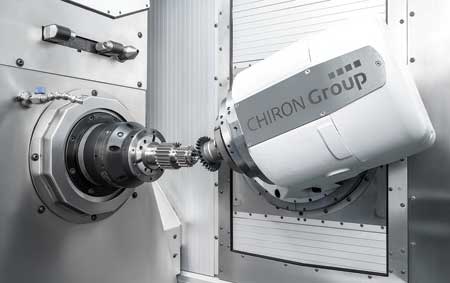
Milling-turning: Gear-cutting power skiving, newly integrated into the MT 715.
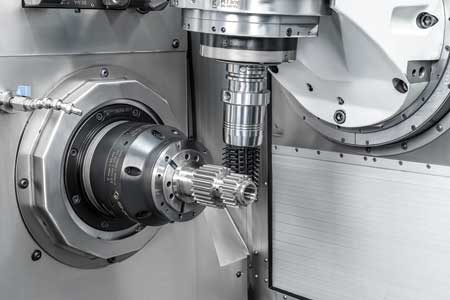
Hobbing: the most productive gear cutting technology but limited when it comes to internal gears and external without a permissible run-out area.
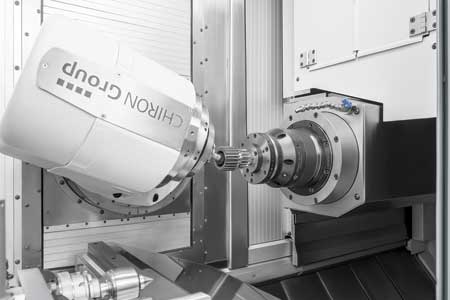
Internal skiving on the 6th side of the workpiece.
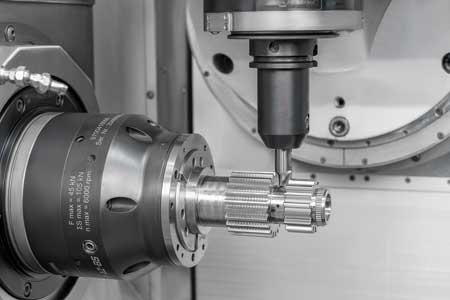
Deburring to finish complete machining processes at high precision.
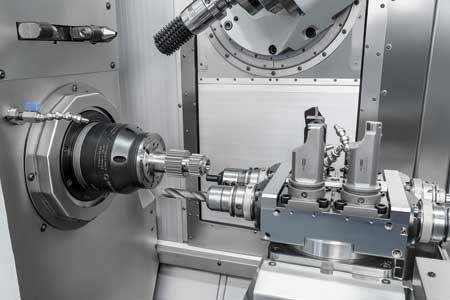
Tooth cutting completes the gear cutting technologies on MT 715.
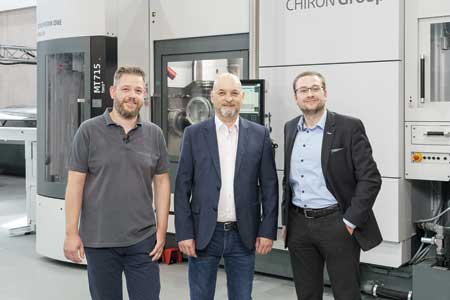
The gear team: Daniel Kopp, Application Engineer; Klaus Wichmann, Product Manager; Paul Horn; Michael Wurster, Senior Product Manager
In the early 2000s, manufacturing was changing. The industry was limited to specialized machines, each dedicated to a single job: milling, turning or drilling.
It was efficient, but there was a catch. Creating a complex part involved moving it from one machine to another. This process was slow, took a lot of time and often led to mistakes. A few visionary engineers looked at this process and thought, what if there was a better way?
One of those engineers was Michael Wurster, Senior Product Manager at CHIRON Group. Wurster had an idea: What if one machine could do everything? A machine that could mill, turn and drill all six sides of a part without ever needing to move it. This concept of an all-in-one machine was not only efficient, but it would change how parts were made. The CHIRON team took on the challenge, and soon, the first milling-turning machining centers were born. The success of these new machines quickly caught the industry's attention, but CHIRON's engineers were already looking for a new challenge: gear cutting.
Gears are essential components, but traditional gear-cutting techniques, like hobbing, had limitations and could not cut certain types of gears, especially internal gears or complex shapes without enough room for the tool to exit.
Wurster believed in gear skiving, a versatile and precise method that could shape both internal and external gears even those with unique, complex shapes.
The challenge was there, but Wurster and his team were convinced that integrating gear skiving into the MT series 715 could be the key to unlocking new possibilities for manufacturers giving a flexible solution for prototypes and large production runs.
This vision came to life in the CHIRON MT series 715, which incorporated gear skiving as its first gear-cutting technology. This addition aligned with the changing needs of the manufacturing world-responding to demands for smaller batch sizes, higher precision and faster production times.
The MT 715 opened new possibilities for manufacturers seeking a flexible solution for prototyping and series production. With its ability to handle gears up to a module of 3.5 mm and achieving a quality level of IT 7 or better, this machine proved to be the perfect fit for manufacturers across a range of industries in need of a single machine that could do it all.
Authored by CHIRON America, Inc.
For more information contact:
CHIRON America, Inc.
10950 Withers Cove Park Drive
Charlotte, NC 28278
704-587-9526
info.america@chiron-group.com
www.chiron-group.com/products/715-series