

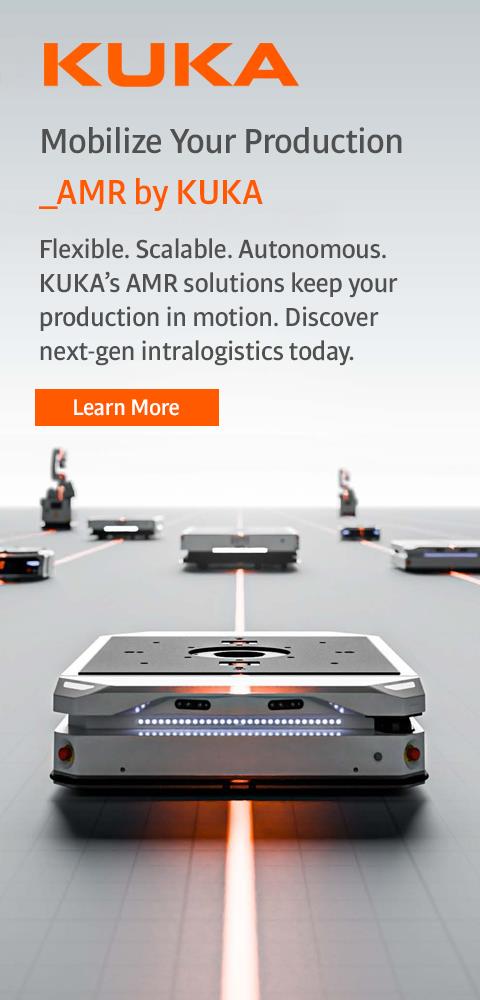
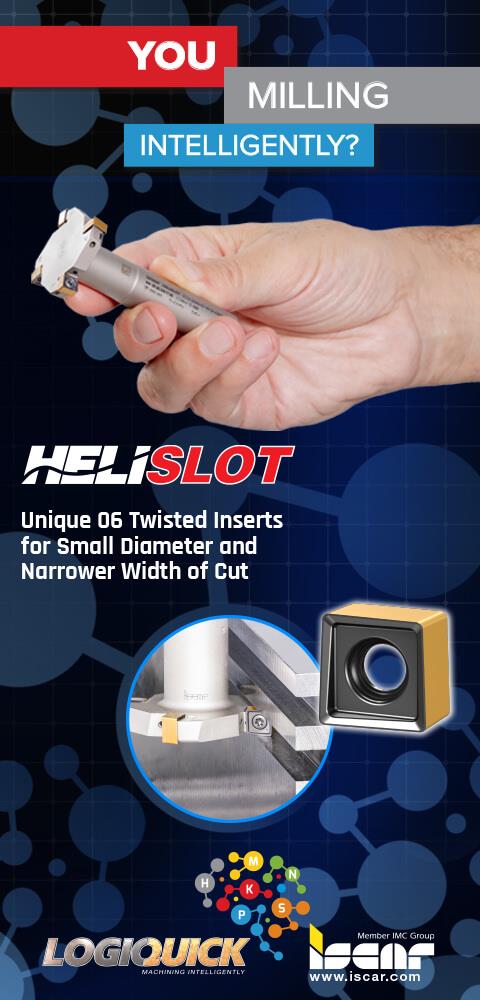
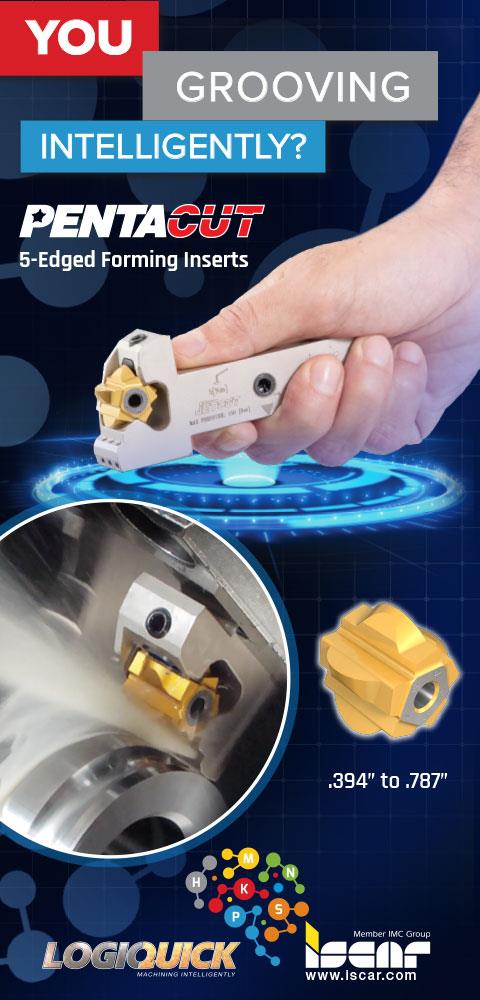
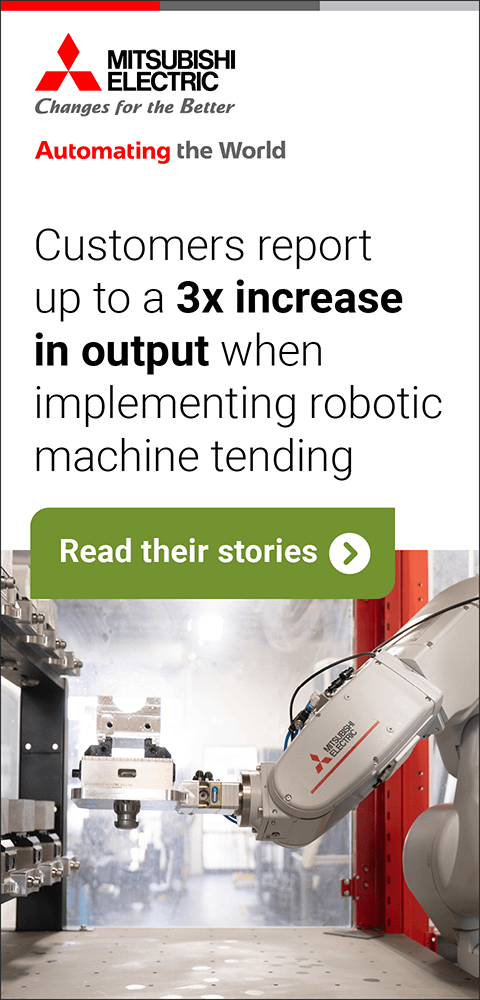
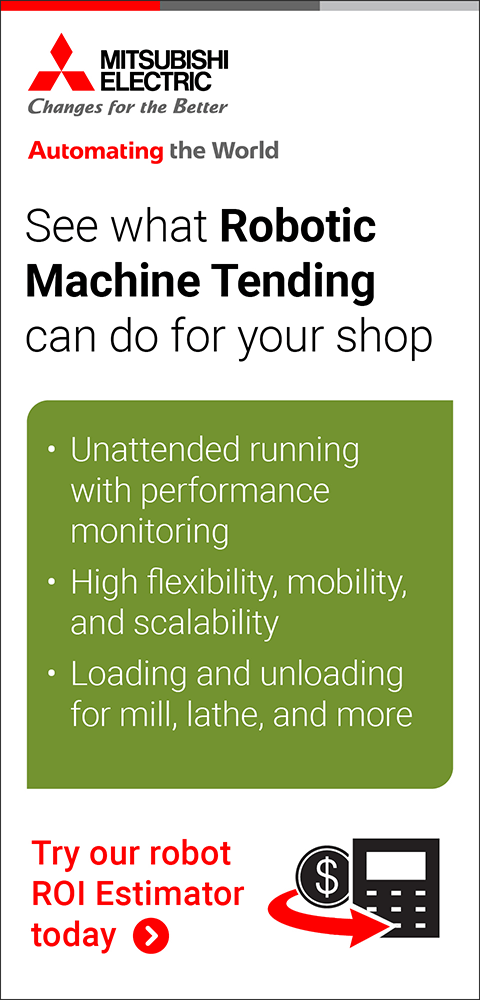
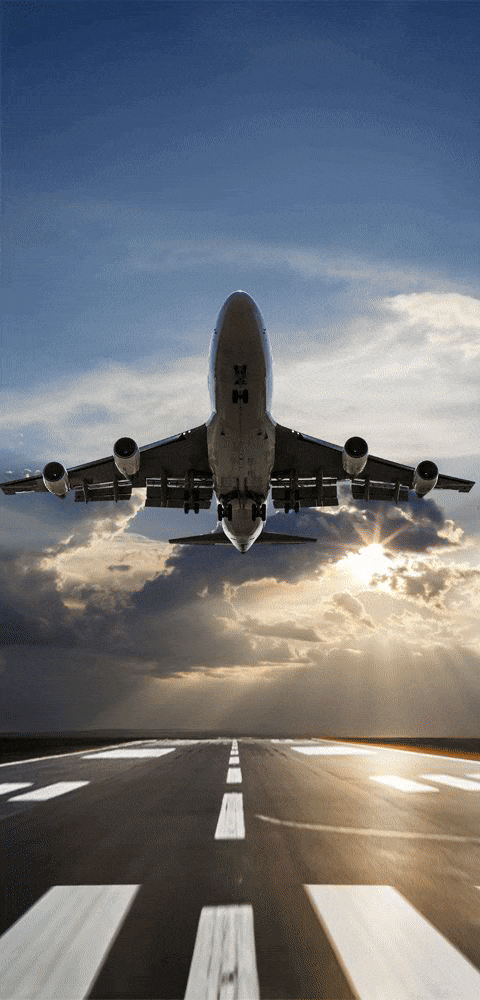
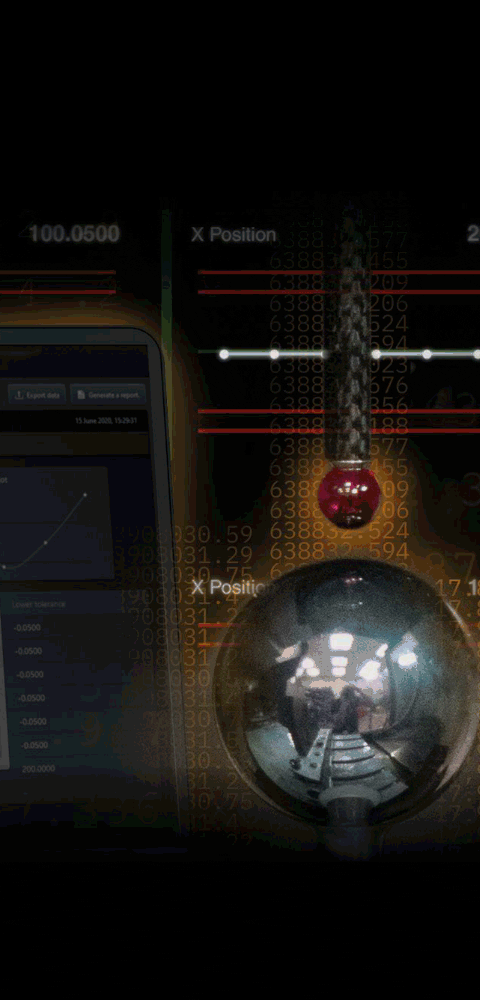
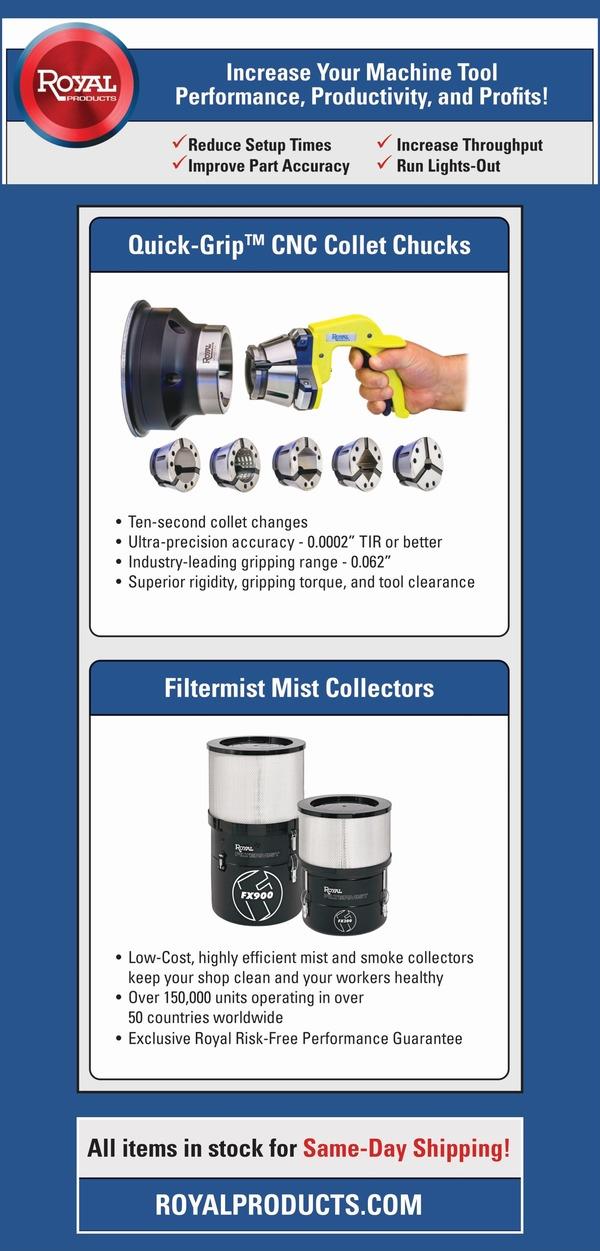
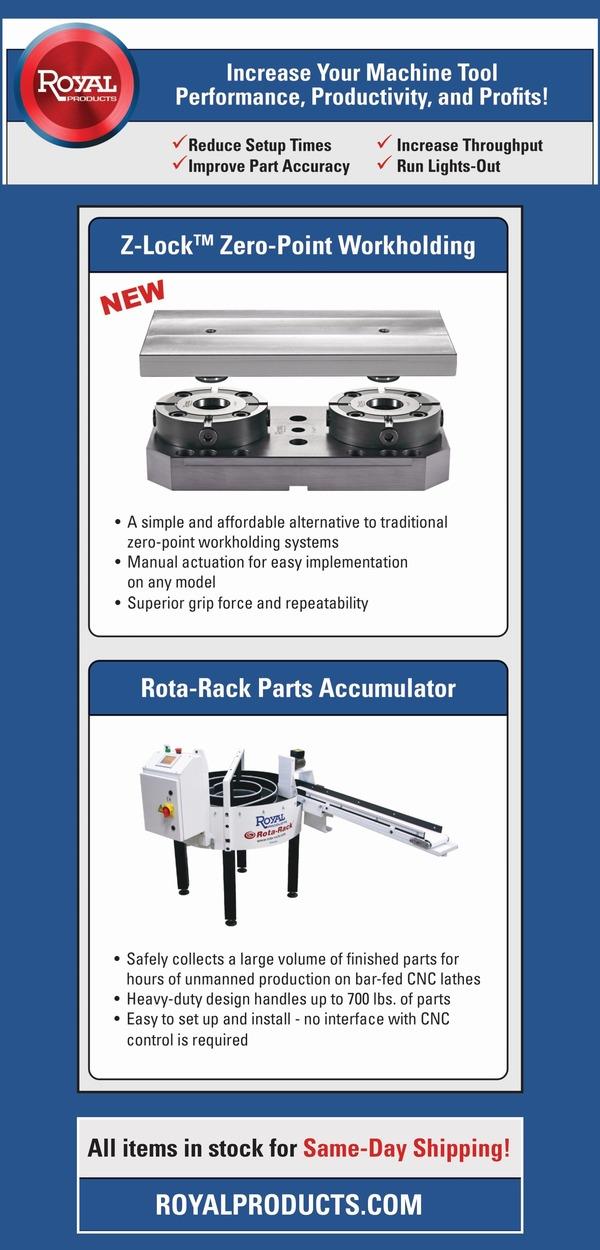
Delcam Illinois to Host Release Seminar
November 4, 2013Delcam Illinois will be hosting a seminar on its latest CAM developments on December 4th at Ingersoll Cutting Tools, 845 S. Lyford Rd., Rockford, IL 61108.
"In this seminar, we will demonstrate the latest version of PowerMILL 2014 plus show a live machining demonstration of Vortex, the new roughing strategy inside both PowerMILL and FeatureCAM," said a company spokesperson. "In the afternoon we will introduce Delcam Electrode, a new electrode solution that guides you seamlessly from design through manufacture to inspection of electrodes, and show you what's new in FeatureCAM 2014."
Vortex, for which Delcam has a patent pending, has been developed specifically to gain the maximum benefit from solid carbide tooling, in particular those designs that can give deeper cuts by using the full flute length as the cutting surface. It can be used for two- and three-axis roughing, three-plus-two-axis area clearance and for rest machining based on stock models or reference toolpaths.
"The strategy will be supplied at no additional charge to FeatureCAM customers on maintenance with the appropriate licenses," said the spokesperson. "Two-axis Vortex functionality will be included for customers that have the FeatureRECOGNITION module, whereas Vortex for Z-level roughing will be able to be used by customers that have the FeatureMILL 3D HSM high-speed machining module. Assuming that they have one of these base products, Vortex can also be used for three-plus-two roughing by users with the positional five-axis programming option and on mill-turn equipment by customers with the FeatureTURNMILL module.
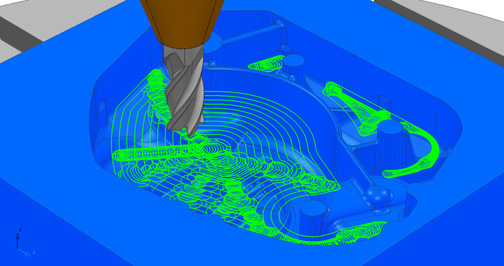
"Like other Delcam roughing strategies, Vortex toolpaths are calculated to give more efficient machining by following the shape of the part and by keeping air moves to a minimum. This is particularly important for rest machining operations. Unlike other high-speed roughing techniques that aim to maintain a constant theoretical metal-removal rate, the Vortex strategy produces toolpaths with a controlled engagement angle for the complete operation. This maintains the optimum cutting conditions for the entire toolpath that would normally be possible only for the straight-line moves. As a result, the cutting time will be shorter, while cutting will be undertaken at a more consistent volume-removal rate and feed rate, so protecting the machine."
Following the demonstrations of the new functionality by Delcam International Engineer Craig Chester, delegates will be given a tour of the Ingersoll production facility. This will include demonstrations of the Vortex strategy with Ingersoll tooling on a Toyoda-Wele AQ1050.
"We very much appreciated the hospitality provided by Ingersoll for our users, especially the opportunity to show the time savings that are possible by using our new Vortex area clearance strategy with Ingersoll cutting tools," commented Mark Cadogan, Vice President Delcam North America. "In addition, I'm certain that our users will welcome a chance to tour the production facility."
For more information contact:
Delcam
877-335-2261
marketing@delcam.com
www.delcam.com
< back