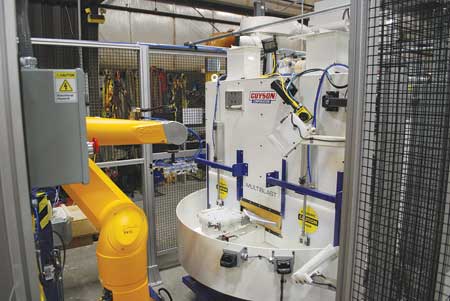
Guyson Corporation has integrated a robotically automated bead blast finishing cell that operates unmanned to process fragile electronic components for the automotive industry.
Guyson Corporation has integrated an unmanned surface finishing work cell that combines robotic component handling with automated bead blasting and 100% optical inspection. The RX-800-RB blast system is designed for rapid processing of fragile automotive electronic parts that require a precise degree of impact treatment on one side.
Due to the accuracy and repeatability needed to perform the part handling routine and the brand preference of the customer, the machine tending robot selected for this application was a 6-axis Staubli TX-90XL with a compact CS8C controller. The robotic arm is fitted with a vacuum-style end effector designed to pick up, flip, re-orient and place the flat components before and after blasting in the multiple gun bead blast machine. As the robotic loader picks parts from a stack at the load position on the in-feed conveyor, proximity sensors located on the vacuum gripper signal the robot when it has a part.
The robotic blast system manufacturer designed and fabricated custom component holding fixtures for the four-station indexing table blast machine, as well as automation accessories such as a fixture for the inspection station, a cradle for alignment of parts and a flipper to invert the product as it is placed on the exit conveyor of the finishing cell going to the next production process.
Inside the bonded rubber lined blast chamber of the RX-800, five suction-blast guns are mounted on a ballscrew ballnut linear actuator in a tight cluster at the correct angles and distances for uniform coverage of the product's target surface. During the blast cycle, the blast guns move at controlled and adjustable speed for the programmed stroke distance, then the table indexes to deliver the part to a separate station where automatic air wash blow-off removes blast media and dust before being returned to the load/unload station at the front of the blast machine.
The robotic automation system includes an optical inspection station. Prior to blasting, each component is placed in a dedicated fixture for imaging to detect cracked or broken parts and to confirm that the product is properly oriented with the correct side facing the camera. If an inverted part is found, the robotic machine tender will automatically remove and turn the product over for re-inspection and then proceed to load the passed component in the blast cabinet.
The blast system includes a number of electronic sensors that monitor critical conditions. For instance, blast media is automatically added to the machine when a low media level is detected in the hopper that feeds the blast guns. A separate low media level sensor in the adder supply hopper triggers a fault indication beacon and audible alarm to summon an attendant. Likewise, a full dust collector waste drum will result in a fault indication.
Prospective users of automated or robotic blasting equipment are invited to submit sample components for free laboratory testing and application engineering evaluation at the blast machine builder's factory in northeastern New York State.
For more information contact:
John C. Carson
Guyson Corp.
13 Grande Blvd.
Saratoga Springs, NY 12866-9090
800-633-6677
518-587-7894
info@guyson.com
www.guyson.com