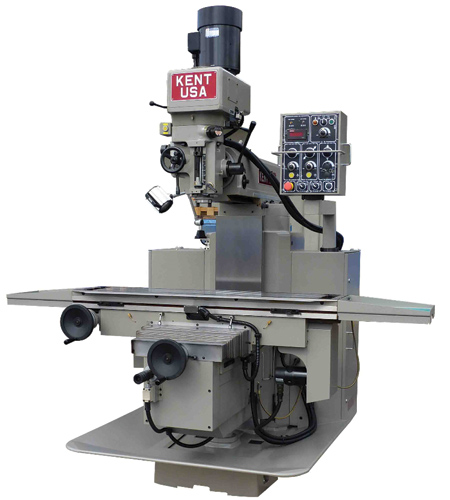
The KTM-5AVKF from Kent Industrial USA
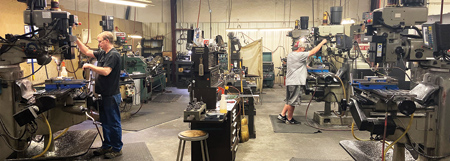
Progressive Machining of Greenville has used Kent USA equipment for years. Its most recent purchase was a KTM-5VKF CNC knee mill.
"Despite the widespread adoption of CNC machine tools over the past few decades, some shops remain on the fence, preferring manual equipment instead," said a Kent Industrial USA spokesperson. "The reasons for this vary, but the most valid of them is that production quantities do not support the significantly larger investment in tooling, education and especially the machine tool itself. And while one might argue that a CNC lathe or machining center equipped with quick-change tooling and supported by offline presetting and CAM programming systems can actually compete quite effectively on 'onesie-twosie' work, reaching that bar admittedly takes substantial effort."
Identifying Constraints
The challenges of managing an all-manual machine shop, however, are twofold. The first is capability. Machining relatively simple shafts and brackets is a no-brainer on a manual machine, but what happens when the customer's part designs grow more complex? What about 3D surfaces, non-orthogonal geometries, engraving and large or deep pockets, where the ability to remove massive amounts of material quickly and accurately is the difference between profit and loss?
The second is flexibility. While a seasoned machinist can bust out prototypes and handfuls of parts as quickly as the average CNC, the scales begin to tip as quantities rise. Are you going to turn away the work when prototypes move into production? This last statement brings up another objection to the purely manual approach, and that is the seasoned machinist needed to operate knee mills and engine lathes. Where does a shop owner or production manager find such people?
None of this is surprising to anyone who has spent a few years on the shop floor. What might come as a surprise, though, is that there is a viable alternative to the either/or of manual and CNC machinery. Some refer to them as half-CNCs, CNC knee mills or teach-style lathes. Whatever you call them, they represent a middle ground between the all-in of CNC and the limited-and-I-know-it of manual machines, one that shops can use to produce a wider range of parts and production quantities without the daunting investment.
Progressive Thinking
Andrew Ruedinger can speak to the value of these machines. He and his sister Patti are the co-owners of Progressive Machining of Greenville, Inc., having taken over from their father Doug, who founded this job shop in Greenville, SC, 33 years ago. Today the shop employs a dozen or so "extremely talented crew of guys," produces "a mix of difficult parts, in everything from stainless steel to just about any kind of plastic you can imagine," and has a mix of manual, CNC and half-CNC equipment.
The company has used Kent USA equipment for most of that time. Its most recent is a KTM-5VKF CNC knee mill, purchased in 2017 from long-time friend and machinery dealer John T. Simms at Machine Tools Inc., who Ruedinger said first introduced him to the brand 25 years ago and has provided excellent support ever since.
"We have the same problem as a lot of shops," he said. "It is tough to break into one of the CNC machining centers to make one or two parts, but not everything we do can be machined on a knee mill. The KTMs offer a nice mix. You can take a heavy cut and it does not bother them. We also do a lot of really close tolerance work, and there is not always time for grinding. I need equipment that can handle whatever you throw at it. These machines last. We do not beat our machines up, but they are used every day, and I cannot afford any downtime. That is the main thing. If someone asks me what knee mill to buy, CNC or otherwise, I tell them to buy a Kent USA. They are good machines, and they have treated me well."
Features of the KTM-5AVKF:
- 13" x 59" hardened and ground table top
- Saddle and knee with hardened and ground square (box) ways
- Oversized precision ballscrews in X and Y axes, telescoping cover on front cross way
- X and Y axes driven by DC servo motor
- Precision bored and ground milling head, with super precision ABEC-7 bearing
- Meehanite casting, with built in coolant reservoir in machine base
- Coolant system and chip tray
- Centralized automatic lubrication, with metered check-valves
- Table size: 13" x 59"
- Table travel (X-axis): 39.37"
- Saddle travel (Y-axis): 20"
- Knee travel (Z-axis): 20"
- Spindle motor: 5 HP
- Spindle speed: 70 RPM to 4,500 RPM
- Max. work load (center): 1,200 lbs.
Standard accessories:
- Quick change tooling package (Mach-1)
- Digital readout system
- NMTB-30 spindle
- Flood coolant system (built-in base)
- Knee (Z-axis) power feed
- Air power drawbar
- Flood coolant system
- Chip tray
- 3D edge finder
- Knee linear encoder feedback for coupled Z-axis position
- AMI with programmable M-functions.
For more information contact:
Progressive Machining of Greenville
14A Oakvale Road
Greenville, SC 29611
864-277-3900
www.progressivemachining.com
Kent Industrial USA
1231 Edinger Ave.
Tustin, CA 92780
800-KENT-USA / 714-258-8526
sales@kentusa.com
www.kentusa.com