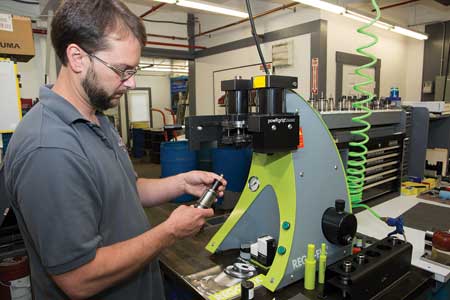
Tony Chastenay, All Axis R&D Owner and Operator. All Axis' REGO-FIX powRgrip push-button automatic unit loads/unloads tools in less than 10 seconds. The unit accommodates five different powRgrip collet sizes.
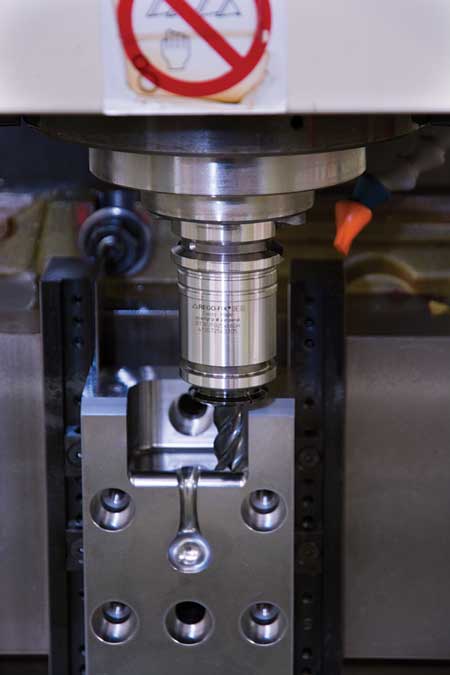
"Accuracy and speed go hand in hand," said Chastenay. "The more I use the REGO-FIX holders, the more I realize that they help us run a little faster and feed a bit harder."
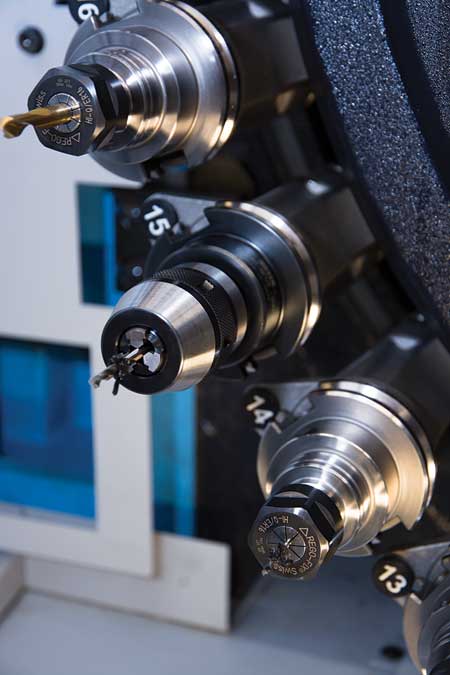
"We run REGO-FIX tooling because it is quicker than heat shrink and extremely precise," said Chastenay. "Plus, we can save hours of set-up time on just one tool. That is significant when a job may require as many as 30 tools."
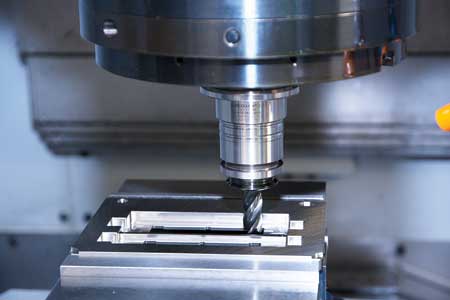
All Axis R&D machines between 300 and 500 new part numbers annually. Typical lot sizes range from single-digit runs to perhaps 100 pieces, and the parts routinely require tolerances of +/- 0.0001" and surface finishes of 8 Ra or better.
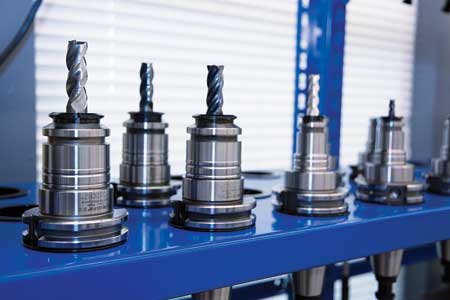
The powRgrip tooling involves no heating and is ready for immediate use after the cutting tool has been clamped into place.
All Axis R&D, a three-man prototyping, pilot production and engineering shop in Claremont, NH, machines between 300 and 500 new part numbers annually. Typical lot sizes range from single-digit runs to perhaps 100 pieces, and the parts routinely require tolerances of +/- 0.0001" and surface finishes of 8 Ra or better. In addition, the shop also provides customers with manufacturing process engineering assistance. The shop's heavy and varied workload magnified the need for efficiency.
"One of our goals is to manufacture parts in as few operations as possible," said Tony Chastenay, All Axis R&D Owner and Operator. "To increase part quality and accuracy, we try to machine parts on multiple axes so we can complete them in one or two set-ups. At the same time, we work to minimize spindle downtime associated with tool set-up and adjustments."
Getting a tool set up to run correctly can consume a considerable amount of time, according to Chastenay. "Quite often when an endmill exhibits runout or produces a tapered cut, it is not the endmill, it is the way its being held," he explained.
Earlier in the shop's history, Chastenay said that they would typically have to put an indicator on an endmill and move it around in the holder to dial it in and achieve concentricity. "Sometimes this process took 20 minutes, sometimes an hour. In any event, it wasted a lot of time," he said.
"REGO-FIX powRgrip tooling helps eliminate that downtime," said Chastenay. "The system is a hydraulically actuated press-fit tool clamping - one that provides TIR of less than 3 microns. Unlike heat-shrink toolholders, the powRgrip tooling involves no heating and is ready for immediate use after the cutting tool has been clamped into place."
Clamping and unclamping tools into powRgrip holders is accomplished with a hydraulic hand pump or, as in All Axis' case, a push-button automatic unit that loads/unloads tools in less than 10 seconds. The unit accommodates five different powRgrip collet sizes.
"With the REGO-FIX holders, as long as I put in a quality endmill that meets the REGO-FIX tolerance on the shank, the tool runs beautifully and without any taper," said Chastenay.
Because it is a premium toolholding system, powRgrip tooling costs a little more than generic toolholders. However, Chastenay gathered payback data via tool tests before purchasing the system and realized the tooling was well worth the investment. "Small company or not," he said, "I felt I could handle the investment because my payback was less than a year and the benefits far outweighed the monetary cost. You can buy a side lock holder for $80, but if you spend two hours trying to get that tool to run correctly, you just lost two hours of spindle time. Our shop rate is $70/hour, so with the $80 holder, I just really spent $200-plus the first time it gives us problems. We run REGO-FIX tooling because it is quicker than heat shrink and extremely precise. Plus, we can save hours of set-up time on just one tool. That is significant when a job may require as many as 30 tools."
Use of the holders also boosts tool life at the shop, explained Chastenay. Only a few thousandths runout encountered with a traditional side lock holder will cause uneven cutting action that can wear one flute out before the others. The truer a holder runs, the more it improves tool life and the better the resulting part accuracies and surface finishes. It also allows for higher cutting speeds.
"Accuracy and speed go hand in hand," said Chastenay. "The more I use the REGO-FIX holders, the more I realize that they help us run a little faster and feed a bit harder. For some of our parts with hour-long cycle times, for instance, we have been able to cut 10 to 15% off of those just by the increased speeds and feeds. The tooling has definitely provided a boost in productivity and helped us stay more competitive and win more jobs."
All Axis adapts its services to meet specific customer needs. "We are not simply a parts machining business," said Chastenay. "We are involved in our customers' design processes and how the part fits into their manufacturing environment. We give them feedback to help them get the part cost down to sell their product competitively. We take pride in the quality work we offer and are competitive on price while maintaining a personal, in-depth approach."
Illustrating the shop's pride and competitiveness, All Axis rarely turns down jobs. And according to Chastenay, it has a reputation for taking the tough or strange jobs that other shops are hesitant to accept.
All Axis machines a wide range of materials from standard aluminums, stainless steels and tool steels to engineering plastics like Delrin and PEEK, and even graphite. "Not a lot of shops like to machine graphite, but one of our biggest graphite parts is actually a carbon base for a fixture," said Chastenay.
Chastenay founded All Axis in 2008, working after hours at his home with a manual milling machine while he managed an OEM manufacturer's prototyping and model shop during the day. The model shop was basically an R&D facility that provided plenty of time to explore different workholding and toolholding. The jobshop environment at All Axis does not afford that luxury.
At All Axis, operating multiple machines in a two-man shop is a deliberate strategy. "Having more machining stations does help me react to my customers' needs," Chastenay said, "because I can route more work to certain ones and leave some open to handle emergency work. It is a dynamic process." The company has four vertical CNC machining centers, a CNC turning center, CAD/CAM software and CMM capabilities, as well as welding, fabricating and assembly equipment.
Its variety of machines also helps the shop accommodate work of different scales. "We do some tiny micro stuff, such as parts that are 0.125 inch in diameter or smaller, and machine some very small micro features with endmills around 0.005 inch in diameter," he said. At the larger end of the spectrum, the shop uses endmills up to 1" in diameter, and one of its VMCs will handle plates up to 36" x 20".
"All Axis is busy because we have a strong contact list," said Chastenay. "Most of our work has been from that list over the years. We focus on having a network of customers and acquire new jobs basically by word of mouth."
The shop serves customers in the electronics, aerospace and firearms industries, among others. However, the shop is seeking to diversify its customer base to include perhaps medical or alternative energy customers. Business growth and additional staff, Chastenay foresees, will let him continue to live his dream, but perhaps on a less hectic basis.
As All Axis grows, he plans to further update the shop's equipment to ensure its strength and competitiveness. In fact, he is already considering the addition of 5-axis machining capability. And when that happens, he said the machine is going to run REGO-FIX powRgrip tooling.
For more information contact:
REGO-FIX Tool Corp.
7752 Moller Rd.
Indianapolis, IN 46268
800-REGO-FIX (800-734-6349)
info@rego-fix.com
www.rego-fix.com
Tony Chastenay
All Axis Research And Development LLC
13 Bowen Street
Claremont, NH 03743
603-477-8656
tchastenayallaxis@gmail.com