

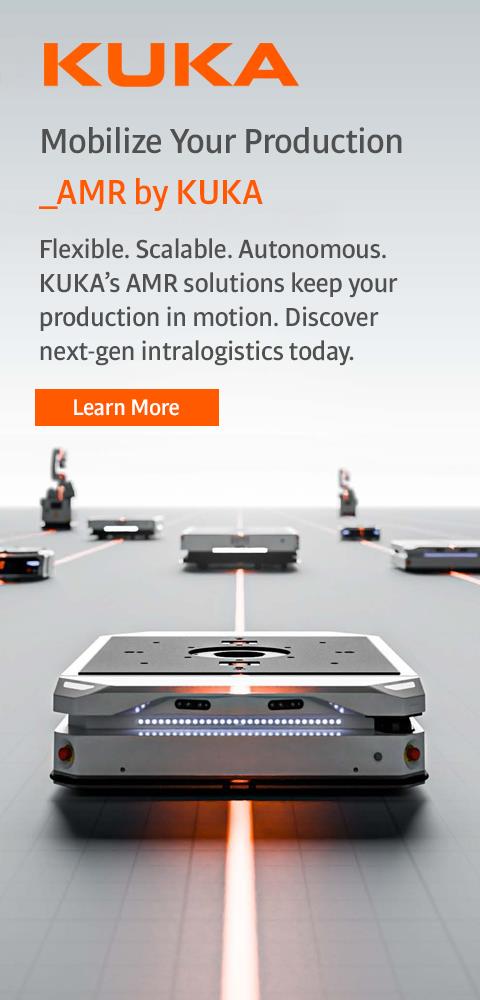
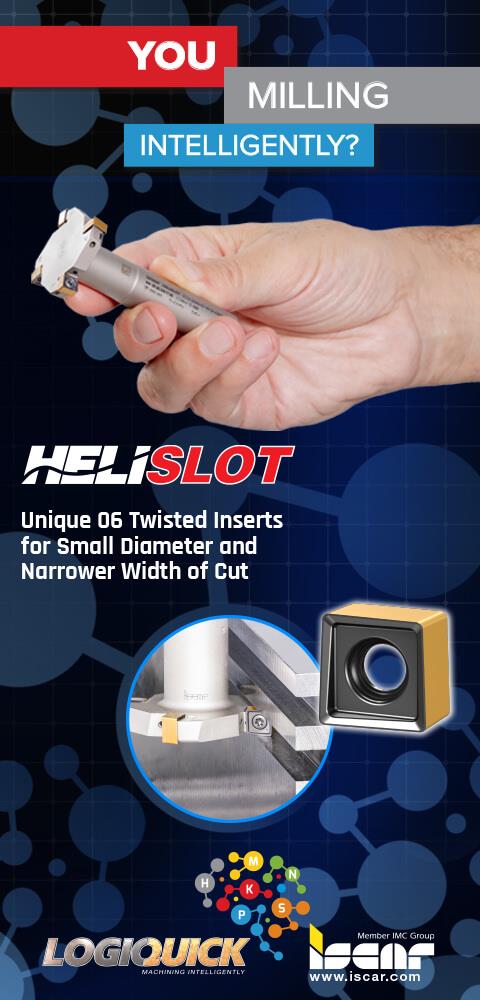
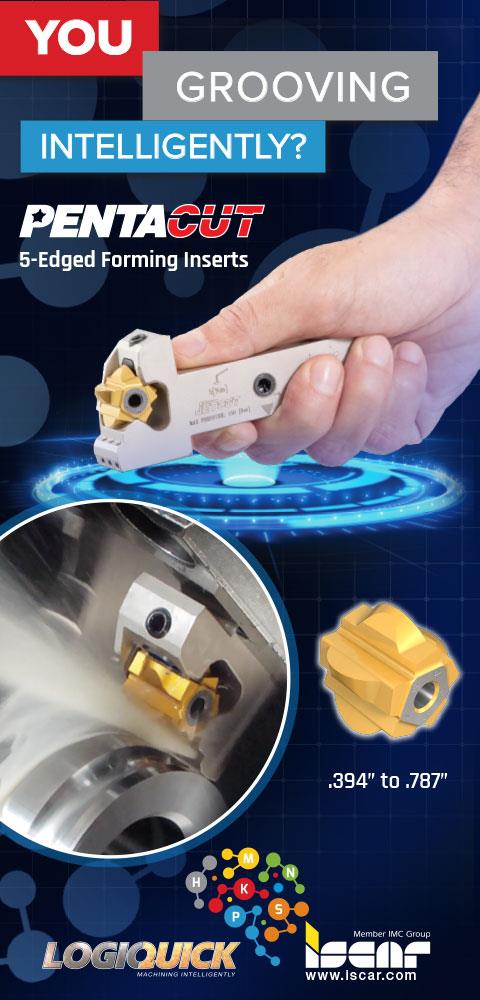
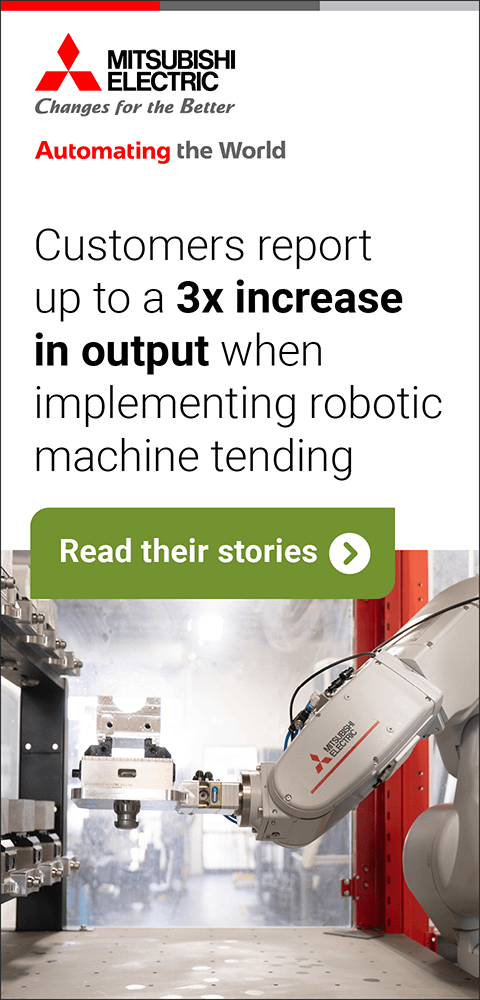
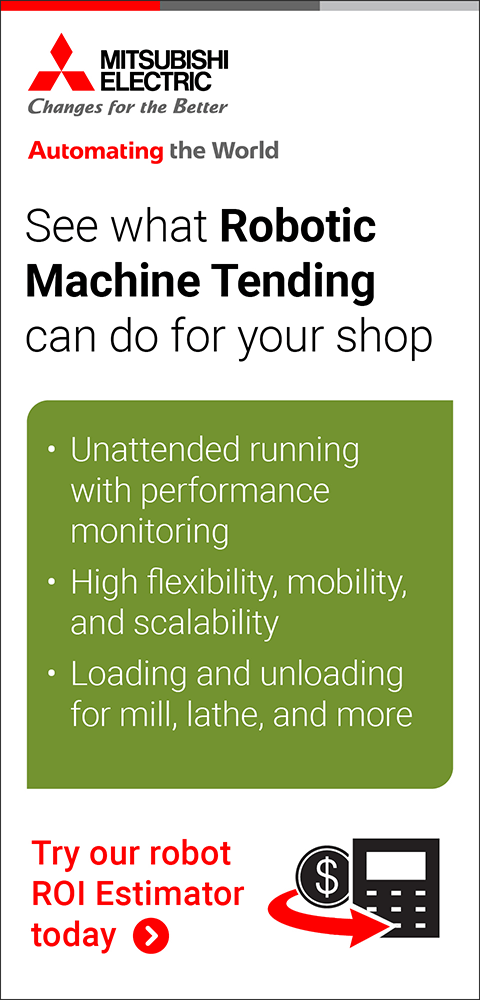
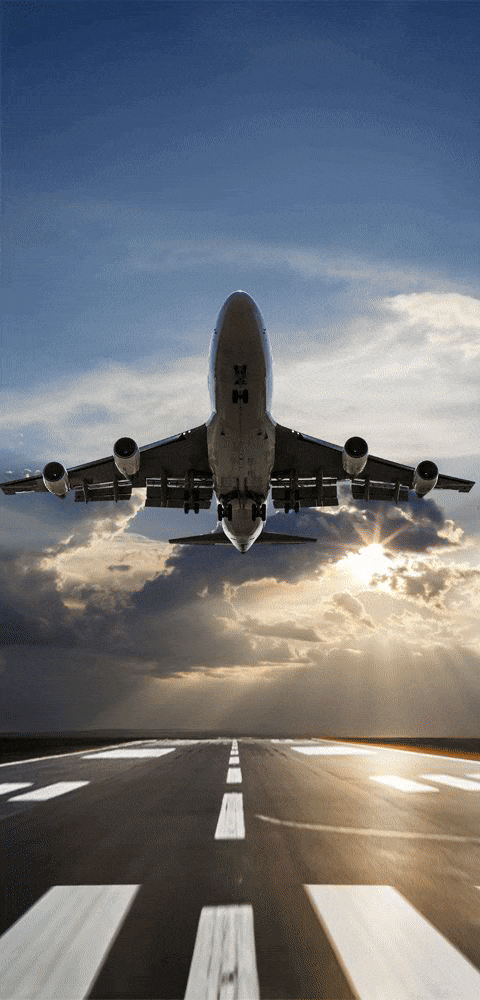
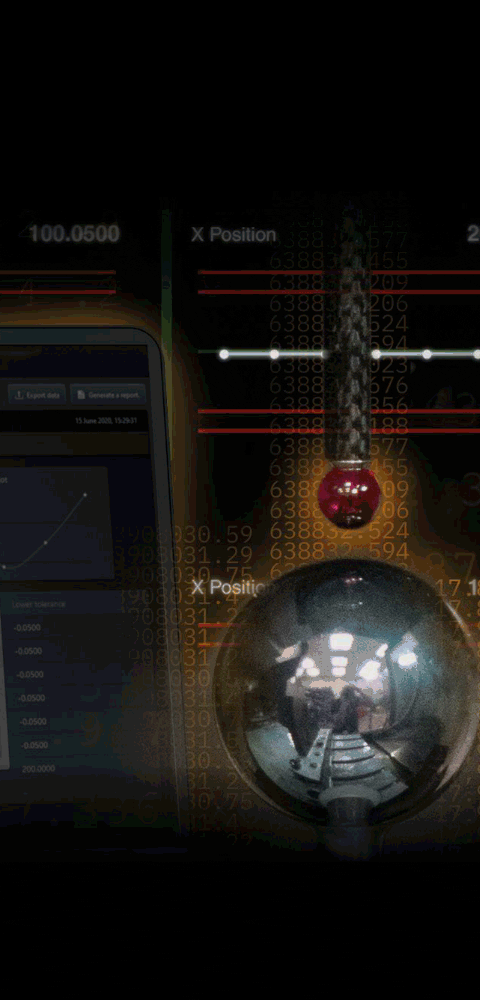
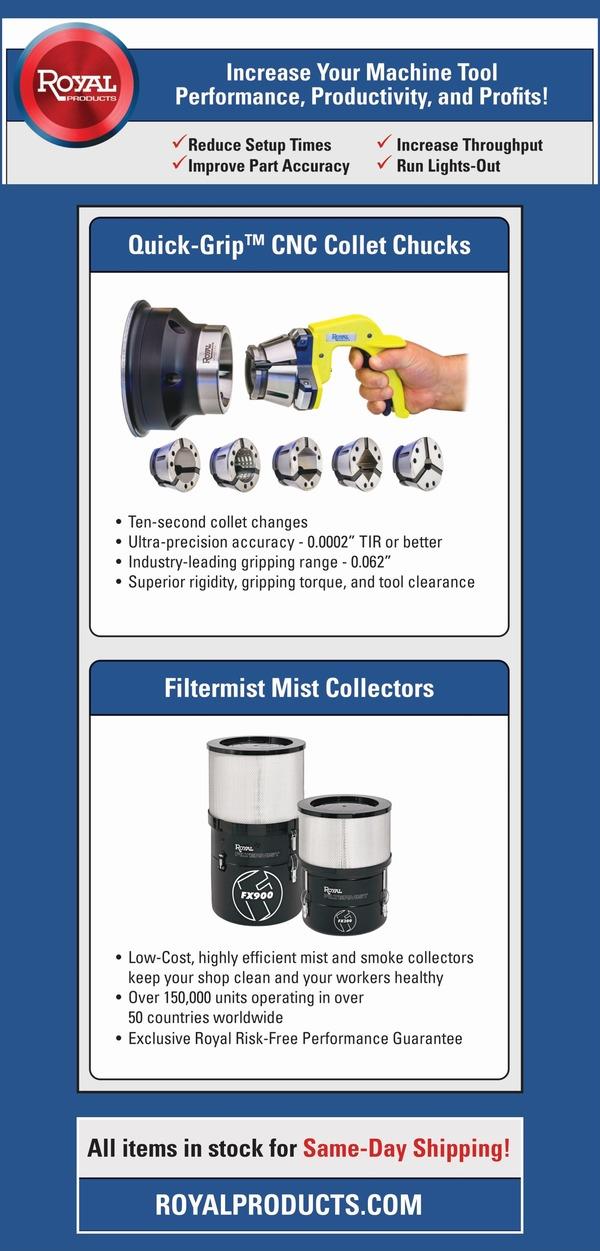
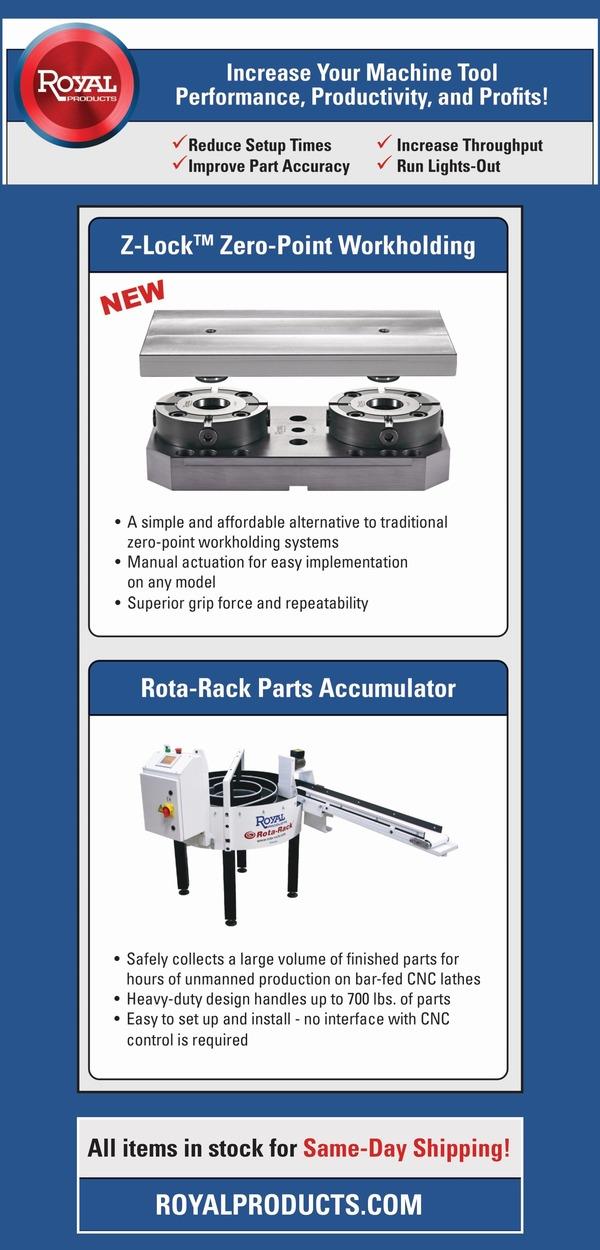
Destacker Tooling Design Feeds Aluminum and Steel Blanks
July 1, 2013
Bilsing Automation has developed flexible destacking technology that can separate and feed both steel and aluminum blanks in various sizes and configurations. The solution was designed and engineered by Bilsing for flexibility where the end effector can handle multiple parts. It is comprised of the company's 2.5" diameter aluminum round body tooling and other Bilsing components.
"Whereas traditional steel blank destacking systems rely on magnetic holders for separating the blanks before lifting and transfer, aluminum has no magnetic qualities," said a company spokesperson. "Typical aluminum destacker systems employ peel cylinders to lift the corners of the blank with air knives that shoot air in that space to break the vacuum. Another issue is that lubrication on the blanks acts like a glue agent, causing the blanks to stick together.
"To overcome these issues, Bilsing compiled field data for strategic placement of the peel cylinders in its design. During a cycle, the automation lowers so that the peeler suction cups are all level, with the front cups being spring-loaded and programmed to fire just slightly prior to the other cups. The air knives then fire to help peel back the top sheet - breaking the vacuum, which assists in separating the blanks."
Bilsing originally developed this solution for a customer that wanted to bring components of varying materials running on three different lines to a single pressline.
For more information contact:
Bilsing Automation - North America
22287 Starks Drive
Clinton Township, MI 48036
586-463-0686
info.na@bilsing-automation.com
www.bilsing-automation.com
< back