
Manual or Hydraulic Fixtures?
February 1, 2014
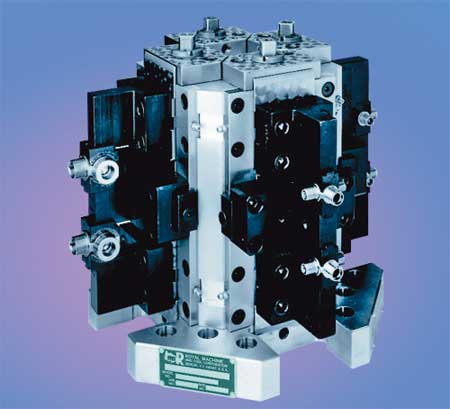
Multi-part manual fixture with each part individually clamped by the operator.
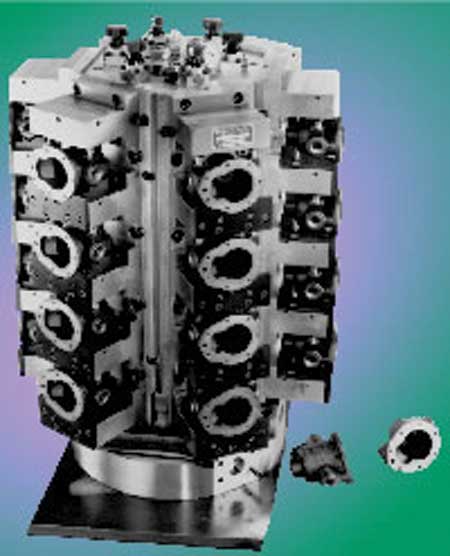
Multi-part hydraulic fixture complete with check valves, sequence valves and part load confirmation.
"Chucking a part manually has always taken precedence for a number of reasons," said a Royal Machine & Tool (RMT) spokesperson. "Manual clamping is usually simpler and more cost effective for most low volume parts and requires very little maintenance. Therefore, based on these major reasons for using manual clamping, why then consider using hydraulic clamping?"
Before deciding on manual or hydraulic clamping, RMT offers a number of factors to consider:
- Part seating: First, what is the nature of the part to be gripped? The part's configuration must be evaluated. It may not be conducive for hydraulic clamping because of datum locations or areas with little access to hold the part with a hydraulic clamp. In addition, some parts may require only hand loading to clear the clamping units and sit properly in the work nest. However, many hydraulic fixtures hold a number of parts and they are all clamped simultaneously.
- Production: What is the daily volume of parts to be manufactured? For a small volume of work there would be no justification for using hydraulic clamping. Should there be a large volume to run, the load/unload time can be greatly decreased using hydraulic fixtures.
- Automation: Is automation included in the process? The part must be able to sit firmly on the work locators or in the work nest without manual intervention to hold the part while clamping. This may require some type of load assist device as simple as a spring clip. Also, accessibility by the load device is required. Plus, an air blow-off to clear chips is recommended as well as some means to confirm that the part is seated at clamping to ensure the piece is secure in the fixture and not a loose safety hazard.
- Chip evacuation: Is there a possibility of harmful chips piling up? Chips cause havoc many times. If hard piping is used, it will cause an area for chips to pile up and wrap around the piping. RMT provides all the hydraulic flow within the tombstone and does not use hard piping for this reason. If not addressed initially, this may cause an increase in the load/unload time.
- Tool path: Is the tool path inhibited? Hydraulic clamps can take up a great deal of room, especially swing type clamps, which may inhibit the tool path and size of the tools required to machine the part. Larger parts may require larger clamps to provide the required gripping forces - sometimes leading to complications in the design and not allowing sufficient room for machining.
- Changeover: Is going from one part to another an issue? Moving of the clamping areas is not very feasible or recommended. It increases the chances for hydraulic leaks. Most hydraulic fixtures are dedicated to a particular part, but this is not always the case. With some thought, it may be possible to cover a number of parts with the same set-up.
- Costs: In the manufacturing of the work nests and plates, hydraulic fixtures are more costly than manual fixtures. Hydraulic clamping cylinders are more complicated - the hydraulic unit alone may add up to an additional $4,000. Keeping hydraulic fluid clean of contaminants requires additional maintenance. In addition, check valves, sequence valves and accumulators are required.
- Advantages: Hydraulic clamping offers consistent clamping of the part in each cycle, as opposed the time consuming process of having the operator tighten the part each time. On thin parts the possibility of distortion is greatly reduced. Finally, hydraulic clamping allows clamping more than one part at a time - improving load/unload time.
For more information contact:
Bernie McAloon, Sales Manager
Royal Machine & Tool Corp.
P.O. Box Y
4 Willow Brook Drive
Berlin, CT 06037
860-828-6555
royal@royalworkholding.com
www.royalworkholding.com
< back