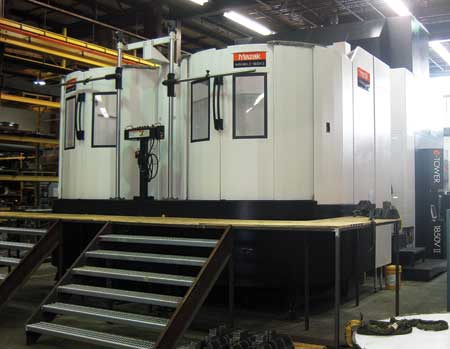
Mazak Integrex installed at Zak Inc.
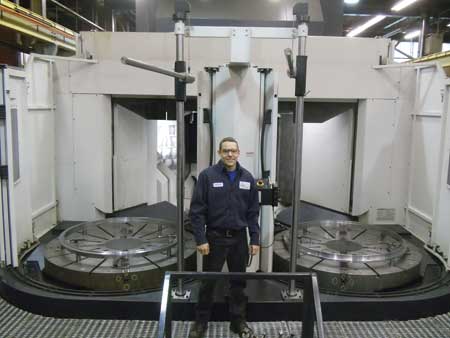
CNC machinist Barry Morehouse with the Mazak Integrex's dual pallets.
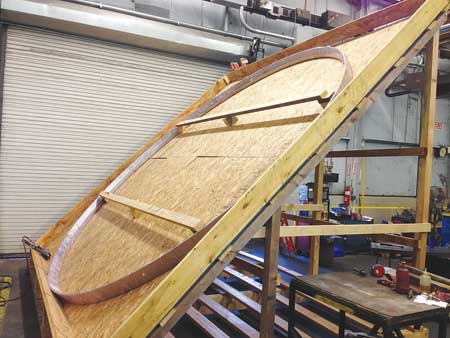
Angled shipping crate for a 189" OD ring for the hydropower industry.
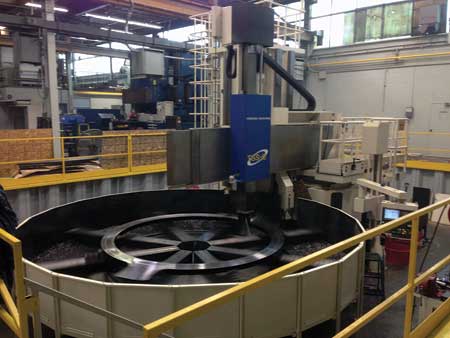
Toshiba TSS turning a 124" OD ring.
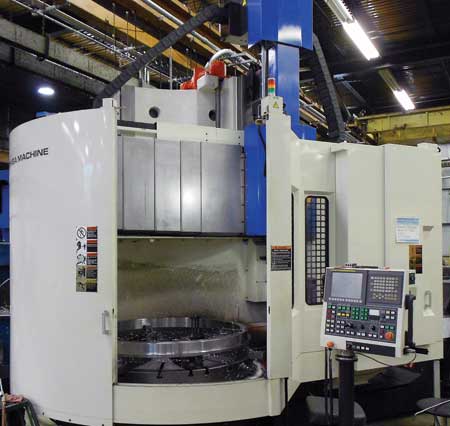
Toshiba TUE at Zak Inc.
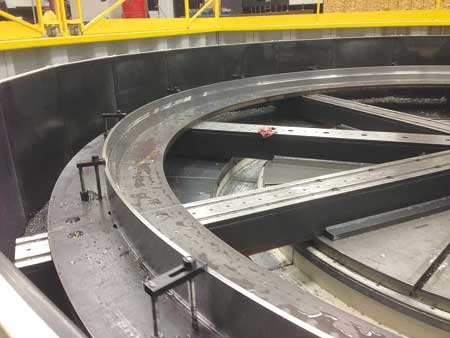
Machining a 189" OD ring for the hydropower industry.
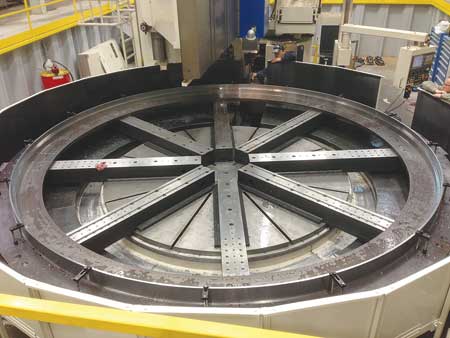
Toshiba TSS turning a 189" OD ring.
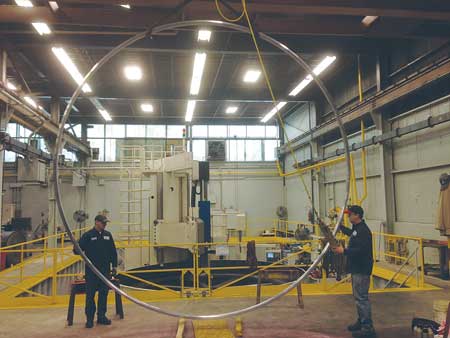
Bernie Daoust and Mike Dolan, CNC machinists, positioning a 189" OD ring for non-destructive testing.
Zak Incorporated, a contract manufacturer for the power generation, oil and gas, aerospace, defense and heavy machinery industries, faced the challenges of providing increasingly complex work and improving throughput. Higher productivity and reliability, exceptional quality and process repeatability, as well as expanded capabilities and manufacturing capacity were the goals President Mike Dagle and his team set out to accomplish.
With the need to both upgrade and expand, the team initially explored the option of retrofitting and rebuilding their existing equipment. However, after an in-depth analysis and evaluation, they decided that the productivity gains associated with multifunctional CNC machining centers exceeded the efficiencies and return associated with existing equipment rebuilds.
"This is not a first for the team at Zak Incorporated," said a company spokesperson. "Zak became one of the first machine shops in the Northeast to adopt multifunctional tooling technology when it installed its Phoenix VTL (with 180 inch swing capability) in 2002 and its smaller Okuma V80R VTL (with 40 inch swing capability) in 2007. The increased productivity of these work centers, and their ability to minimize the movement and setup of large, heavy components, were key factors in Zak's decision to continue to focus on multifunctional tooling technology."
"With a globally competitive marketplace, the challenges on us as a supplier are ever more demanding in terms of our quality performance, cost competitiveness and the reliability of our delivery fulfillment," said Mike Dagle, President, Zak Incorporated. "In order to successfully meet these ever changing business challenges, we determined that we had no choice but to invest in the newest CNC machining center technology and we had to expand upon an already highly trained work force."
The team selected the Mazak Integrex e-1850v II VTL as the first replacement unit to be added to Zak's equipment lineup. With 5-axis machining capability, the Integrex leverages its dual pallet and live tooling to machine parts by reducing setups and improving efficiencies. Size capabilities of up to 92.5" in diameter by 71" in height allow the Integrex to play a versatile roll in reducing cycle times and cost while increasing the overall throughput capacity of the facility, according to a company spokesperson.
Once the 5-axis Integrex was installed and operational, additional turning centers were analyzed by the Zak team and the Toshiba TUE-150(S) VTL and Toshiba TSS-30/55C(S) VTL were chosen. "With the ability of the TUE to mill, drill and turn parts up to 78 inches in diameter and 78 inches in height, our mid-range turning capability significantly improved," said Kevin Burriesci, Assistant Sales Manager. "The TSS further increased our size capabilities by becoming the largest machine to ever be installed at our facility. The Toshiba TSS utilizes a special Zak designed and fabricated enclosure to machine parts up to 216 inches in diameter and 131 inches in height. Its multifunctional tooling capability allowed us to expand our part size capability and significantly increase capacity."
Burriesci said the new machines have allowed the company to maintain its current footprint (plant size) in Green Island, NY, while significantly improving throughput capacity and increasing the complexity of its machining capabilities. "By utilizing state-of-the-art multifunctional tooling with 4- and 5-axis capabilities, our new CNC machining centers have allowed us to improve efficiencies by reducing setups and reducing labor touch points," he said. "Our new machining centers have given us the ability to successfully grow our business within the accounts and markets we already serve, and to increase our revenue growth by entering into new and expanding industries. Today, our organization is poised to continue to grow and effectively improve upon its 75 years of success."
Zak Incorporated operates within two distinct markets: (1) as a contract manufacturer, machining and fabricating parts and assemblies for original equipment manufacturers and (2) within the specialty melting industry through the design and fabrication of copper molds and crucibles. Typical materials machined and fabricated include steel, aluminum and copper in the form of forgings, castings, plate and bar.
"These machines can hold tolerances of .0005-inch," said Joe Pratt, Sr. Engineer. "The all-new Mazatrol Matrix 2 and the latest FANUC series controllers offer unmatched operator interface, allowing faster set up time and more accuracy in production. The recent introduction of an off-line tool pre-setter further enhances the setup time reductions by having all of the required tool offsets pre-loaded into the machine control."
The Mazak Integrex e-1850v II features the following:
- Maximum swing: 92.52" (2,350 mm)
- Maximum cutting height: 70.87" (1,800 mm)
- Maximum table load: 15,400 lbf. (7,000 kg)
- Maximum spindle torque: 372.5 ft-lbs (505 Nm)
- Table drive motor (30 min/cont.): AC 45/37 kW
- Spindle drive motor (30 min/cont.): AC 37/30 kW
- Additional information: 5-axis, Dual Pallet
The Toshiba TUE-150(S) features the following:
- Maximum swing: 78.74" (2,000 mm)
- Maximum cutting height: 61.02" (1,550 mm)
- Maximum table load: 17,600 lbf (8,000 kg)
- Maximum spindle torque: 172.44 ft-lbs (233 Nm)
- Table drive motor (30 min/cont.): AC 45/37 kW
- Spindle drive motor (30 min/cont.): AC 18.5/15 kW
- Additional information: 4-axis
The Toshiba TSS-30/55C(S) features the following:
- Maximum swing: 216.5" (5,500 mm)
- Maximum cutting height: 102.3" (2,600 mm)
- Maximum table load: 44,090 lbf (20,000 kg)
- Maximum spindle torque: 258 ft-lbs (350 Nm)
- Table drive motor (30 min/cont.): AC 45/37 kW
- Spindle drive motor (30 min/cont.): AC 18.5/15 kW
- Additional information: 4-axis.
Zak specializes in large, precision machined rings and ring-shaped assemblies along with specialized copper products, including molds and crucibles. Typically, it provides complete turnkey manufacturing services. This includes raw material procurement and testing, precision machining operations (including turning and/or milling and/or drilling), final assembly and/or fabrication, and final inspection and testing. Parts are frequently assembled with custom manufactured or purchased hardware and/or fabricated in its weld shop. Every part, assembly and fabrication is inspected in-house. "Zak's turnkey manufacturing services provide efficient and cost competitive solutions for OEMs that require large machining, assembly and/or fabrication," said the spokesperson.
"With precision machining as the most significant value-added factor in the products we produce, it was imperative that our new equipment help us to improve our machining efficiency," said Burriesci. "Since installing the new machines, we have seen a clear reduction in both setup and machining time. Our new multifunctional work centers have allowed us to completely eliminate some setups, which has dramatically reduced material handling time and has allowed us to reapply those resources to further improve our processes. These machines have also allowed us to reduce our machining hours while simultaneously improving the quality of our work."
Founded in 1937 by Alexander F. Zak, Zak Inc. has evolved from serving the local textile industry to supplying precision machined components to customers across a broad range of industries. Zak Incorporated remains a family owned company and is currently owned by third generation Chairman, Douglas Zak.
As an ISO 9001:2008 certified manufacturing facility, Zak Inc. has a fully qualified quality management system and a full lineup of in-house inspection capabilities (including CMM capabilities) along with qualified third party Level III NDT service providers. Zak also has a drafting and design team in-house to support its copper crucible and mold business.
"With the new equipment, we are more strongly positioned to service our existing customer base and take on new work," said Dagle. "This new equipment capacity and capability plays a major part of the new business growth plans that we have for our Green Island, NY, location."
For more information contact:
Kevin Burriesci, Assistant Sales Manager
Zak Incorporated
1 Tibbits Avenue
Green Island, NY 12183
518-273-3912 ext. 16
kburriesci@zakinc.com
www.zakinc.com