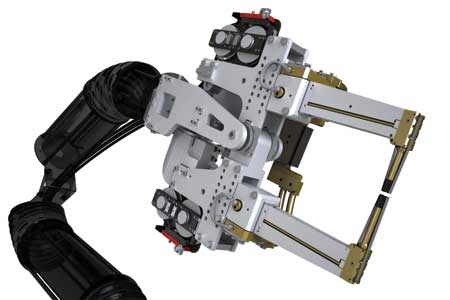
A new generation of pincer-guns has been designed for deployment in large-scale production.
Working closely with users from the automobile industry, welding technology supplier Fronius International has updated the pincer guns used in its resistance spot-welding process DeltaSpot. "Now available, this second generation of pincer-gun is designed to improve both the serviceability and the technology of the system, leading to shorter production downtimes and to lower operating costs, allowing light-alloy sheets to be joined more economically and with consistent quality," said a company spokesperson.
The core elements of the second generation of pincer-gun are its reshaped carrier body and the fundamental redesign of the pincer-gun arms and drive motors. Unlike in the previous generation, where the process-tape reeling and unreeling devices, the arm adjustment mechanism and the servo-electric main drive were all integrated within the pincer gun, these components are now located directly on the carrier body. "By 'decoupling' the components in this way, the Fronius engineers have made the construction of the pincer-gun arms both simpler and stronger, which is an absolute must in aluminum spot-welding. Even in the standard version, the pincer guns now come with a powerful MFDC transformer that runs at 1,000 Hz. Another result of this is that the system readjusts once every millisecond during welding, in order to achieve perfect results. The transformer and the rectifiers have also been moved closer to the electrodes so as to reduce transmission losses," said a company spokesperson.
As part of the overhaul given to the mechanical design, Fronius also restructured the interface between the carrier body and the pincer-gun arms to make it more modular. According to the company, this means that far less design work and equipment are needed when the pincer gun has to be individually adapted to a particular welding task. It also provides greater flexibility regarding the pincer-gun geometry and the "window" between the arms. The new pincer guns are much quicker to maintain and service, as assemblies such as the transformer, the motor control box, the tape drives and the main drive now feature high-quality plug in connectors and can be changed in just a few simple steps when needed.
"Fronius have also designed it to be easier to replace the process tape, with no change in the principle underlying the welding process itself: in this, a specially coated metal tape is guided between each of the electrodes and the weldpiece, protecting the surface of the electrode from soiling. It moves on to the next position after every weld-spot and the electrode contact surface always remains clean, with the same situation ensured for every single weld-spot. This is designed to lower soiling of the electrodes and to ensure consistent quality weld-spots, up to 10,000 times per tape, with no need to clean the electrodes using complicated electrode milling cutters," said the spokesperson.
According to the company, the process-tape mechanism has been overhauled on the basis of insights gained from the first generation of DeltaSpot machines. The tape feed has been redesigned for greater robustness and the reeling and unreeling device has been amalgamated into a single compact unit. As well as the standard 12 mm wide process tapes, it is now also possible to use optional 16 mm wide versions. This new feature broadens DeltaSpot's range of application still further.
The drives of the new generation of pincer-gun are also equipped with a fail-safe brake. One of the advantages of this for the system operator is that the time-consuming reference cycle is no longer necessary after an automatic pincer-gun changeover, meaning that production can be restarted more quickly.
For more information contact:
Fronius International
6797 Fronius Drive
Portage, IN 46368
877-376-6487
www.fronius.com