
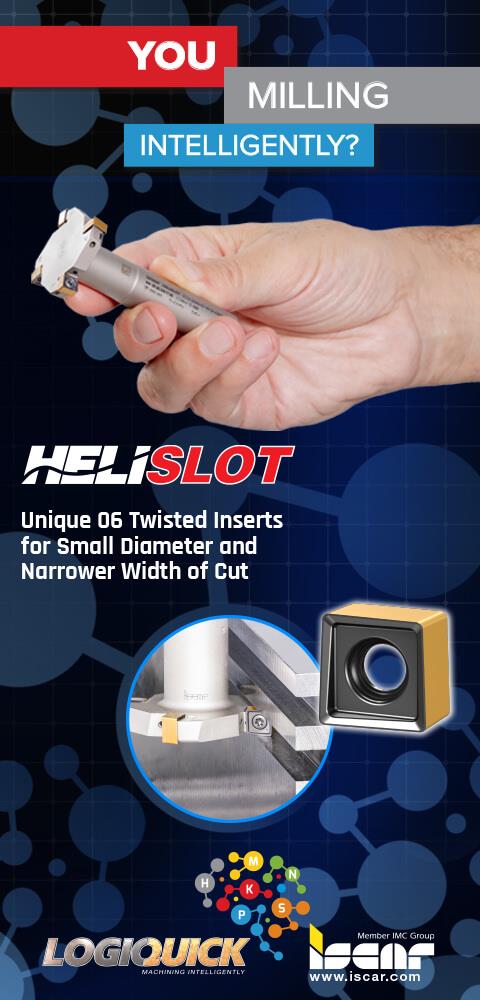
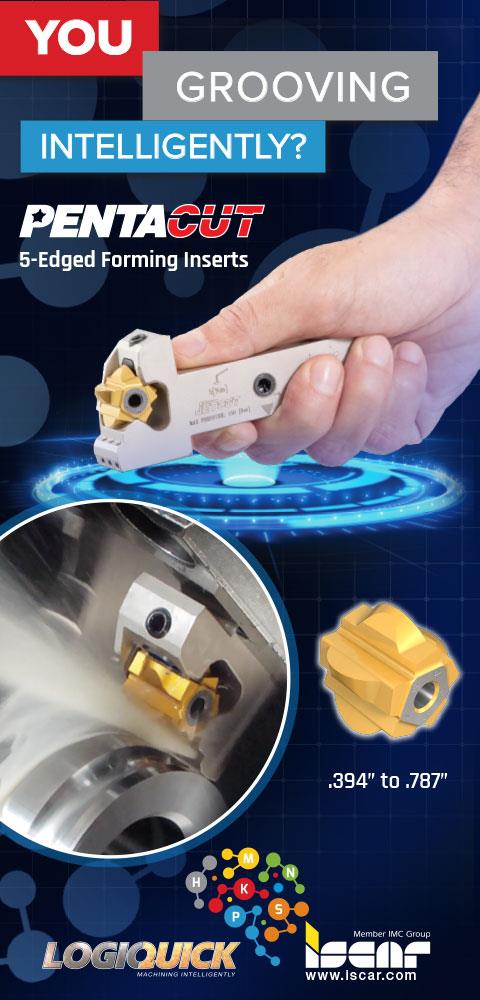
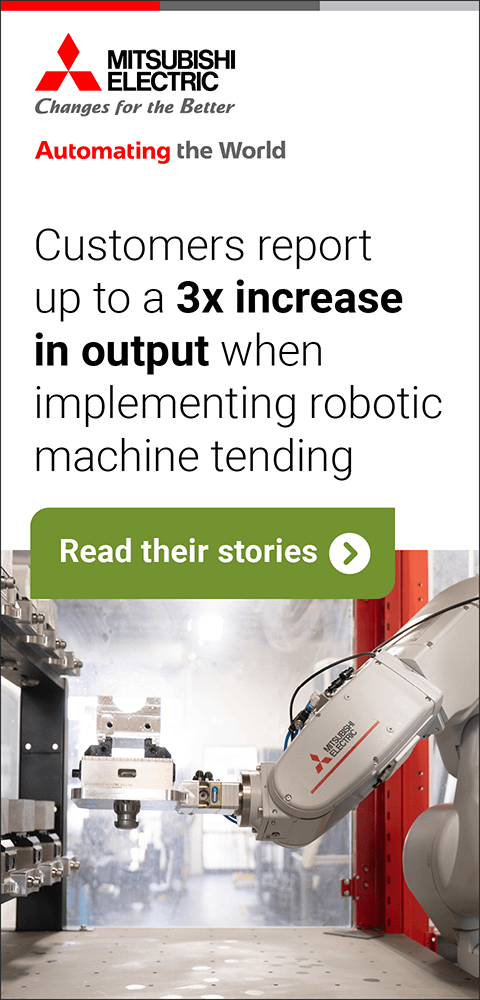
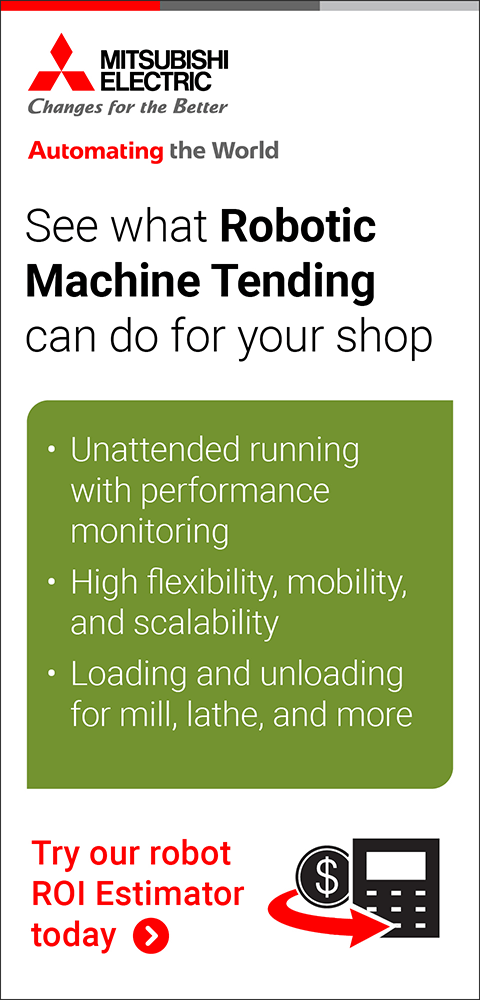
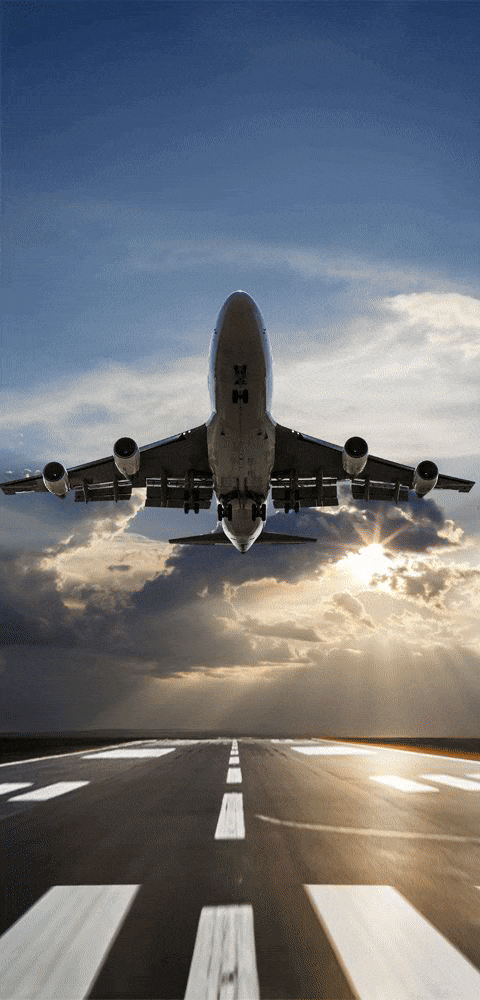
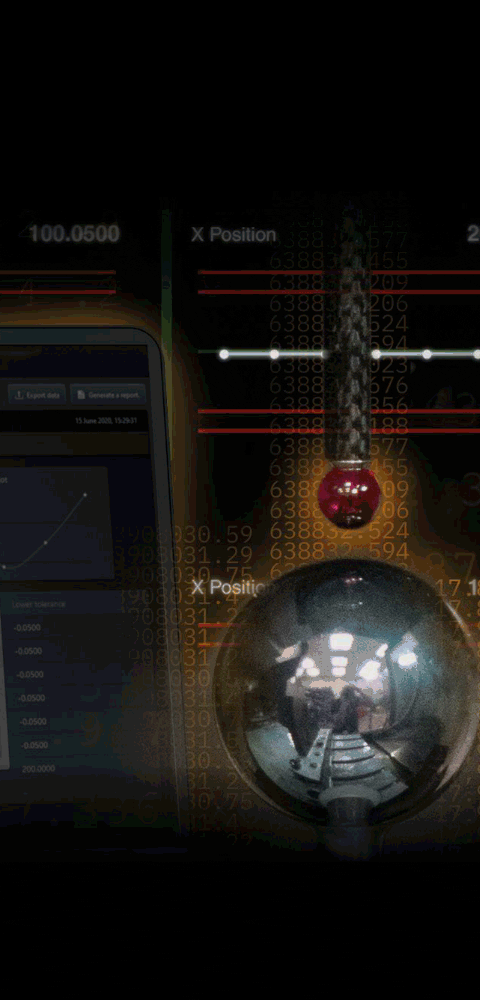
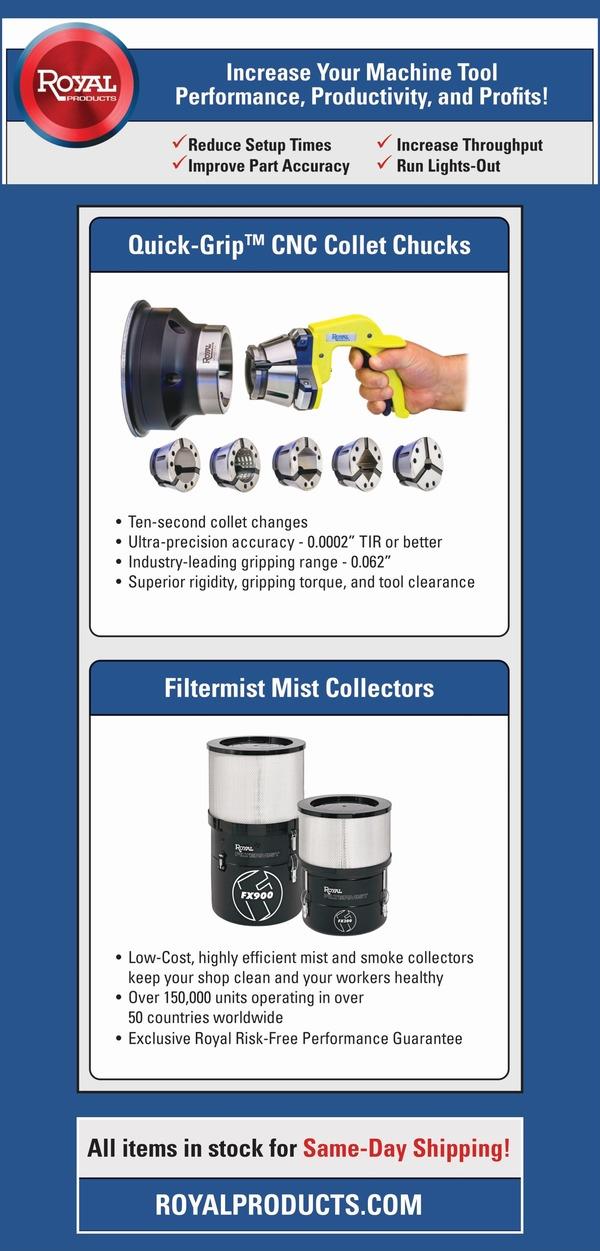
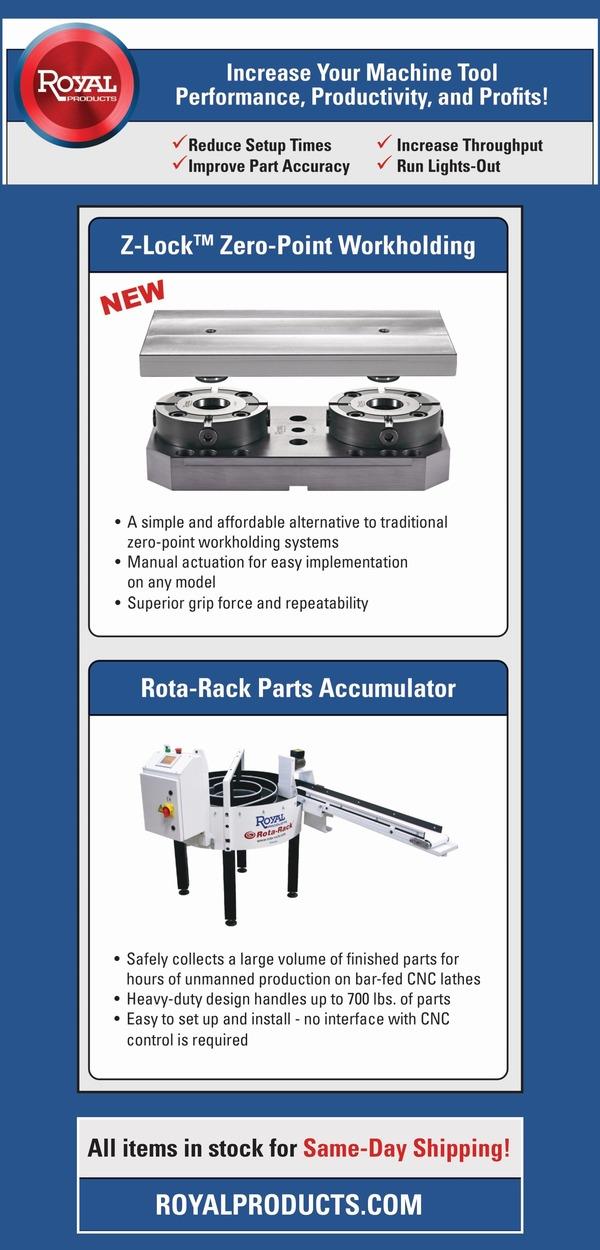

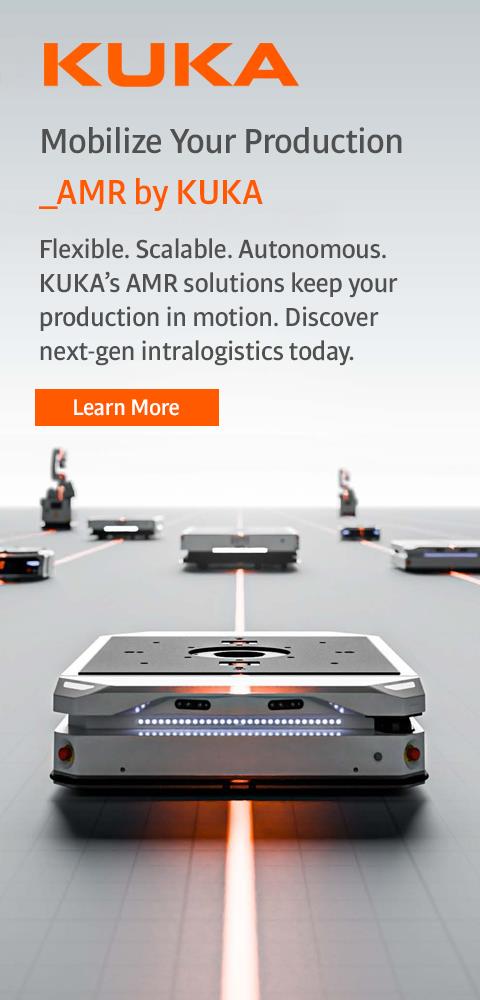
Mid-Size UAM Machine
August 1, 2013
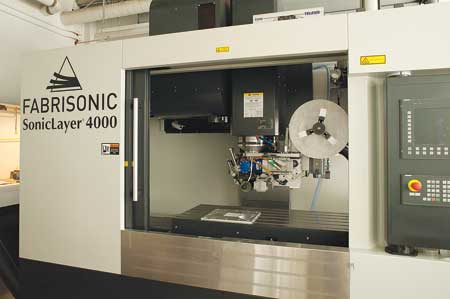
The SonicLayer 4000
Fabrisonic, LLC has introduced the newest addition to its line of ultrasonic additive manufacturing (UAM) machines, the SonicLayer 4000. This mid-size, fully automated 3D printing machine can be customized for specific settings and applications. According to the company, the Ohio State University College of Engineering has been the first to adopt the SonicLayer 4000 for use in its research on embedded smart materials.
The SonicLayer 4000 has a 3-axis CNC mill with bed dimensions of 40" x 24" and a 25 HP 8,000 RPM spindle for machining metal parts. It utilizes Fabrisonic's patented 9 kW UAM welding head to additively manufacture solid metal parts. To enhance productivity, every machine comes with a copy of Fabrisonic's custom-made G-code CAM software, which allows for true CAD-to-part automation. When CAD geometry is imported into the SonicCAM, the software generates the tool path for both welding and machining. The automatically generated G-code is then moved to the machine for production.
Specifications of the SonicLayer 4000:
- Footprint: X direction 12'; Y direction 12'and height 113"
- Axis working travel: powered X-axis ~40"; powered Y-axis: 24"; powered Z-axis 24"
- Linear accuracy: positioning ±0.0002"; repeatability 0.0001"
- Table size: 44" x 24" length x width
- Welding machine - U.S. power: 9 kW; welding force 2,500 lbs; welding speed (max) 200 IPM.
"Ultrasonic additive manufacturing is changing the way that we produce parts," said Fabrisonic CEO Mark Norfolk. "By combining process capabilities, UAM can create deep slots, hollow, latticed of honeycombed internal structures, and other complex geometries that just cannot be made using conventional subtractive processes. This technology opens up a whole new frontier for manufacturers."
For more information contact:
Mark Norfolk
Fabrisonic, LLC
614-688-5223
mnorfolk@fabrisonic.com
www.fabrisonic.com
< back