scenarios a combination of gantry and storage systems or palletizing cells are frequently employed.
Where a batch size of one and low-volume batches of work pieces with small to medium diameters are involved, machines and fixtures have to be adjusted frequently. Liebherr provides a range of different solutions for individually adjustable work piece jigs.
"In respect to larger gears up to 2,500 mm in diameter, the key is to decouple set-up times from machining times and thereby improve capacity utilization. These days up to 50 percent of machining time in this segment are lost due to set-up activities, since the work pieces are usually set up directly on the machines. During these downtimes the machine cannot produce anything. Automation systems in combination with suitable part racks facilitate preparation away from the machine, meaning any pre-set-up component can be processed immediately. This approach is still comparatively new in gear technology - but the potential is considerable," said Stefan Jehle, Sales Director Automation Systems at Liebherr-Verzahntechnik GmbH.
"The machine's utilization rate can be increased to 90 percent. One such solution in achieving this is that preliminary setup can also be applied to gears produced on lathes and shaping machines in down stream operations. There are special jigs that facilitate both machining processes using the same mounting."
Implementation in practice
At a U.S. manufacturer lathes and shaping machines were combined in one production line and automated, in order to be able to manufacture frequently changing components in small batches. Automation and set-up stations away from the machine can be expected to increase the utilization rate from 55 up to 90 percent compared with a machine that is loaded manually, according to Liebherr.
Customized planning using standardized modules
Given the specifics of each case, such projects often involve a considerable amount of engineering effort. "Liebherr and its experienced project teams are also ready to meet whatever challenges that they may be confronted with on any given application," said a company spokesperson.
Essentially all solutions, whether standard or customized, are based on a modular toolkit of automation components. That means that several basic process reliable solutions, which have been used in practice over the years, already exist.
Simplified handling
Automation systems must accomplish different amounts of tasks, depending on how a particular manufacturer is structured. In addition to reducing workload of staff, the objective is also to make the systems as easy as possible to operate. Customers with high staff turnover require quick and simple initial staff training. Depending on requirements, the user-interface can be designed to allow less qualified staff to operate the automation systems.
An all-inclusive approach is the key.
"Our product range enables us to consider all the main criteria when designing an automated production line: batch sizes, jig designs, component diameters and weights," said Jehle. "It is key to keep the user's entire process in mind. Actual design is always client-specific."
For more information contact:
Kevin Heise, Vice President of Sales
Liebherr Automation Systems Co.
1465 Woodland Drive
Saline, MI 48176-1259
734-429-7225
Kevin.Heise@liebherr.com
www.liebherr.us