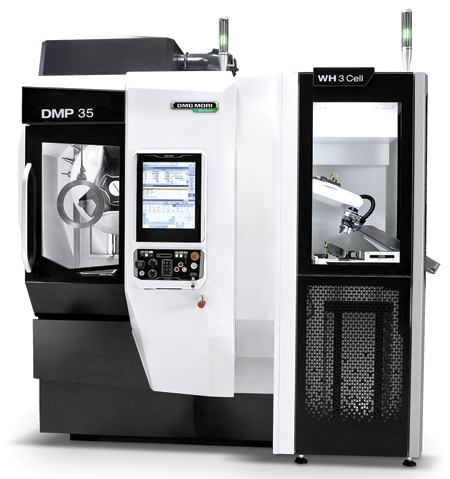
With a footprint of 3.15 sq. m and a minimum dismantling height of 2,090 mm, the DMP 35 makes optimum use of even tight production areas.
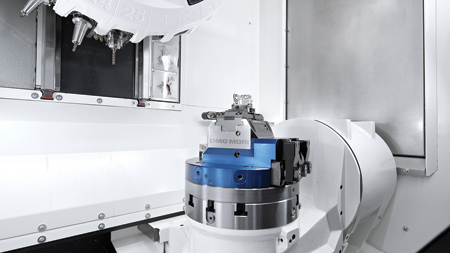
The DMP 35 includes an inline spindle with 15,000 RPM, direct absolute path measuring systems in all axes and the tool magazine with 15 places for tools up to 150 mm long.
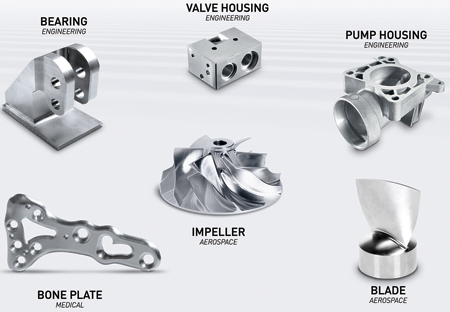
The DMP 35 allows efficient and precise production of complex workpieces made of a wide range of materials from aluminum to titanium.
DMG MORI has announced the DMP 35, a high-speed, compact machining center. It is based on the DMP 70 and enables the production of complex workpieces from a wide range of materials including aluminum and titanium. With a footprint of 3.15 sq. m and a minimum dismantling height of 2,280 mm, the DMP 35 makes optimum use of even tightly dimensioned production areas.
"In particular, users in competitive industries such as manufacturing and medical technology benefit from the added spatial value of the DMP 35," said Fabian Suckert, Managing Director of DECKEL MAHO Seebach.
Traverse paths are 350 mm x 420 mm x 380 mm with a width of only 1,285 mm. DMG MORI has equipped the DMP 35 in the standard version with an inline 15,000 RPM spindle, direct absolute path measuring systems in all axes and a tool magazine with 15 places for tools up to 150 mm long. Optionally, 25 tool places are possible, which only marginally increases the width of the DMP 35 to 1,410 mm. The modular system also includes a spindle with 24,000 RPM and an HSK-A40 or SK 30 interface.
The DMP 35 with an integrated table for 5-axis simultaneous machining is also available. The stable design of the compact machining center offers vibration-free and accurate milling in applications with high quality requirements with free chip fall. DMG MORI also offers an internal coolant supply with 40 bar and a chip conveyor with a capacity of up to 1,000 cu. cm/min. This and the internal doors help ensure high process reliability in production.
With only 1.15 sq. m of additional floor space, the WH 3 on the DMP 35 is the most compact automation solution from DMG MORI. The DMP 35 autonomously produces fully automated components with short changeover times with high quality.
With the new input programming on the WH 3, the set-up process can be simplified and shortened. In this way, even inexperienced programmers can set up components quickly and easily.
For more information contact:
DMG MORI - Americas Headquarters
2400 Huntington Blvd.
Hoffman Estates, IL 60192
847-593-5400
Service Hotline:
855-DMG-MORI (364-6674)
us.dmgmori.com