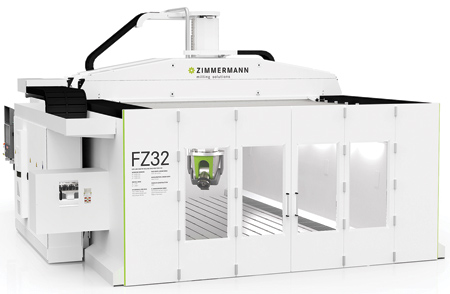
The new FZP32 5-axis portal milling machine is compact, flexible and accurate.
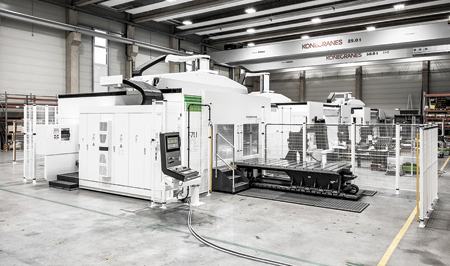
The machine can be equipped with automation-shown here with changeover slides on both sides.
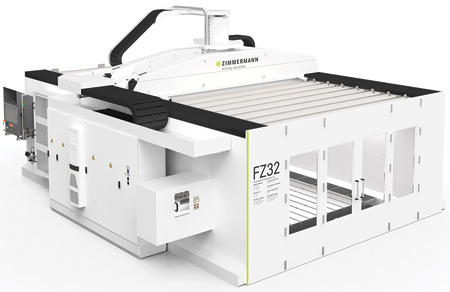
The developers have applied symmetry not only to the basic structure, but also to the complete machine concept.
"Model, tool and die makers must deliver perfect quality at competitive prices under increasing deadline pressure in order to prevail against strong global competition. Zimmermann is responding to this market condition with the newly developed FZP machine line," said a company spokesperson. "These 5-axis portal milling machines are customizable, space-saving and extremely thermostable. These features are ensured by the new thermosymmetrical design with a center-guided Z-slide."
Daniel Demlang, Zimmermann Technical Director, said, "Our customers are burdened by increasing cost pressure and the demand for ever higher quality, along with delivery deadline pressure for components. Reducing throughput times for workpieces was one of our main goals with the newly developed FZP series in terms of design. Stable process control and high machining quality are decisive factors for the cost-effectiveness of our systems. However, the customizability of our milling machines was not allowed to decline. Machines of the FZP Series are therefore even more flexible, in terms of set-up and design, with a comprehensive range of additional options."
Customizable Solution
Zimmermann placed particular emphasis on the customizability of the machines. Their structure can be varied in length and width with different vertical slides and gantries, thus adapting to a wide range of workpiece sizes. The lightest machine in the FZP line is the new FZP32 with an XYZ working range of up to 10 m x 4 m x 2.5 m (393" x 157" x 98"). The user can machine block materials, plastics, as well as CFRP, GFRP and aluminum, among other materials. Due to the large working area, it is also possible to mill components completely without reclamping.
"The modular design of the machine offers the possibility to consider different options. Automation solutions, such as a pallet changing system, a positionable rotary table, dust extraction bells and an individualized tool clamping system, are all possible," said Demlang.
Thermosymmetrically Constructed
The FZP line was designed for maximum dimensional accuracy during workpiece machining. This is because changing temperatures in the user's facility, as well as long machine running times, inevitably influence the machining quality. For this reason, the Zimmermann developers designed these new portal milling machines thermosymmetrically.
"The idea of the thermosymmetrical design is based on the fact that inevitable thermal influences can be absorbed to a considerable extent by the design of the machine structure," said Demlang.
In the portal milling machines of the FZP line, Zimmermann has arranged the milling spindle, guides and other accuracy-determining components in such a way that their heating is either absorbed or can expand in non-critical directions. The gantry's center-guided Z-slide in double-bridge design, for example, has an octagonal cross-section that makes it particularly stable. "With this design, we achieve very high thermosymmetric stability," said Demlang. "Comparable systems usually use complex cooling or software-based compensation for this purpose."
VH10: Milling Head with Extraction
The Zimmermann VH10 milling head is used on this new machine line. The fork head is designed in monoblock versions made of cast iron. It is compactly built, has only minimal interference contours, achieves high clamping forces and thus enables stable component machining.
Zimmermann optionally equips the VH10 milling head with process cooling via cooling lubricants and minimum quantity lubrication. To reduce throughput times, a spindle with 34 kW (45 HP) at a maximum speed of 24,000 RPM is used as standard in the milling head.
"We have now also equipped the VH10 with a dust extraction bell around the milling tool," Demlang said. "This makes it suitable for abrasive and harmful materials such as GRP or CFRP, which are used in aircraft construction. The dust extraction system captures the dust directly at the point of origin, which reduces contamination of the interior."
Flexibility by Design
Facility conditions are often a challenge for the installation of large milling machines. Free installation space is usually scarce and machine concepts must offer a high degree of flexibility in installation.
"The Zimmermann developers have applied symmetry not only to the basic structure of the gantry, but also to the complete machine concept. This allows the customer to individually determine specific connections or peripheral attachments. We can then simply position the peripherals as required by the individual situation without making any major design changes to the new FZP32," said Demlang. "Overall, the ratio of floor space to workspace has been optimized with this new development."
Zimmermann equips the new machine line with larger tool magazines or even pallet changers on request. This allows users to reduce non-productive time and make their production more automated. Another feature: "Milling-turning applications are increasing, especially in aircraft construction, for example in turbine production," said Demlang. "For this purpose, we also equip our milling machines with carousel rotary tables on request."
Regardless of the task the customer needs to perform, Zimmermann's experts can supply the machines in a customer-specific, optimized way with their modular plant construction kit (MAB).
For more information contact:
Zimmermann Inc.
30587 Century Drive
Wixom, MI 48393
248-305-9707
sales@zimmermann-inc.com
www.zimmermann-inc.com