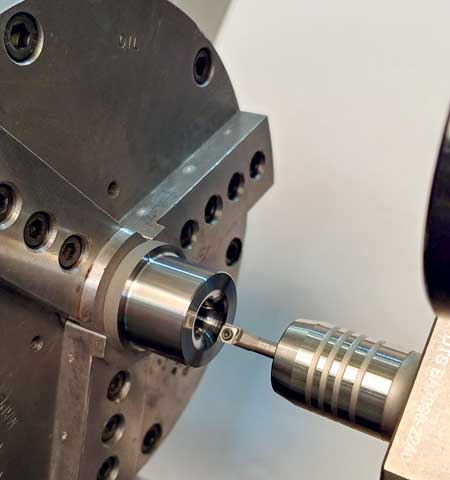
Hard turning of a carbide draw die on a Hembrug Mikroturn 100 lathe.
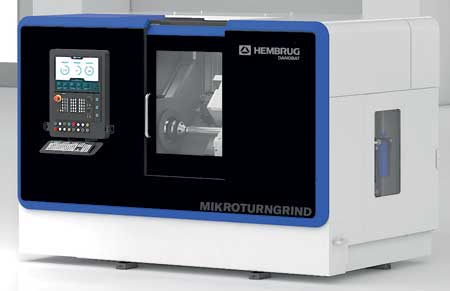
The newly designed, fully hydrostatic Hembrug Mikroturn 100 3rd generation.
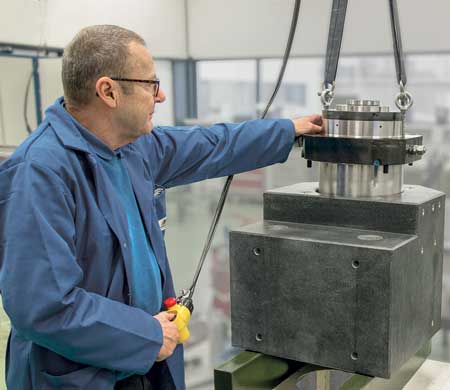
Construction of a Hembrug hydrostatic main spindle in a granite housing.
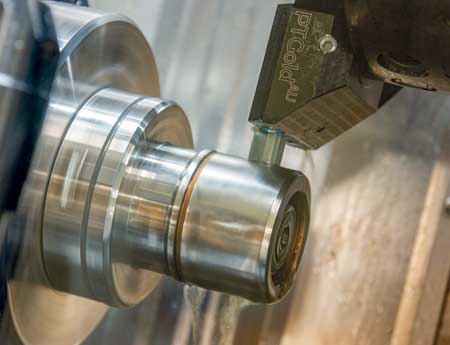
Stone honing after turning makes surface finishes of Ra 0.02 µm possible.
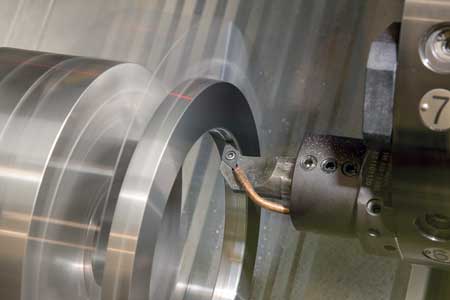
This draw die was made within 30 minutes compared to the old grinding process of 8 hours with similar accuracy results.
Tungsten carbide tooling is widely used in the mold and die industry for punching, drawing and extrusion applications. This tooling is known for its wear resistance and complex contours, which require the highest standards of form and surface finish. Traditionally, these workpieces have been finished using grinding machines due to their difficult machinability.
A flexible manufacturing process for finishing carbide tooling is now possible with the combined effect of a dynamically stiff and accurate turning machine.
High precision turning is a very flexible process. It is easy to set up and change over, achieving high metal removal rates. The greatest advantage is the ease with which complex contours can be programmed and machined.
Optimal machine and tooling are key to successfully turning tungsten carbide to the same accuracy as grinding. Often referred to as "hard metal" due to its very high hardness, tungsten carbide can have a hardness value of 80 Rockwell C. In comparison, the hardness of hardened steel is typically in the range of 58 to 64 Rockwell C.
Turning this material on a conventional precision lathe will result in high vibrations due to minimal machine damping characteristics. The elevated cutting forces required to remove material from the workpiece are higher in tungsten carbide than in hardened steel. These higher cutting forces result in significant pushback pressure on the guideways and spindle bearings. Conventional turning machines are not designed to handle these forces, leading to premature wear of the guideways, even in hardened steel, let alone carbide. This results in a drop-off in size holding capability, form accuracies, surface finishes and increased tool wear.
The Dutch builder Hembrug Machine Tools, part of the Spanish machine tool group Danobat, specializes in the development and construction of high precision hard turning machines. They also have extensive process experience turning ultra-tight tolerance tungsten carbide workpieces where sub-micron accuracy is needed.
This in-house developed technology is applied to the slide-way and spindle bearings in every Hembrug Mikroturn machine model. It provides increased damping properties along with high dynamic stiffness, independent of speed, necessary to minimize vibrations at the tool tip. These characteristics are essential for surface finish integrity and extended tool life. The absence of metal-to-metal contact between moving machine elements results in a completely wear-free platform with low operational costs and everlasting accuracy.
With this level of design and construction, together with a natural granite machine base, there is a higher upfront investment compared to a conventional precision lathe. The benefit is longer tool life, fewer adjustments, consistent piece-to-piece repetitive accuracies due to its inherent stability, and most importantly, workpiece quality on par with grinding tolerances.
Hembrug, owned by Danobat, often leverages Danobat's expertise in precision grinding to integrate advanced grinding technology into its machines. Depending on the application, it may be beneficial to pre-turn parts, followed by grinding or honing, to achieve the desired surface finish and tolerance requirements. For example, the exclusive "Kombifin-Stone finish option" offered by Hembrug enables surface finishes as fine as Ra 0.02µm.
Numerous Hembrug Mikroturn machines are used worldwide for the finishing of carbide forming tools. In a recent application, a 150 mm draw die with a 12% cobalt binder, Hembrug engineers were able to finish-turn this die with a rough cutting depth of 0.2 mm, achieving a total cycle time of 30 minutes. A CVD diamond insert was used, resulting in a tool life of up to 1.55 miles, but with a PCD tool, 2.48 miles was even achieved. The surface finish achieved was 0.2 micron Ra.
Authored by Danobat, Inc.
For more information contact:
Danobat, Inc.
4080 Winnetka Ave.
Rolling Meadows, IL 60008
847-250-6168
danobatinc@danobat.com
www.danobat.com