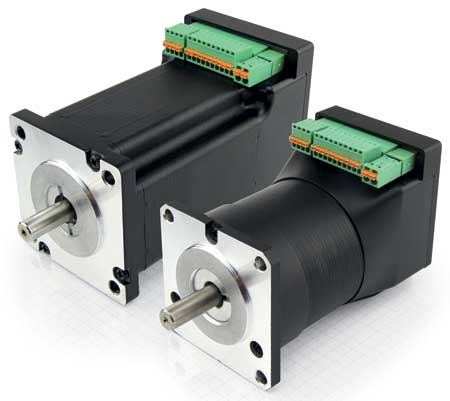
New Plug & Drive motors PD4-C and PD4-CB from Nanotec.
Specifically designed for applications that require high performance and efficiency, Nanotec Electronic has reported that its new generation of Plug & Drive motors feature precise positioning control, do not exhibit step losses and are controlled via the encoder in a load-dependent manner. Because both the motor controller and the encoder with 4,096 increments are already built in, cabling is limited to the communication connection and power supply.
The motors of sizes 56 and 60 mm (Nema 23 and 24) are available as low pole count (BLDC) and high pole count (stepper motor) versions. Due to field-oriented control, the stepper motors also act as a DC servo with a nominal speed of less than 1,000 RPM but a torque of up to 3.5 Nm. According to the company, the low pole count motors best demonstrate their power in dynamic applications, achieving a nominal speed of 3,500 RPM and an output of 135 W.
The integrated controller is offered in two versions to suit a variety of applications. In the stand-alone version with a USB connection, the motors are actuated either via the clock-direction or by a set value that is specified on the analog input. In the CANopen version, they are actuated via the field bus as per the CiA 402 standard.
Both actuation versions are compatible with application programs that are directly executed in the motor controller. Programs created in the C++ based programming language NanoJ are executed in the motor controller as machine code. They are synchronized with the digital inputs and outputs via the real-time operating system in 1-ms cycles and with the instructions received via the field bus. Thus, in the stand-alone version, it is possible to program applications such as format adjustments or valve controllers that can only be actuated via the inputs and do not possess any form of higher level intelligence.
In the CAN version, NanoJ can also be used to process inputs directly in the motor or to control certain procedures autonomously to increase response speed or reduce bus load.
The new Plug & Drive motors are best suited for multi-axis applications, positioning tasks with load changes, winding applications, dosing pumps and filler systems, semi-conductor mounting, wafer production, textile machines, and testing and inspection systems.
For more information contact:
Stephan Huber, CEO
Nanotec Electronic, U.S. Inc.
98 Sheridan Ave.
Medford, MA 02155
781-219-3343
info@us.nanotec.com
www.us.nanotec.com