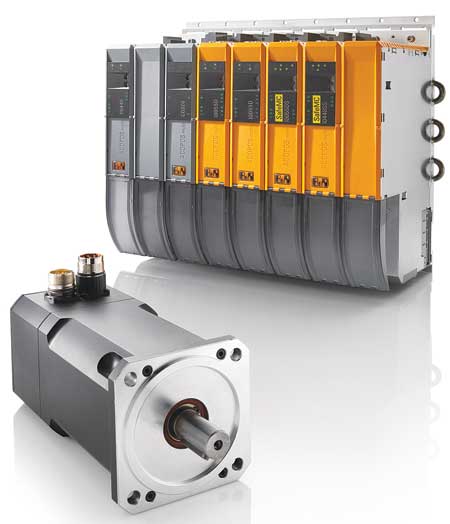
With cold-plate control cabinet installation, heat from drives can be directly dissipated and used, for example, as heat for the process. According to B&R, this saves the cost of control cabinet cooling devices as well as the energy they consume.
"Because of increased environmental awareness and to take advantage of new business opportunities, more and more machine and system manufacturers are choosing to implement innovative motion control technologies," said a B&R spokesperson. "If motors and drive components are generally working with a level of efficiency near 100% when operating at the rated load, it makes sense to have a look at the secondary components around the actual drive system."
"The sum of many individual measures can turn out to be very significant," said Alois Holzleitner, Business Manager for Motion Control at B&R. "When using the right components, large amounts of energy can be saved in the area around the drive system with relatively little effort."
B&R ensures that drives can be sized in a targeted manner using the SERVOsoft tool from ControlEng, according to the company. The masses to be moved and the drives needed to do it can be perfectly matched, which reduces energy consumption to a minimum.
For complex machines where movements are executed consecutively, kinetic energy is often released in the braking resistors in the form of heat. By connecting ACOPOSmulti servo drives via the DC bus, the company has reported that up to 30% of the energy used for movements can be saved. Brake energy is stored in capacitors and made available at a later time for acceleration. "The user profits not only from efficient use of energy, but also from a cooler control cabinet because the heat from the resistors is greatly reduced," said the spokesperson.
In cases where braking and acceleration within an axis group do not often take place simultaneously, a further increase in energy efficiency can be achieved through active energy regeneration on the power mains. While all of the brake energy is put to use, unavoidable friction remains as the sole source of loss. With the use of modern ACOPOSmulti drive systems, B&R said it is possible to cost-effectively regenerate up to 80% of the energy previously lost as heat in the resistors.
Energy-saving measures are supported by B&R through cold-plate control cabinet installation. This provides the option of using the energy from heat loss that occurs in the servo drives themselves where it is needed via fluid circulation and a heat exchanger. "A big advantage of cold-plate technology is that a separate cooling device is no longer needed for the control cabinet," said Alois Holzleitner. "This provides savings of up to 23%."
A further energy-saving effect of using the ACOPOSmulti family of products is correcting the total power factor (TPF) to 1.0. "While conventional inverters with a small TPF exhibit considerably higher effective power consumption, which leads to unnecessary loss in the supply lines and transformers, the active power supply of the ACOPOSmulti ensures that the energy is used efficiently," said the spokesperson. "This saves up to 50% of the infrastructure costs by reducing the size of wires, feed components and fuses."
For more information contact:
B&R Industrial Automation Corp.
1250 Northmeadow Parkway, S-100
Roswell, GA 30076
770-772-0400
www.br-automation.com