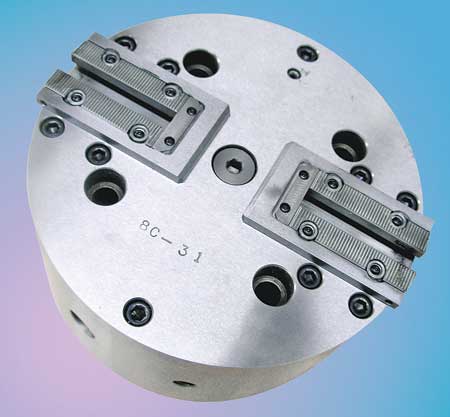
Before deciding whether to repair, recondition or replace a defective chuck, companies can contact Royal Machine & Tool for suggestions. It may be recommended to have the chuck forwarded to the factory, where the company provides a free evaluation and proposal.

After evaluating the defective original chuck, reconditioning was recommended to provide new chuck standards, a one-year warranty (the same as a new chuck) and a cost advantage of 60% or less of the cost of a new chuck.
The decision to repair, recondition or replace a chuck must be made on the results one intends to achieve. Obviously, safety considerations are first and foremost. Additionally, does the chuck have to operate for a short period of time or for a long period of trouble-free use? Also, does the cost difference affect the decision?
Next, consider the four specific reasons for repairing, reconditioning or replacing chucks:
- Does the chuck appear to be worn?
- Has an accident broken something in the chuck?
- Has the chuck begun to lose its gripping force or its accuracy?
- Is the chuck design incapable of holding a part specifically designed to meet the part's process and tolerances?
If the answer to any of these questions is yes, then the three Rs - repairing, reconditioning or replacing - should be considered.
Repairing
Usually, this is the least expensive service. If the chuck were in an accident with a broken master jaw or a broken wedge, then replacing the broken part and cleaning up some damaged surfaces can make the chuck serviceable at little expense. The exception to this service is if the broken part is a special part, in which case it may have to be reverse engineered and manufactured. Repairing provides a serviceable chuck returned to its original condition prior to breaking. However, this leaves a chuck with a warranty only on the replaced parts and workmanship. Also, replacement parts may not have the same fit with worn parts and may not provide the best results for holding the part.
Reconditioning
This is the midrange of expense. A correctly maintained and lubricated chuck will usually age gracefully and will only show wear by loss of accuracy and/or gripping force. When all the major wear surfaces are worn and require rebuilding of one form or another, it is time to send it in for evaluation. Reconditioning is recommended if the cost of reconditioning is 60% or less of the price of purchasing a new chuck.
Chrome plating forms are used for building up slightly worn surfaces, and welding is used for badly worn surfaces. After the worn surfaces are built up and the parts are checked for cracks, the new surfaces are ground to new chuck tolerances. Master jaws are also qualified to new chuck tolerances. A reconditioned chuck usually has a one-year warranty (the same as a new chuck), and for most situations are as good as a new chuck.
Once the original chuck has been reconditioned to new chuck standards, the one negative is that the chuck will retain any problems and/or deficiencies inherent to the old design. Any desired changes usually require replacement.
Replacing
Sometimes the cost of reconditioning exceeds 60% of the cost of a new chuck, or it is simply time to update and replace with a new design. The new chuck in sizes up to 84" will have all the advantages of the latest designs and materials. Many times operations will have changed and require redesigns to improve performance. In addition to receiving a full one-year factory warranty, possible considerations for selecting new chucks are the ability to operate chucks at a higher RPM, additional travel in master jaw strokes and the ability to mount locators on chuck facings. Other special features that may require new chucks are options such as part sensing, chip blasting and automation.
The final decision must be based on what is functionally and financially best for the situation.
Authored by John Darling, Chief Application Engineer, Royal Machine & Tool Corp.
For more information contact:
Bernie McAloon, Sales Manager
Royal Machine & Tool Corp.
P.O. Box Y
4 Willow Brook Drive
Berlin, CT 06037
860-828-6555
royal@royalworkholding.com
www.royalworkholding.com