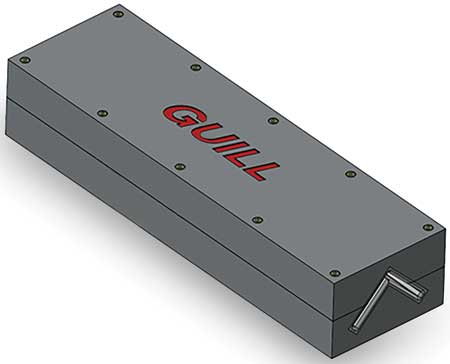
Typical pultrusion die now offered by Guill for this production process.
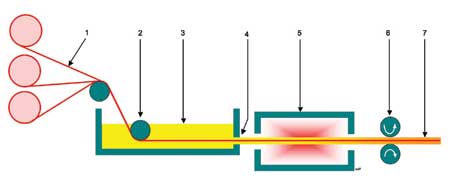
Diagram of the pultrusion process: (1) Continuous roll of reinforced fibers/woven fiber mat; (2) Tension roller; (3) Resin impregnator; (4) Resin soaked fiber; (5) Die and heat source; (6) Pull mechanism; (7) Finished hardened fiber reinforced polymer.
Guill has announced the expansion of its product portfolio to include custom-engineered pultrusion dies. This strategic move marks a significant advancement in providing comprehensive, high-quality tooling solutions for industries such as automotive, aerospace, construction, energy, marine, sporting goods and telecommunications, the company reported.
"As the demand for pultruded composites grows due to their strength, durability and lightweight properties, Guill is well-positioned to meet this need," said a company spokesperson. "Leveraging its expertise in extrusion tooling, Guill is now applying its precision engineering capabilities to develop innovative pultrusion dies tailored to the specific requirements of each target industry."
"We are excited to enter the pultrusion market with our advanced tooling solutions," said Peter Leary, Technical Sales Engineer at Guill. "Our extensive knowledge of extrusion processes and commitment to custom engineering enable us to design dies that not only meet, but exceed, our clients' expectations in terms of performance, efficiency and quality."
The Guill Tool Extrusion Division has a long history of designing and manufacturing tooling for various applications, including medical tubing, wire and cable coating, hose production and multilayer extrusions. Its capabilities include creating multilayer crossheads, in-line, reciprocating, rotary dies and a variety of other custom solutions supporting materials such as plastics, rubber and silicone.
Guill's new line of pultrusion dies is engineered for industries utilizing fiber-reinforced polymers (FRP) and are compatible with a range of polymer matrices, providing versatility and high performance across different applications.
Tom Baldock, Guill Sales Manager, said, "Pultrusion is a cost-effective process for producing parts with a constant cross section in high volumes, requiring relatively little labor. Fiber-reinforced polymer (FRP) pultruded composites are durable, corrosion-resistant and eco-friendly."
For more information contact:
Tom Baldock, Sales Manager, Extrusion
Guill Tool & Engineering
10 Pike Street
West Warwick, RI 02893
401-828-7600
tbaldock@guill.com
www.guill.com