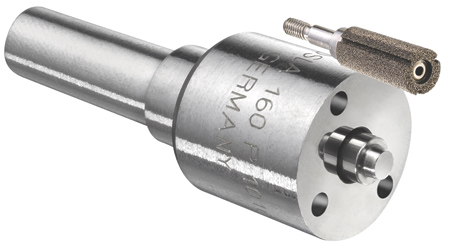
Fuel injector nozzle bores are ground to a smooth finish using tiny wheels extended into the narrow bore via disproportionately long quills. Deflection issues resulting from this relatively unstable configuration make it difficult to maintain increasingly tight taper and cylindricity tolerances without sacrificing other important process attributes. (e.g., surface finish, cycle times and/or wheel life). A new 3D Abrasives Technology from Meister Abrasives can significantly ameliorate these problems.
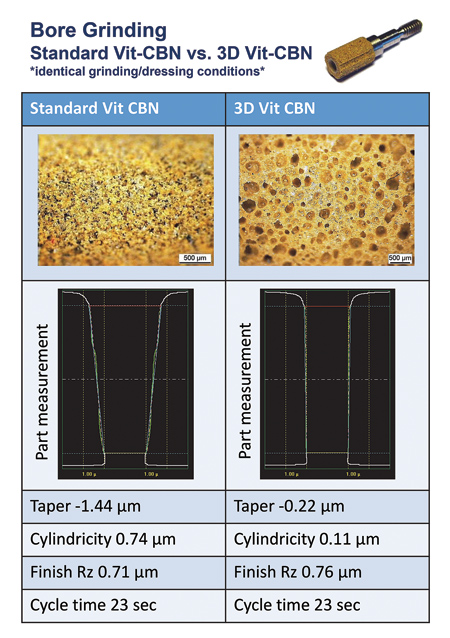
The need to achieve better fuel economy is driving the requirement of increasingly tighter form tolerances for fuel injector bores. However, tight fuel injector bore tolerances are very difficult to achieve because these nozzles have very high length to diameter ratios and they must be ground using tiny wheels extended from long quills that deflect readily. This relatively unstable configuration makes it very difficult to grind fuel injector nozzle bores and avoid tapering, in one direction or the other, and maintain cylindricity within very narrow bands.
Manufacturers have tried several conventional solutions to this problem and rejected them:
- Using sharper wheels, which are achieved by dressing more aggressively. However, this often results in rougher surface finishes that can only be improved by slowing the grinding process - a modification that is totally unacceptable in a 24/7 production environment.
- Using softer wheels would provide better finish and form tolerances. However, these wheels would break down more rapidly, adding costs and diminishing productivity.
- Using very fine mesh abrasive wheels could achieve the desired finish and form tolerances, but fine grit wheels with conventional bonding have not been able to handle the advanced nozzle materials at full production rates without burning or loading.
3D Abrasive Technology Solution
Meister Abrasives' innovative new 3D Abrasives Technology was developed as an answer to the concerns outlined above. "3D Technology makes it possible to secure the tiniest grains of CBN or diamond within the most open, self-sharpening bonding matrices ever created," said a company spokesperson. "It is ideally suited for applications where grinding processes are inhibited by hard materials that must be ground to micro-precision form, finish and ever-tightening geometrical tolerances and where low grinding forces are essential to minimize deflection."
Before the introduction of the 3D Technology, the porosity of a wheel (its openness) had to be reduced by the manufacturer as grain sizes diminished for finish grinding applications. The new 3D Technology eliminates this restriction, making it possible to incorporate grits ranging from 10-50 microns within matrices that have pores as large as 500 microns.
The new 3D wheel structure tends to reduce forces within the grinding process that would otherwise deflect the quill or distort thin-walled part features. To compensate for such forces, manufacturers often needed to grind less aggressively for longer cycles. With 3D Abrasive Technology, compensation correction that the CNC grinding machine provides for optimizing the bore requires significantly lower values. Users can grind with lower force but without having to back off on other grinding process settings.
Comparison
To test the viability of the new abrasive technology for improving fuel injection nozzle form tolerances without sacrificing other important variables, Meister Abrasives conducted a laboratory study comparing an existing nozzle grinding process with one that changed just one variable - the grinding wheel itself.
Trials were conducted using the current benchmark standard Vit-CBN wheel and then with a 3D Vit-CBN wheel. The CBN type, grit size, concentration, wheel hardness and the shank were all held constant. Identical process conditions, including grind and dressing parameters, were also held constant. Everything was the same, except for the bonding technology.
There was a 7x improvement in taper and a 7x improvement in cylindricity with virtually no change in the required surface finish precision. "In this application, 3D Abrasives significantly out-performed the heretofore best available abrasives technology for grinding fuel injector nozzles without sacrificing anything," said the spokesperson.
Meister engineers attribute the success of this product to the extreme openness of the wheel's pores, which bring in more coolant to flush away more material with each grinding wheel rotation. Free flow of coolant also lowers part temperature to limit the potential for burning. Tiny abrasive grains projecting out from the wheel's honeycomb-like bonding matrix make for sharper cuts, but grinding forces are reduced because the matrix itself and the part have minimal surface contact. Reduction of forces that cause grinding quills to deflect and hard wheels to bounce are the keys to minimizing unwanted taper and cylindricity deviations in this application.
No attempts were made in this study to adjust grinding parameters to achieve a different balance of results, for example sacrificing some of the taper improvements to obtain faster cycles and greater productivity. These considerations, of course, would be part of a normal grinding process development protocol.
There are many other grinding applications in which 3D Abrasives Technology is under consideration for extending grinding performance beyond the limitations of current best practice solutions.
Meister Abrasives is an international manufacturer of industrial abrasive products, offering superabrasive grinding wheels, dressing tools, ancillary equipment and technical support to provide customers with optimized solutions for high-precision grinding applications.
For more information contact:
Meister Abrasives USA, Inc.
201 Circuit Drive
North Kingstown, RI 02852
401-294-2530
sales@meister-sbrasives-usa.com
www.meister-abrasives-usa.com