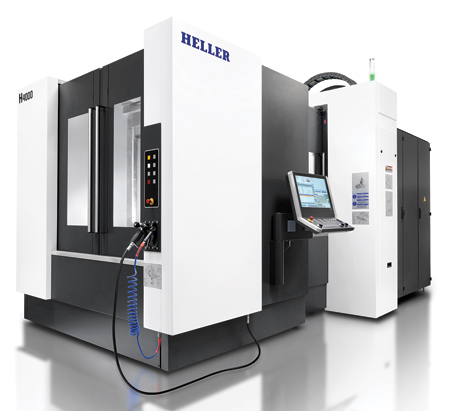
The new H series HMCs are available in sizes H 2000 (B01a), H 4000, H 5000 and H 6000 (B01b).
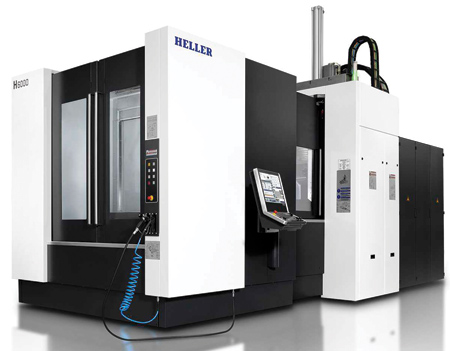
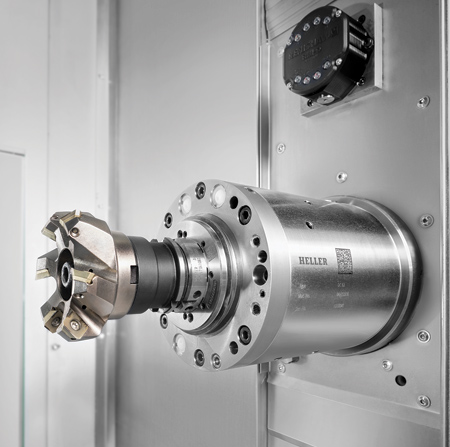
HELLER spindles for the Gen4 machines are available in the Power (PC) and Speed-Cutting (SC) and now also in a Dynamic-Cutting (DC) version. The latter provides the optimal combination of high torques and speeds.
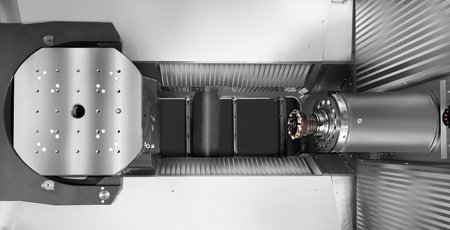
A newly developed rotary table structure with rigid bearings contributes to the high stability of the machines from the H series.
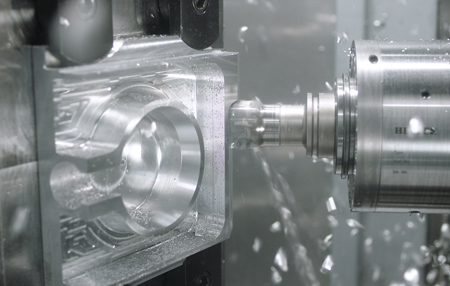
With its new Gen4 H series 4-axis machines, HELLER reduces idle times while increasing milling performance for the machining of aluminum (B06a) as well as steel (B06b).
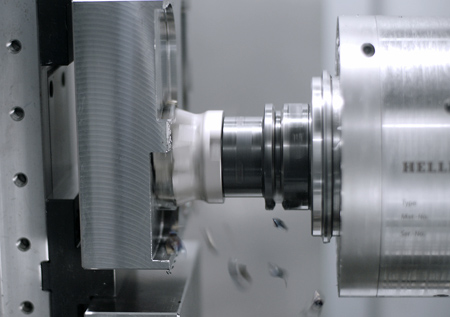
HELLER has launched the fourth generation of the H series. "The 4-axis horizontal machining centers (HMCs) offer numerous benefits over the previous generation and stand out even more from other machines in this segment due to their shorter idle times, increased milling performance, reduced service times and more flexible customization to customers' requirements," said a company spokesperson.
HELLER offers the H series in sizes H 2000, H 4000, H 5000 and H 6000, covering a stroke range from 630 mm to 1,000 mm, with the first two models for tools with HSK-A 63 and the larger ones with HSK-A 100.
Featuring a modular design and many standard components, users have a wide range of options to adapt the machine to their individual requirements. In terms of drive technology, there are essentially two equipment packages to choose from: Power and Speed. The Power package is designed for medium batch sizes and for the machining of steel and difficult-to-machine materials. The Speed package is suited for high-volume machining of cast iron, aluminum and other light metals.
"With the Speed equipment package for the Gen4 we have succeeded in reducing chip-to-chip times by an average of 10%," said Manuel Gerst, Head of Development. "One of the crucial factors is the short positioning times. In field tests, we were also able to demonstrate cycle time improvements of approximately 7%."
A new AutoSet technology cycle for weight-dependent dynamics adjustment of the Z-axis and B-axis is included in the Speed equipment package. The cycle helps to achieve optimum axis dynamics in direct correlation to the load capacity. Moreover, the developers optimized the tool change process in order to enable time savings for medium tool weights and reduced the spindle run-up times. Depending on spindle size, these vary between approx. 1.4 and 2.6 seconds.
Inline Spindle for Gen4
The in-house developed spindle for the Gen4 machines is available in three different versions: Power (PC), Speed (SC) and a new Dynamic Cutting (DC) version. All spindles are available with HSK-A 63 or HSK-A 100 toolholder. The DC units in particular offer an ideal combination of high torques and high speeds, with the DC 63 i version providing 16,000 RPM and 180 Nm and the DC 100 i option delivering 12,000 RPM and 400 Nm. "Users requiring even higher torques can still opt for our classic gear-driven spindles found on models H 5000 and H 6000, which are available with up to 2,292 Nm torque," said Gerst. "However, the high spindle power and the extreme axis dynamics alone are not sufficient to increase the machine's productivity in practical application. To achieve this, the machine also has to provide the necessary stability and a suitable damping behavior. Therefore, the classic machine design with a twin-drive in the Z-axis has been maintained and improved."
Options including a High-Accuracy package and U-axis further increase accuracy and surface finishes.
Potential temperature fluctuations can be compensated in a quick and easy way. With the touch of a few buttons, the AutoCal and AutoLin software features allow users to quickly adjust the axis geometry to the current conditions.
The integral U-axis of the HELLER out-facing head allows users to perform contour turning operations on components using motion tools. According to HELLER Head of Sales Fabian Mattes, the feature is a frequently requested option. He said: "In series production, it eliminates the otherwise necessary changeover to a turning machine, resulting in massive time, and thus cost savings."
Reduced Life-Cycle Costs
HELLER reduced life-cycle costs by lowering energy consumption of the new H series with speed-controlled pumps in the hydraulic unit and in the high-pressure portion of the coolant unit, smart switch-off strategies of energy consumers and the use of machine waste heat by optional water/water heat exchangers, along with other features.
Maintenance and service work can be performed faster due to good accessibility to all units. As an example, Mattes mentioned easy spindle replacement based on the HELLER zero-spindle system: "Our zero-spindles can be exchanged within about an hour since only the mechanical parts have to be replaced. The motor remains inside. As a result, our customers are able to save approximately 30% of running costs throughout the life cycle of a spindle compared to classic motor spindles."
Improved Ergonomics
The main operating unit in panel design with double pivot arm is installed next to the work area door equipped with a large vision panel. This allows the operator to keep an eye on both the screen and the work area. Another useful feature when running in processes is the WorkCam work area camera. It allows the user to monitor processes throughout the entire work area on the 24" screen. Multi-touch technology as well as additional hard keys and three potentiometers for the regulation of speed, feed and rapid traverse provide increased operational convenience and simplify set-up and operation of the machine.
A compact, touch-sensitive operating panel comprising key functions, a low loading sill, short overhangs and the possibility of overhead loading make work at the workpiece setting station easier. Integrated LED lighting at the setting stations and inside the work area are standard.
HELLER4Industry
A range of Industry 4.0 features is available from HELLER under the product name HELLER4Industry. All these HELLER4Industry features can be visualized directly at the machine, in the company network or online.
Connectivity to MES and ERP systems has been expanded by OPC UA-based communication with the help of "umati," simplifying the integration into the company network. Users who also use the HELLER Services Interface (HSI) option are provided secure access to their production and maintenance data from any location in the form of a browser-based solution.
For more information contact:
HELLER Machine Tools
1225 Equity Drive
Troy, MI 48084
248-658-6600
www.heller-us.com