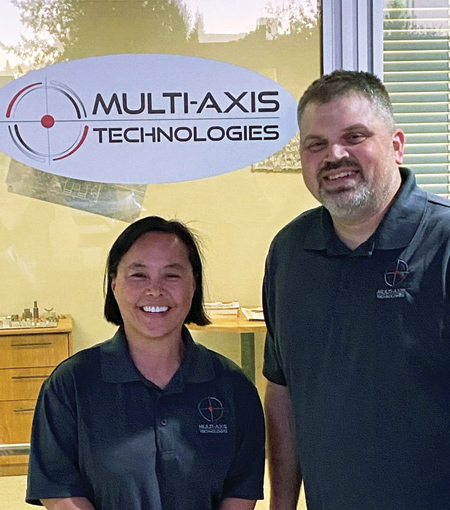
Daisy Kelly and Jay Simpson, co-owners of Multi-Axis Technologies
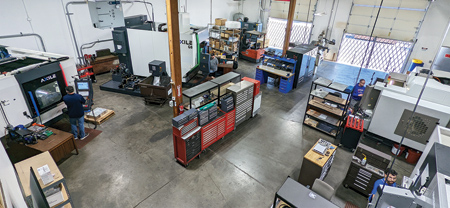
Multi-Axis Technologies in Kent, WA
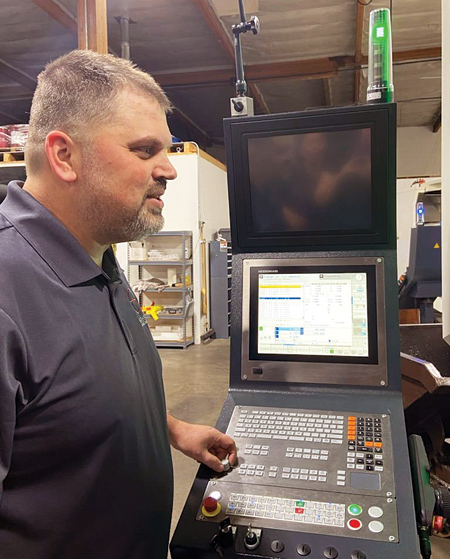
Jay Simpson taking the lead at a HEIDENHAIN TNC 640 control.
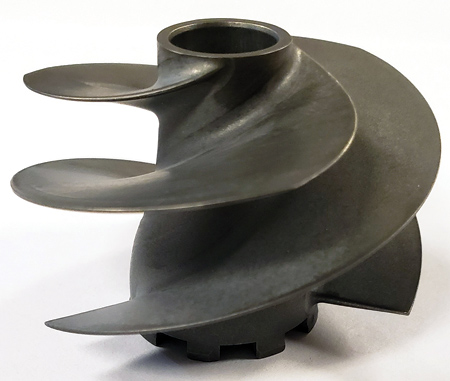
A three-blade inducer part made of titanium at Multi-Axis Technologies.
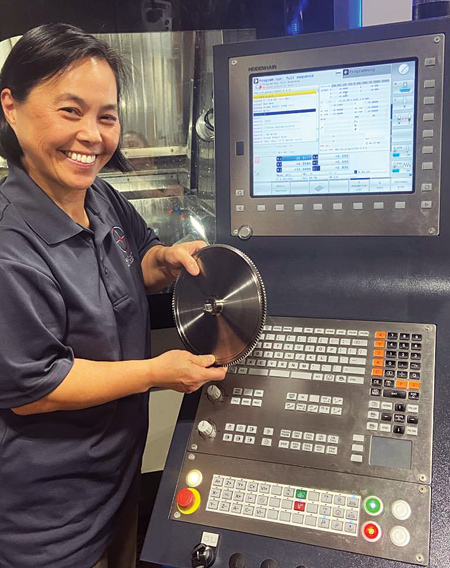
Daisy Kelly holding a part made at a machine tool controlled by a HEIDENHAIN TNC 640.
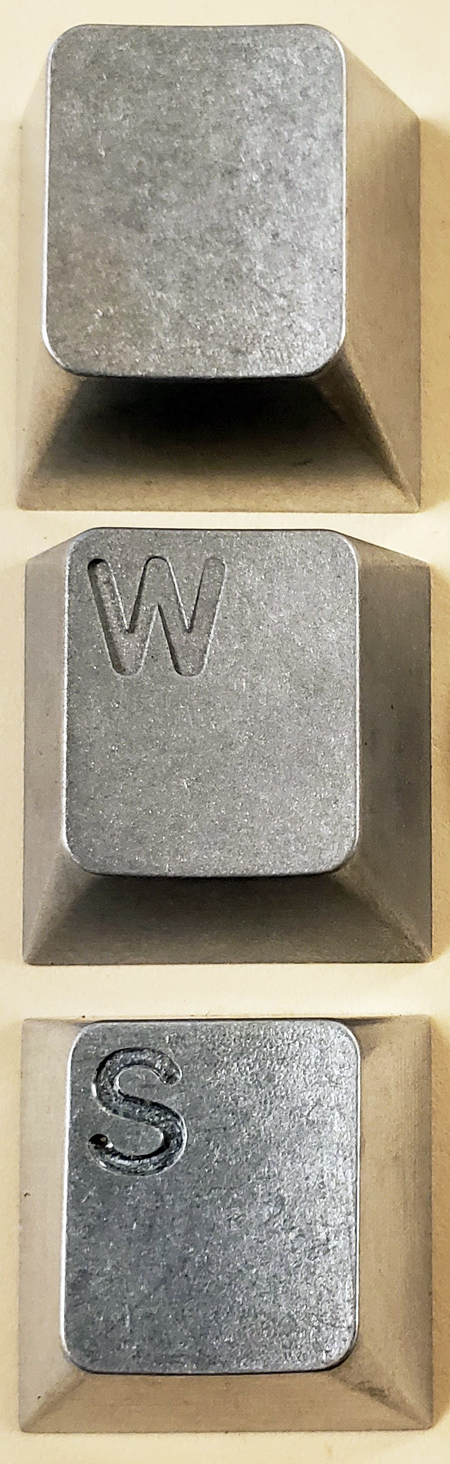
Examples of small parts made at Multi-Axis Technologies. These are small key caps for a laptop computer.
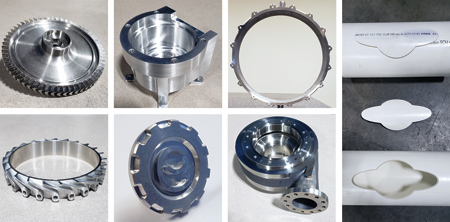
A sampling of parts machined at Multi-Axis Technologies. Anywhere from one to 10 parts are being made at Multi-Axis Technologies at any given time.
Two former Blue Origin employees saw an unmet need during the COVID pandemic shut down and stepped out in 2021 to support the community. Starting their own advanced machine shop in Kent, WA, they are now fulfilling the emergent needs of area manufacturers and heading skyward.
"We have a unique skillset and machining capabilities that includes 5-axis and more that allows us to do low-volume, high-mix parts in a flash," said co-owner Daisy Kelly, who handles company administration and more. "That is not something common around this area and the need was there."
Multi-Axis Technologies' customers include many in the aerospace industry who need turbo machinery parts for rocket engines, although they are quick to explain that they have been fascinated about the variety of unrelated groups coming to them for part development as well as for Design for Manufacturing (DFM) work. The owners cite a variety of commercial industry customers, including extraction vessels, abrasive cutting machines, gaming industry, hobbyists/homeowners and more.
Co-owners Kelly and Jay Simpson, former Blue Origin leaders, have combined their experience in the manufacturing industry and supply chain management to start this upward-trajectory machine shop. "With our machining capabilities, which include two 5-axis machines and more, we are able to specialize in rapid prototyping and part development for our customers," said Kelly.
Simpson, who handles the company's technical side, has made sure that all the CNC machine tools in their shop host HEIDENHAIN controls as he believes it gives them a competitive edge. As a working machinist, programmer, post developer and leader for over 28 years, Simpson said he has worked with all the major CNC types. He was responsible for the original development of the machine shop at Blue Origin, and over his 15 years there, built its shop from three machines to over 60 today, across multiple sites.
"A HEIDENHAIN control was not known in our area, so it was never in my initial plans while I worked at Blue," explained Simpson. "Then during the start of the COVID pandemic crisis, I acquired a much-needed machine at Blue Origin that came with a HEIDENHAIN TNC 640 control. Not only was I unfamiliar with how to use it, but outside training and support was limited because of the pandemic. I started playing around with the control and researched a lot on the internet to teach myself a whole different system. It was shockingly easy due to its intuitive control style. And in just a couple of weeks, I quickly began producing very intricate parts and started to realize how powerful it was. I knew when we decided to start Multi-Axis Technologies, the decision was simple: the machines we buy must have a HEIDENHAIN control."
Uncommon is Common Here
"We have many stories over the past year where we have met the needs of our customers that were unexpected," said Simpson. He cited one example at Multi-Axis Technologies of the development of a small batch of three-blade inducers made of titanium that he defined as micro/2" across. The process was all developed and produced on the 5-axis CNC machine controlled by a HEIDENHAIN TNC 640 and ran lights-out with a completed part in the morning. "The customer CEO could not believe how fast the part was completed and came to our shop personally to thank us for a quick turnaround," added Kelly, who also periodically operates the machines.
She cited another story of uncommon note. "On one unusually hot week here in Washington state, it was 89° outside, which made the shop about 99° as we do not have air conditioning. We were machining ± .0002 in. journals, which are very high accuracy parts, in a tight timeframe," Kelly said. "One of our employee's friends told him that there is no way we were going to be able to hold the tolerances needed to complete the job or without a discrepancy. The employee was able to inform him that not only did we absolutely hold the tolerances, but we did it five more times. And despite everything that could have gone wrong as the heat affects the machine, the material, cutting tools and even the staff, the team was able to pull together and get the job done right and on time. It was another proud moment for us."
Both Kelly and Simpson noted that the features and functions of the HEIDENHAIN TNC 640's motion control system with closed loop feedback and linear glass scales on their machine tools are a large contributor to much of their success. "These controls automatically adjust for conditions and allow us to keep working even in the toughest environments," Simpson added. "In all my years, I have never run machines that have been this accurate. It is giving us the competitive edge we need."
What Makes the Difference?
Simpson said that the ease of use in which their HEIDENHAIN-controlled machine produces some of their most intricate parts is helping in their agility to meet their customers' needs. Their part sizes range from a small key cap for a laptop to a 24" x 30" aerospace isogrid structural component. Part types vary and often include the use of hard to machine materials, such as Inconel 718, Monel and A286.
"I do not believe we would be as successful in machining some of the parts so readily without the TNCs because the control provides the ability to translate and read the data fast, allowing the machine to move accurately and fluidly," said Simpson. "The simplicity of program restarts is quicker than I have ever seen. There is no reconfiguring; with the push of a single button, it just starts where it left off. Other controls, even with their restart functions, do not do that. The high level of accuracy the control provides, along with a well-integrated machine tool, makes the difference. This enables a whole system controlled by the TNC to produce high accuracy parts quickly. In fact, it can move so fast, I often have to slow it down in order to watch."
Just Ask the Operators
At Multi-Axis Technologies, the importance of rapid set-ups cannot be understated since they are typically working on one to 10 parts at any one time. Nick Santos-Carter, a machinist with 20 years' experience, said, "One of the great features about the TNC 640 control is that you can fine-tune the rapid rates to any value while maintaining your feedrate. It is incredibly helpful with monitoring multiaxis movement, thus successfully proving out the program quickly." Santos-Carter has become acquainted with the HEIDEHNAIN TNC since joining Multi-Axis Technologies in February 2022 as an employee.
The controls' Tool Life Management system was another feature Santos-Carter cited as now making a difference by increasing productivity. "You can easily program tool inspection points and tell the control which tools to change out if one becomes dull, allowing us to run lights-out and reap the rewards of machining while unstaffed. It is an incredible offering that blows the competition out of the water."
Santos-Carter also added that editing tool numbers on the TNC-controlled machines is also much easier: "The TNC knows the length and radial offsets with a simple tool call, which eliminates the common codes for initiating cutter compensation," he said. "This makes changing tool numbers within a program much safer and will reduce the likelihood of crashes automatically."
Another machinist, Dmitri Dougherty, said, "Editing the programs is much easier using a TNC 640, and the probing cycles are much simpler to find and use than what I am used to. It is amazing how well these machines hold tight tolerances."
Within these machine tools, Multi-Axis Technologies has incorporated TS 740 touch probes from HEIDENHAIN that incorporate on-machine inspection and automated work presetting. "This type of probing process allows us to meet the critical dimensions repeatedly and consistently," Dougherty added.
Often, customers send high-value 3D printed parts to Multi-Axis Technologies to finish as well. "On those, we can very accurately measure and set work offsets to complete the task at hand quickly. Multi-Axis Technologies is really rising to the occasion," said Santos-Carter.
Multi-Axis Technologies' motto is "The Highest Standards Driven by Passion." Kelly said, "Our high standards drive us to be better people, help others achieve their goals for success and be creative problem solvers. There is no greater feeling than working with people who share the same passion. We are humble and excited to build an incredible partnership with customers, suppliers and the manufacturing community."
For more information contact:
Multi-Axis Technologies
1112 4th Ave. N
Kent, WA 98032
253-854-2881
www.multiaxistech.com
HEIDENHAIN Corporation
333 E State Parkway
Schaumburg, IL 60173-5337
847-490-1191
www.heidenhain.us