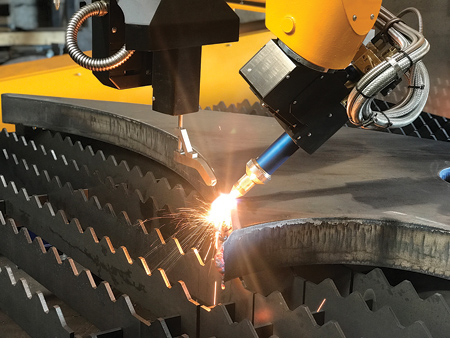
Oxyfuel rotator for weld preparation on thick metals utilizes MicroStep's patented ACTG technology for automatic compensation of kinematic inaccuracies, and thus delivers reliable cutting results in the long run with less frequent maintenance necessary.
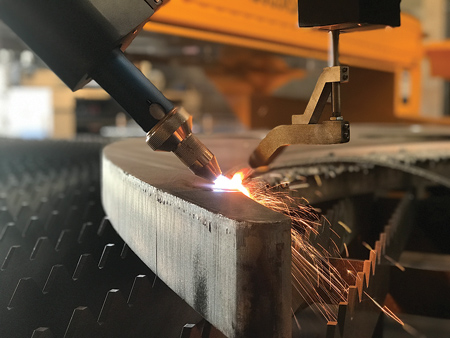
Oxyfuel beveling
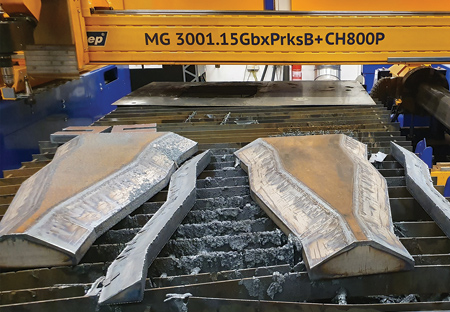
Advantages of additional beveling with oxyfuel: minimum waste, smooth cut surfaces, precise cut contours also for bigger bevel angles, as showcased on the above parts 3.55" thick, Y cut with land size 0.8", bevel angle 60°, cut with MicroStep ABP technology for a South African customer.
The integration of oxyfuel technology in MicroStep's rotary bevel heads creates new application areas especially where complex contours with multiple bevel cuts in larger material thicknesses are required. Paired with innovative solutions such as ACTG and ABP, the new technology proves to be highly efficient and precise.
The efficiency of bevel cutting of thick metals is determined by several factors: energy and gas consumption, wear of consumables (cutting nozzles), cutting speed, the number of cuts needed to achieve the desired cut profile (for X, Y, K cuts), the possible need for additional material handling between individual cuts, and finally, the volume of waste material that does not belong to the final cut part but also degrades in the cutting process
The quality of the cut is determined by the limitations of the technology itself and, in case of thicker materials, by the ability to cut material of a certain thickness at all. A sustainable production technology needs to be well balanced between efficiency (cost) and cut quality.
Limitations of Oxyfuel Triple Torches
In today's industrial applications, there are materials up to a maximum thickness of 2" commonly cut with plasma, utilizing rather high cutting currents of 400 to 450 A. In the case of bevel cutting, applications from 1.4" to 1.6" thickness tend to be the limit for plasma: thicker mild steels are traditionally bevel cut by oxyfuel triple torches, which allow two or three simultaneous cuts, creating Y, X or K cut edges in a single pass.
Triple torch technology has certain drawbacks: the geometry of the torch setup does not allow cutting some types of contours (especially internal beveled edges); the bevel angle is limited to max. 50°; and, overall, the maximum material thickness for bevel cuts is usually limited to 3.15" to 4", making it suitable just for certain applications.
To address these issues, MicroStep integrated an oxyfuel torch into the company's existing rotary bevel head design. This allows them to leverage existing plasma and oxyfuel features.
Introducing the Oxyfuel Rotator
The MicroStep rotator is a 5-axis 3D bevel head with endless rotation and a tilt up to 52° (for plasma torches) that has proven itself in hundreds of installations worldwide. Due to the torch pivot point being aligned with its rotary axis, the design is well suited for cutting a range of bevel shapes, including internal contours, variable bevels as well as multiple bevel contours Y, X or K. For oxyfuel, the head has been modified to include an endless gas transmitter, a tactile height measurement system. Most importantly, the torch tilt was increased to 67°, allowing the generally narrower oxyfuel torch to be used for cutting material at larger angles.
Compared to triple torch cutting, the advantages are obvious: maximum material thickness for direct beveling increased above 4.75" in (depending on application and bevel angle even up to 7.85"), the cut angle increased to a full 0° to 65° range compared to the 20° to 50° range for triple torch. The AC geometry of the bevel head allows significantly smaller cut radiuses on holes and internal contours, e.g., for thick pipe intersections. Furthermore, oxyfuel rotator with an integrated laser scanner can use Additional Beveling Process (ABP), which greatly expands the possibilities of beveling thick sheets on a cutting machine.
Multiple Material and Gas Savings with ABP
With additional beveling the part is first cut straight; afterwards it is taken out of the sheet, placed on a free spot on the cutting table, scanned for exact contour/position and, subsequently, bevel cuts are added to the contour. For oxyfuel, this means that very thick parts (~9.85" to 11.8") can be produced with clean bevels with angles ranging up to 60° to 65° with great savings of gas and material. For Y or K cuts, with ABP the effective bevel cut thickness is significantly smaller compared to direct beveling into a full sheet, which allows operators to cut bevels much faster and with multiple saving of the cutting gas. Higher cutting speeds also mean that there is a smaller heat-effected zone in the material, i.e., better quality of the final part. Any additional part-handling times associated with ABP are offset by having a machine with multiple straight gas torches and using ABP on multiple parts in one sequence.
Finally, with ABP there is no additional material waste from unused bevel cuts. This is because beveling is performed on an already cut contour with no material around it. This presents significant material saving, especially for larger thicknesses and higher bevel angles. Not to mention that, compared to other methods of additional beveling-e.g., using one cutting machine for straight cutting and a separate robot workplace for beveling-the use of one machine for all operations is much more efficient and comes with much lower initial cost. A customer case study has shown that employing a combined MicroStep machine for thick sheet cutting can deliver production time savings of up to 85%.
Authored by United Precision Services
For more information contact:
United Precision Services
11180 Southland Road
Cincinnati, OH 45240
513-851-6900
sales@unitedprecisionservices.com
www.unitedprecisionservices.com