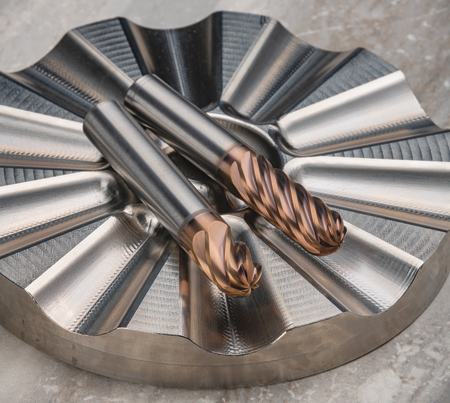
The POW-R-ARC 6-flute roughed this titanium 6AL-4V distributor disc at 3362 RPM, 1/2xD axial depth. The part is 5-1/2" dia. The POW-R-ARC 8-flute provided the finish at over 200 IPM. Cycle time = 13.5 min., end mills are still like new, the company reported.
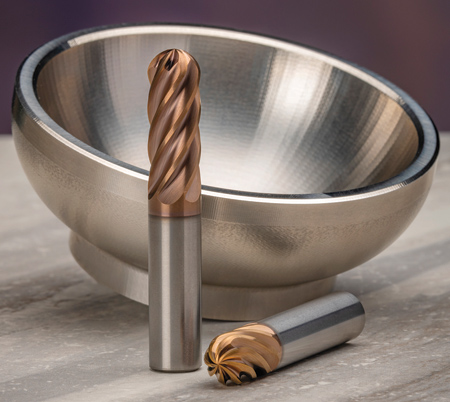
The POW-R-ARC 8-flute did the 3D roughing and semi-finishing on this Inconel 718 deflector bowl in 50 min. at 31 IPM. The same tool completed the finishing at 60.5 IPM and chamfering the rim in just 22 min. total cycle time.
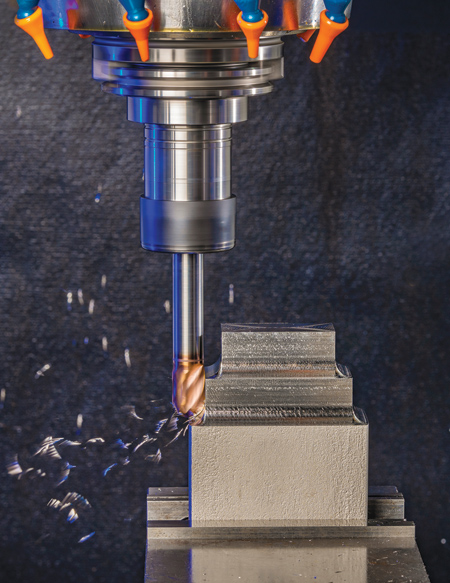
POW-R-ARC A106N (3/4" dia., 6-flute ball end with neck relief and a 3-3/4" LBS) removes stepdown notches left by a corner radius roughing end mill in 316L stainless steel. This semi-finish pass, machining on the tool's sidewall and ball nose, removes .020" from sidewall and radius with minimal notching. One finish pass with the same tool will yield an excellent finish, the company reported.
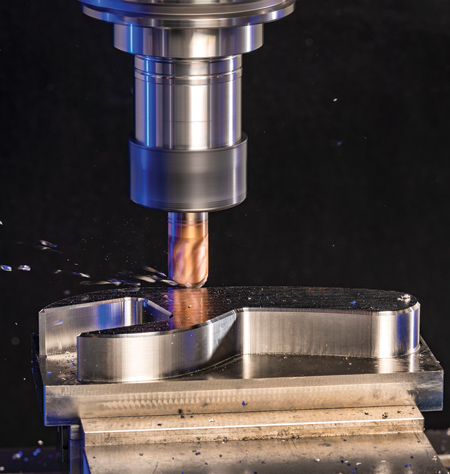
POW-R-ARC A108 (3/4" dia., 8-flute ball end and 1" LOC) machines a .050" perimeter chamfer in 6AL-4V titanium. "Compared with a 4-flute tool, the POW-R-ARC cutter leaves a bur-free finish at incredible speeds," said a spokesperson.
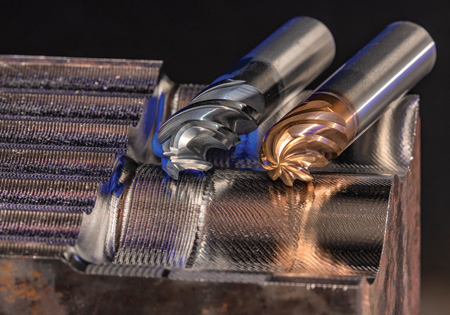
The POW-R-FEED M924B (left, 3/4" dia., 4-flute ball end, 1" LOC) v. the POW-R-ARC A108 (right, 3/4" dia., 8-flute ball end, 1" LOC) Material: A2 at 60 HRc. Using the same stepover value, the POW-R-ARC 8-flute tool provides a better 3D contour cut 5x faster, with barely visible ridges (far right) and little finish work, the company reported.
IMCO Carbide Tool has launched the POW-R-ARC ball-end, high-performance solid carbide cutting tools.
"Designed for 3D contouring and chamfering at fast speed and feedrates, POW-R-ARC cuts and finishes in hardened metals up to 62 HRc, aluminum, stainless steel, low carbon steel and super alloys such as high nickel alloys, cobalt chrome and titanium," said Matt Osburn, Vice President and Technical Director. "We focused on speed and high feedrates, and POW-R-ARC exceeded all expectations."
Available with six or eight flutes, POW-R-ARC cutters feature advanced geometries, free-cutting design and a next-generation coating for faster feedrates, greater lubricity and reliable chip clearance in most materials, the company reported.
"Increasing the flutes from the traditional 4-flute tools to six or eight flutes increases speed and feeds," Osburn said. "Plus, POW-R-ARC provides a great finish with a second pass. So, no stopping to change tools. No need to even stock dedicated finishing tools. And tests show POW-R-ARC lasts much longer."
"In a recent test, a moldmaker was cutting both P20 steel and 4140 low alloy steel using a competitor's tool running at 88 IPM," said a spokesperson. "After eight hours of roughing with the competitor's tool, they threw it away. After 16 hours of semi-roughing and finishing with the competitor's tool, they discarded that tool too.
"Then they tried a POW-R-ARC cutter, running at 450 IPM-nearly five times the speed-and completed roughing and finishing using the same tool. POW-R-ARC cut cycle time by half, from 24 hours (roughing to finishing) to 12 hours, and it more than doubled the tool life; it was still going strong after 32 hours. Just one POW-R-ARC tool did all the work and kept on going."
The POW-R-ARC is engineered to work well in machines with lower-max-speed spindles as well as high RPM machines. The geometry evacuates the chips, reducing the chances of loading up, even at a lower RPM. Long necks can be ordered for working in pockets and around mold guide pins.
POW-R-ARC also is suited for 5-axis machines, with the added number of effective cutting flutes going from the OD all the way to the tip of the tool.
According to Steve Avers, IMCO's Technical Support Manager, even greater savings are seen when cutting across dissimilar materials, which typically requires handwork to eliminate digs where materials meet.
"Molds and dies, medical implants, turbine blades and glass molds often have abutting materials with different characteristics," Avers said. "POW-R-ARC cuts through both materials smoothly, eliminating digs where edges meet. The time-consuming handwork required to remove these digs is gone."
Watch POW-R-ARC work at imcousa.com/video-gallery.
For more information contact:
IMCO Carbide Tool
28170 Cedar Park Blvd.
Perrysburg, OH 43551
800-765-4626
support@imcousa.com
www.imcousa.com