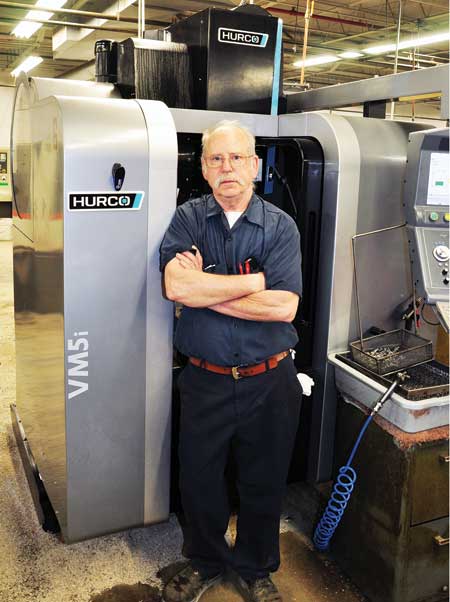
Doug Pekari, Shop Manager, with the Hurco VM5i.
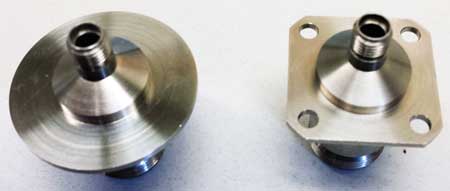
This part was made out of round bar and the holes were drilled and the square was milled as a second operation on the Hurco. "We used to make this out of square bar because it would take too much time to mill the square," said Parillo. "With the Hurco we can line up six to 10 at once and mill and drill. Speed and ease of programming allows this to be accomplished. As a result, we can use round bar, which is much cheaper, machines better and is easier to acquire."
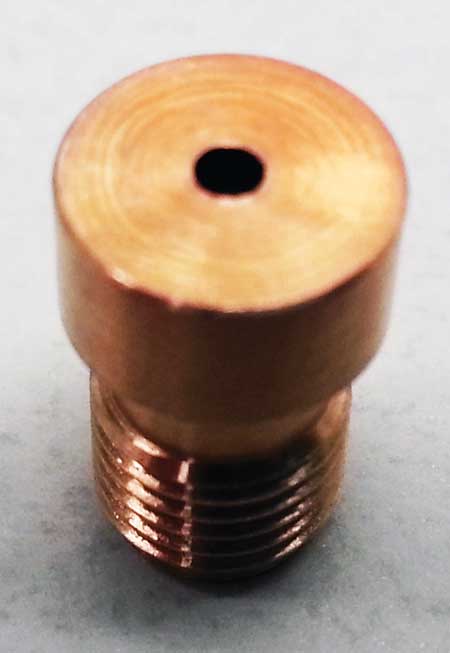
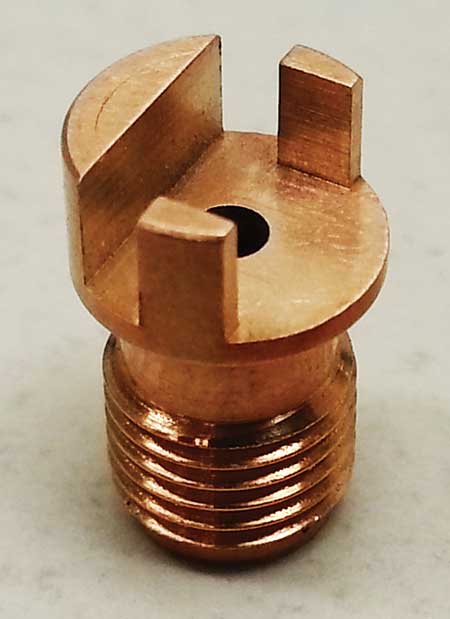
This RF edge launch connector has the tabs machined as a second operation. This was previously done on an older CNC milling machine, but the operators could only machine one part at a time because dimensions would go out of tolerance. With the Hurco, they are able to machine 12 parts at one time.
Manufacturers Associates, Inc. specializes in small, complex parts that span a variety of industries, such as aerospace, communications, defense, electronics and fiber optics. Even though the core business has remained constant, Manufacturers Associates has expanded its services to include precision turning, precision milling, secondary operations, mechanical assembly, inspection and CAD/CAM.
Doug Pekari, Shop Manager, made a strategic decision to update the milling department that is used for secondary operations. He considered repairing his older equipment and buying new. He needed a CNC machine that was easy to use, flexible, would reduce set-up time, reduce cycle time and increase flexibility in job changeover.
"We have a broad mix of products, and quantities are trending down, so set-up reduction is very important to us," said Pekari. "Ultimately, we selected the Hurco VM5i CNC mill because of its powerful control and unusually small footprint. The Hurco control allows us to set up and break down two or three times a day with minimal spindle downtime. The Hurco VM5 is also extremely compact for a 40 taper machining center. Floor space is at a premium in our shop and the VM5i has a minimal footprint without sacrificing performance." Another key factor in selecting the Hurco VM5i was the control's conversational programming that lets the machinist program and edit right at the machine instead of using an off-line CAM system.
Pekari said the selection of this second Hurco mill (the company purchased a Hurco VM10 in 2001) has been good for the company's bottom line. He is seeing better throughput, sometimes up to 30%, increased accuracy and improved surface finishes.
One part was made out of round bar and the holes were drilled and the square was milled as a second operation in the Hurco. "We used to make this out of square bar because it would take too much time to mill the square," said Anthony Parillo, Jr. "With the Hurco, we can line up six to 10 pieces at once and mill and drill. Speed and ease of programming allow this to be accomplished. As a result, we can use round bar, which is much cheaper, machines better and is easier to come by."
An additional component being manufactured on the Hurco VM5i is an RF edge launch connector that has tabs machined as a second operation. This was previously done on an older CNC milling machine. "We were only able to do one part at a time because the repeatability of the machine would not allow us to do more than one piece because dimensions would go out of tolerance," said Parillo. "Therefore man-hours were lost because the operator would have to be at the machine constantly loading each part individually. With the Hurco we are able to machine 12 parts at one time. As a result, the operator can run three more machines because he loads 12 of these parts at once and walks away from the machine - saving on labor so the operator has time to load other machines. Due to the rapid tool change, accuracy and increased spindle speed the per piece cycle time is cut by 75%, greatly increasing productivity.
"With a user friendly control the operator can understand and feel confident when he needs to make adjustments. The controls allow us to pin point a single dimension on just one of the 12 parts we are machining rather than having to rewrite the whole program, which had to be done with the old machines."
"Because of the Hurco mill's ease of use, accuracy, dependability, versatility and most of all efficiency, we are able to cut down on labor, operations and cycle time - which saves money and we get a better looking part in the end," said Pekari. "The return on investment has exceeded our expectations. We are very pleased to have found a compact, reliable machine that is easy to use."
The Hurco VM5i has a small footprint and only requires 65" x 88.2" of floor space, but has XYZ travels of 18" x 14" x 14", a 10 HP spindle and 16-station ATC. Table size is 18" x 14" (457 mm x 356 mm).
In addition to continually investing in equipment with the latest technology, Manufacturers Associates is dedicated to quality as an ISO 9001:2008 registered company. According to Pekari, the company has implemented a dynamic Quality Management System. "The commitment to quality is further evidenced by the distinction between Quality Assurance and Quality Control," said Pekari. "Each department is headed by its own member of executive management, an investment unheard of in a precision fabrication facility of this size. While the Quality Control Manager can ensure the product meets the customer's requirements, continually improves the production processes and provides customer-required documentation in any format desired, the Quality Assurance Manager can focus efforts on continual improvement of the Quality Management System, implementation and customer focus."
As Manufacturers Associates looks to the future, they plan to grow by incorporating even more services so that their customers have a "go-to supplier" for all their needs.
Manufacturers Associates, Inc. is a family-owned machine shop with more than 70 years of manufacturing experience. Anthony Parillo, Sr. was a co-founder of New Haven Manufacturing. During World War II New Haven Screw Machine Products was the recipient of the Army-Navy "E" Award that was given to companies for efficiency in production of critical war materials. Parillo started his own shop, Whiting Screw Machine Products, in 1946, which ultimately became Manufacturers Associates. Later, he moved the shop to Hamden, CT, and the second generation, Anthony Parillo, Jr., came on board in the 1960s. The third generation, Anthony T. Parillo, joined the company in the mid-1990s. It was 1996 when the family moved the company to its current location in West Haven, CT, and renamed it Manufacturers Associates to better reflect its diverse product line as one of the largest manufacturers of RF / microwave connector bodies.
The company originally started with a single spindle Brown & Sharpe screw machine. Today it has more than 150 machines to fulfill the diversity of services it provides its customers.
For more information contact:
Manufacturers Associates, Inc.
45 Railroad Avenue
West Haven, CT 06516
203-931-4344
sales@manufacturersassociates.com
www.manufacturersassociates.com
Hurco Companies, Inc.
One Technology Way
P.O. Box 68180
Indianapolis, IN 46268
800-634-2416
317-298-2622
info@hurco.com
www.hurco.com
ME, VT, NH, CT, MA, RI, N. NJ, NY (far South)
Michael Klier
Brooks Associates, Inc.
300 Longwater Dr, Unit A
Norwell, MA 02061
860-460-9664
mikeklier@comcast.net
www.brooksmachinery.com