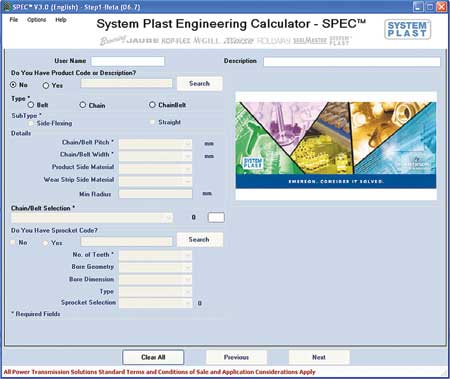
Emerson's SPEC software evaluates applications for steel or plastic chain and modular belt conveyor by validating detailed user specifications with a red, yellow or green rating.
Emerson Industrial Automation's System Plast Engineering Calculator (SPEC) uses built-in intelligence to evaluate applications for steel or plastic chain and modular belt conveyor by validating detailed user specifications with a red, yellow or green rating. Where possible, the software also presents an alternative optimum solution that may reduce energy or lubrication requirements with System Plast's Nolu-S wear material.
The process involves three steps: definition of conveying requirements; application requirements with product specifications; and system layout. Developed by Emerson's Power Transmission Solutions business, SPEC software reports results that include required chain pull, motor speed, torque, shaft power and maximum line back pressure. The software issues alerts for incompatible parameter inputs during the process to help the user achieve successful results. The software covers applications with carbon steel, stainless steel, several types of LF acetal for high-speed/reduced lubrication and New Generation (NG) chain designed for high-speed dry running applications. Wear strip options include stainless steel, UHMW PE and Nolu-S self-lubricating UHMW for low-noise, energy-efficient dry running.
SPEC software is based on Emerson's original SysCalc program, but with upgrades and enhancements. It includes an up-to-date database of System Plast chain/belt and sprockets, and accepts most common product materials or user defined ones. The software can use System Plast product codes, or it automatically determines the correct product code based on customer selected specifications. The software starts by determining the correct chain or belt based on inputs for pitch, width, material for each side of the belt, and radius if side-flexing. User supplied specifications and pull-down options at each point make the process straightforward. Sprockets are selected based on similarly detailed user inputs. Photos and overall dimensions of the recommended products are shown for confirmation.
"SPEC software's strength is its ability to translate the user's input for product and system layout into a specific set of recommended conveyor components," said a company spokesperson. The application definition allows inputs for variances of material, geometry, coefficient of friction, arrangement on the conveyor, type of conveyor lubrication, number of tracks, track pitch, speed, hourly throughput and more. Layout details include length, radii, angle, height, accumulation and product load.
Throughout the process, SPEC software allows the user to return to previous screens to update or change parameters. At the conclusion, the software rates the application as acceptable, marginal or not suitable. A viable alternative solution with Nolu-S wear strips is presented, where appropriate, for unsuitable applications or for those where additional energy and water savings can be accomplished. Nolu-S wear material, when used in conjunction with NG chains and belts, provides the opportunity to reduce lubrication in most applications. Nolu-S also helps reduce noise, energy consumption, squeaking and chain pull/belt fatigue.
SPEC software is free and available in nine languages: Chinese, English, French, German, Italian, Portuguese, Russian, Spanish and Turkish. It can be downloaded from www.powertransmissionsolutions.com.
For more information contact:
Emerson Industrial Automation
8000 West Florissant Avenue
P.O. Box 4100
St. Louis, MO
314-553-2000
industrialautomation@emerson.com
www.emersonindustrial.com